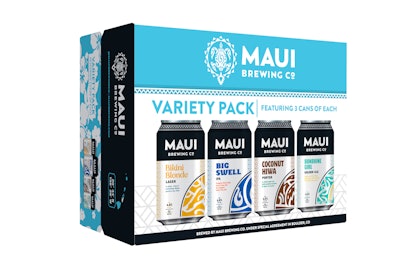
In the 2023 Craft Brew Supplement, Packaging World highlighted Hawaii’s largest craft brewer, Craft ‘Ohana—more widely recognized as Maui Brewing Company (MBC)—and its transition from plastic ring carriers to paperboard cartons for multipacks of its canned beverages. The primary driver was sustainability; plastic ring carriers aren’t recycled in Hawaii, whereas paperboard packaging is. The other was the opportunity for enhanced visibility on-shelf. While the 2023 article explored the why of the change, the how is another story.
![]() | Learn more about Maui’s decision to move to cartons in this related article, “Maui Brewing Ditches Plastic Rings for Paperboard Cartons” |
As Craft ‘Ohana Senior Project Engineer David Brendgard shares, MBC’s journey from ring carriers to cartons took several years, a lot of experimentation, and substantial investments not only in cartoning and tray-packing equipment, but also in an entirely new filling line. “We replaced existing equipment to accommodate what we’re trying to achieve today, and moving from plastic carriers into cartons was the driving factor for that,” Brendgard says. “We basically built this line around the idea that we were going to go into cartons.”
Completed in 2023, the new line has streamlined MBC’s operations significantly, both upstream and downstream. Improvements include an 80% increase in MBC’s filling speeds, the flexibility to add new can sizes, quick changeover of different beverage types with automatic CIP (clean-in-place) capabilities, and the ability to produce four-, six-, 12-, and 24-ct cartons, including variety packs—a new and very popular product for MBC.
Local ingredients set Maui’s brews apart
Maui Brewing was founded in 2005 by CEO Garrett Marrero and COO Melanie Oxley in Kahana, Maui, where it operated a 10-barrel brewhouse—in layman’s terms, a brewery with the capacity to produce 10 barrels or 310 gal of beer in a single batch. In 2014, the brewery moved to its current location in Kihei, Maui, where it now makes a range of beverage brands. These include Maui Brewing Co. beer in year-round and limited-edition varieties, Island Soda craft sodas, Maui Hard Seltzer seltzers and teas, and Kupu Spirits, which include bottled spirits and RTD canned cocktails.
Differentiating MBC’s products is its use of locally sourced ingredients. “One of our most popular beers is our Pineapple Mana Wheat, which uses pineapples grown here on Maui,” shares Brendgard. “A lot of our specialty beers are brewed with local products, whether it’s hibiscus or lilikoi [passion fruit] or limes, that are grown here on the island. We try to do that as much as possible to support our local industry.
“Another thing that distinguishes us is that we are the largest craft brewery in the state of Hawaii. We thrive on providing our beer to the tourist industry by getting it into the resorts, restaurants, chain stores, and C-stores throughout the islands, so when visitors come to Hawaii, our product is in the forefront.”
Many of MBC’s specialty beers are brewed with local ingredients.
“Ideally, we’d like to brew our own beer on the mainland, with Modern Times being included in that,” explains Brendgard. “We feel the product is fresher for the consumer and more reliable when it’s brewed closer to the point of consumption.”
In the meantime, Kihei is still the main production hub for MBC’s range of beverages, with a capacity of 70,000 barrels of product per year, which the company is working to grow to 120,000. All of its canned beverages are produced on a single line at the Kihei facility; a separate line handles beer in kegs for draft sales. MBC uses one can size, a 206, or 12-oz, aluminum can, supplied by Ball Corp. out of Honolulu, Hawaii.
COVID yields unexpected benefit
As Brendgard explains, it was shortly before COVID that MBC began experimenting with the use of cartons rather than plastic carriers for its multipacks. When the pandemic hit, the brewery saw its canned beverage business increase, while sales of its beer in kegs came to a halt. “So we focused entirely on our canning line and how to get those products out,” Brendgard explains.
Throughout the pandemic, MBC used an entry-level cartoner from DMM Packaging to experiment with different carton sizes for its multipacks, including new mix packs, or variety packs, of its beverages. “We found that the mix packs were a very sellable product for us,” says Brendgard. “Visitors to our islands have fewer reservations about buying a case with three or four different varieties than buying a whole case of a single brand.”
It was the success of the mix packs that motivated MBC to upgrade to a more sophisticated cartoner from WestRock, and it was the new cartoner, in turn, that galvanized the brewer to completely replace its existing line, building a new one around the cartoner for maximum efficiency. It took a year for MBC, with the help of A&E Conveyor, to design the new line, which ultimately required the addition of a mezzanine to accommodate all the new equipment.
Carton blanks are stacked at the ready in the WestRock cartoner for mix packs of beer.
