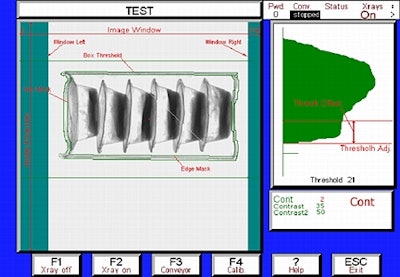
For example:
· Your product has a naturally occurring defect such as bones in meat requiring its identification and removal.
· You have experienced occasional contamination problems with metal fragments in your product and conventional metal detectors are unable to detect them.
· Your product comes in glass jars and your customers are finding chips of glass dislodged by automatic lid sealing equipment.
· Missing product pieces.
Because of your commitment to quality the high cost of handling consumer complaints and the threat of potential lawsuits you are seeking solutions to contamination problems before they become costly.
You've heard of X-ray inspection and now you're asking: is X-ray the solution to my problem?
Any product can be inspected with X-rays. Whether or not the inspection is successful however depends upon the product the defect and the limitations of the technology.
We have designed this article to help you determine whether your application meets the criteria and help you decide if X-ray inspection is the solution you are seeking.
What are X-rays? How do they work?
X-rays are a form of electromagnetic radiation (as are microwaves radio waves ultraviolet and visible light) which were discovered to have an exceptionally useful property: X-rays pass through matter at a predictable rate. This property opened up a world of applications and in many ways revolutionized science and industry.
It was discovered that a specimen placed between a source of X-rays and an X-ray sensitive receiver such as photographic film resulted in a picture of the interior of the specimen. X-rays passing through the specimen are stopped by matter in the specimen at an I-rate which corresponds to the relative density of the specimen. The denser the specimen the fewer X-rays reach the receiver. In this way X-rays allow us to "see" inside opaque objects.
How are X-rays produced?
For most industrial and scientific applications X-rays are generated with a device called an X-ray tube head.
Electricity is applied to a filament which emits electrons that stream towards an anode which is embedded with an angled tungsten plate. When electrons bombard the plate two things are produced: heat which is siphoned off by means of a cooling system; and X-rays. X-ray tube heads are especially useful because of safety considerations. Since they don't rely on radioactive isotopes to produce X-rays tube heads are completely inert and therefore safe to handle when power is not applied to them.
Because the high amount of heat produced could otherwise reduce the life of the tube head a small network of pipes is welded to the back of the tungsten plate and oil or water is pumped through them to take away the heat. This provides the cooling necessary to extend the life of the tube head.
How do X-ray inspection Machines Work?
For most X-ray inspection systems the basic principle of operation conveys the product between an X-ray tube head and a receiver (usually a solid state linear array of Xray sensitive photo diodes). The photo diodes detect the level of X-rays which pass through the product to generate picture elements (pixels) which correspond to levels of gray between '0' (no X- rays detected) and '255' (maximum Xrays detected). The pixels are then combined line-by-line into a coherent image which is either analyzed by a human operator monitoring the image on a video screen or a built-in computer designed for this purpose.
Evaluating the X-ray image: Recognition systems
Once an image of a product is acquired it needs to be analyzed for the presence of defects. Two basic methods are available: visual which utilizes a human operator to make decisions and automatic which utilizes computer hardware and software to make decisions. Three systems are available with our X-ray inspection equipment. These include visual recognition and two types of automatic detection: density threshold and morphology processing.
Visual Recognition
With a visual recognition system a human operator monitors a video screen on which the image is displayed when acquired by the X-ray unit. Upon detection of a defect the operator initiates a rejection sequence.
Strengths: Because it relies on the fastest most efficient computer known the human brain to make decisions visual recognition systems can be very effective at finding unusually shaped items small defects or analyzing particularly complex images. Additionally because of their minimal hardware requirements visual recognition systems tend to cost less than their automated counterparts.
Weaknesses: Humans can be costly to train and are subject to lapses in concentration fatigue or other distractions that can affect the overall performance of the system.
Examples of appropriate products:
· Cooked and stripped chicken.
· Beef or pork roasts.
· Packaged product where the density of defect is similar to the density of the product.
· Any large irregularly-shaped discrete product.
Automatic Density Threshold
Density Threshold requires an operator to set a density threshold above which indicates the presence of a defect. If the computer detects a density level above this threshold a rejection sequence is initiated.
Strengths: Products such as formed patties or bulk applications such as nuts are ideal for density threshold because their consistent thickness and density rarely causes false detection from the product itself.
Weaknesses: The most significant limitation of a threshold image recognition system is that products which naturally vary in thickness or in density cannot be reliably screened by it. With such products natural variances in product thickness or in packaging density can trigger false detection.
Examples of appropriate products:
* Dried beans or nuts.
* Formed chicken or beef patties.
* Any bulk product or any discrete product with a consistent thickness and density.