MBC’s secondary packaging capabilities include the new WestRock cartoner, a WestRock tray former, and a Hamrick drop-pack case/tray packer. After cans are filled on the ground level, they are transported to the mezzanine level with an overhead conveyor/accumulation system. While the tray former erects the trays, the cartoner loads four, six, 12, or 24 cans into the cartons, after which the cartons are placed into the case trays via the Hamrick drop packer. The filled trays, comprising either six four packs, four six packs, two 12 packs, or one 24 pack, are then conveyed back to the ground level on an AmbaFlex spiral conveyor and then palletized.
A four-axis robot with two end effectors picks up 48 cans, with each vacuum head picking up 24 cans, each head handling a different variety, and placing them on a conveyor leading to the cartoner.
Ever conscious of responsible use of packaging materials, MBC uses the same case trays that hold the loose cans to hold the mix packs. After the robots pick the 24 loose cans from each tray, they move the empty trays to another AmbaFlex spiral conveyor that leads to the mezzanine, where they are used for the mix packs. Finished products are transported back to the ground floor by the spiral conveyor and once there, into an FL3000 floor-level palletizer from Columbia, where 100 trays are stacked on a pallet, and the pallet is stretch wrapped.
New filler is fast and flexible
The cornerstone of the new packaging line is a 44-valve can filler from Krones. In specifying a new filler, MBC was looking for a system that could increase its speed by at least 15%. It also wanted to be able to run different can sizes, such as 16 and 19.2 oz, in the future.
As Brendgard explains, the only can size Ball offers out of its Honolulu plant is a 206, or a 12-oz, size, so MBC will have to source other sizes from the mainland. In the U.S., a 12-oz can is a 202. “So the requirement we had for the filler was that it could swap out between a 202 and a 206 can size, which is the diameter for the lid, and the different volume sizes.”
The new Krones filler operates at 550 cans/min, which is 80% faster than MBC’s previous equipment, and can accommodate can sizes other than the 202 12-oz. It also includes a CIP system that cleans both the interior and the exterior of the machine. Foaming heads on the filling valves ensure sanitation when changing between beverage types. “If you’re going from beer to soda, or vice versa, depending on the sugar content or the alcohol content, you have to make sure the filler is 100% clean so you won’t cross contaminate the next product,” says Brendgard.
![]() | Read this related article on Voodoo Brewing Co., “Canning Line Upgrade Keeps Franchisees Fed” |
“Our previous system required a lot more manual cleaning, for sure. You really had to get in there with the hand brush and scrub,” he adds. “We’ll still need to do that, that never goes away, but it will make it a lot easier for the operator at the end of the day with CIP to make sure the machine is 100% clean.”
Another feature of Krones’ equipment that made it the best choice for MBC was its ease of use which is particularly important due to the brewery’s island location. Bringing a technician from Krones to the plant either from Germany or the U.S. mainland causes numerous days of shutdowns.
Finished product, comprising filled cartons in case trays, are conveyed back to the main floor of the facility for palletizing.
“Krones fillers are remarkably easy to use,” says Brendgard. “The complexity comes down to changeparts and repair and maintenance.” For this, he explains, MBC has trained its operators and maintenance department on valve rebuilding and on preventative maintenance for the filler and seamer. “We want to train our maintenance department and our operators to be highly specialized, so we don’t have to bring in techs from outside,” he says. “So training is very important to us, not only for the education of our employees, but also so that we have on-site service.”
The Krones filler is housed along with a six-head Ferrum sealer in a cleanroom enclosure on the ground floor. One option MBC added to the new line is a CSW (Can Systems Worldwide) lid feeder. “With our previous machine, every one and a half minutes we’d have to add a new roll of lids,” says Brendgard. “With the CSW lid feeder, we can run the machine a full hour without having to add more lids. This allows the operator to pay more attention to the actual filling process, rather than stocking up on lids.”
CSW also added a Filtec inspection and sampling system. The system provides valve monitoring to advise the operator when a valve is constantly hitting a low fill or an overfill, for example. “It also makes sampling much more convenient,” Brendgard says. “If you have a rebuilt valve, you can say, ‘Give me the next 10 cans off this specific valve,’ and it will pop those off for you.”
Final pieces put in place
Rounding out the new packaging line are a number of other new machines. At the beginning of the line is a depalletizer from Ska Fabricating that removes the preprinted aluminum cans from bulk pallets onto a conveyor. The cans are then flipped upside down and rinsed with an ion air rinser before they are filled and seamed.
Following filling and seaming, MBC installed a can warmer. As Brendgard explains, cans are filled at 33°F, so when they exit the filler, they begin to sweat immediately due to the high heat and humidity of Maui. “We found that if we place them directly into the cartons, the cartons get ruined,” he says. “So we installed a PRO Engineering can warmer to bring those cans just above dew point so they don’t sweat as they’re going into the cartons.”
![]() | Interested in learning more about cartoning technologies? Read more in this curated collection of cartoning case studies. |
MBC also added an Accutek labeler, which is used when the brewery creates short-run limited-edition offerings using blank cans. “But the majority of our product will be printed cans,” Brendgard notes.
Using a phased approach to installing the new cartoning capabilities and filling line, MBC’s new packaging line was completely up and running by year-end 2023. According to Brendgard, the new line has met all of MBC’s expectations. PW