Automatic Morphology Processing
For products unsuitable for density threshold a combination of hardware and software known as morphology processing is available. Unlike Density Thresholding which analyzes the image line-by-line morphology considers the image as a whole. By submitting an acquired image to several different enhancement procedures the morphology processor accounts for natural variations in thickness or density and eliminates packaging from consideration as well.
Strengths: It can detect contaminants inside packaged products as well as contaminants in products which naturally vary in thickness or density.
Weaknesses: Since each image enhancement procedure requires a finite processing time the speed with which the system can reliably detect contaminants is limited by the speed of the computer. For some applications maximum throughput with a morphology processor may be too low.
Examples of appropriate products:
* Product in jars or cans.
* Any discrete product with inconsistent thickness or density.
* Any packaged product.
Eliminating the defects: Reject systems
Because there are so many products that can be scanned by X-ray inspection systems reject systems vary according to application.
They include:
* Single-action pneumatic push which rejects products off of the side of the belt
* Multi-lane drop flaps ideal for patties
* Air ejectors ideal for dry bulk products like nuts
Additionally our equipment has the capacity to incorporate customized reject system designs. If your application requires a special reject system not currently offered we may be able to design one.
Evaluating X-ray inspection for your application
In evaluating the suitability of X-ray inspection for your application consider the product the defect and the throughput. Each of these is important in its own right yet must also be evaluated with respect to one another.
Is the product suitable?
A product suitable for X-ray inspection must be able to be transported across the machine. Carefully consider the size of the machine - belt clearance for belt machines maximum and minimum jar sizes for jar inspection units etc. - when evaluating your product. Obviously products too large to fit through the machine or too small to be resolved by the image processor are unsuitable for X-ray inspection.
Additionally consider the method of product transportation. Liquids and slurries can be inspected prior to packaging on pipe machines and can be inspected within their packages on jar inspection machines. Dry bulk product like nuts or berries can be inspected on belt machines either directly on-belt in a continuous stream with machines equipped with density threshold or in individual trays on machines equipped with visual or morphology processing. X-ray inspection system manufacturers are aware of the tremendous potential for their technology and are constantly developing new ways to handle products which had previously been thought impractical to inspect using X-ray.
What are the defects?
X-ray inspection systems detect differences in density and identify defects which differ in density from the product itself.
Complicating matters is that every individual product (as well as every defect) has its own "density profile" which incorporates product thickness as well as density. Products that naturally vary in thickness or which are packaged in a high-density material have a "good product" density profile which covers a broad range. Defects which fall within this good product density range can be difficult to detect. The size of the defect is an important consideration as well. X-ray systems have a finite resolution --defects which are too small can not be detected.
Regardless of the size or shape of the defect its suitability for detection is always evaluated with respect to the product. Since Xray systems detect density differences the density of the defect with respect to that of the product is a significant factor in determining defect suitability. For instance chicken skin and chicken meat differ slightly in density. Their density relative to one another however is too small to result in reliable detection by an X-ray inspection system. For this reason alone it is best to arrange for an application test with an X-ray inspection system manufacturer before determining whether or not a defect can be detected by X-rays.
What is the required throughput?
While the concept of using X-rays to inspect food is relatively simple image processing -- automated or visual -- is a complicated endeavor. It takes several seconds for example for a trained human operator to thoroughly inspect an image on a video monitor for the presence of defects. Similarly finite computer processing time limits the speed with which an automatic recognition system can inspect an acquired image. In both instances maximum system throughput is limited by image processing time.
Additionally throughput is affected by product handling considerations. Discrete product for instance must be inspected item-byitem lowering the maximum through-put as compared to that for bulk product which is inspected in a continuous stream.
Safety. An important consideration
For any application involving X-rays safety is a necessary concern. We have taken several steps to ensure the safety of operators of our equipment:
* All of our X-ray systems use low energy X-rays contained within a high-grade stainless steel cabinet designed to prevent any leakage.
* X-rays are generated only when power is applied to the X-ray tube head. No radioactive isotopes are used in the system.
* Numerous safety interlock systems have been integrated into the system design to prevent the unit from being opened while X-rays are generated. If an attempt is made to open the machine while it is in use power is immediately severed to the X-ray tube head.
With regards to applications for the inspection of food:
* Food directly exposed to the X-ray beam receives a maximum dose equivalent to one-fifth of the recommended maximum dose uptake for food as endorsed by a 1990 World Health Organization memorandum.
* The U.S.D.A. has approved similar equipment for use in federally-inspected meat and poultry plants.
With regards to government registration of X-ray systems each country and individual states have their own specific registration requirements. It is our policy to work closely with our customers and any regulatory agencies to ensure complete compliance with all rules and regulations.
Application testing: The best way to get the answers you need
As you can see determining the suitability of a particular application is a complicated process which takes into account several specific factors. For this reason application testing is an essential part of the decision-making process. We will be happy to arrange a test for product and defect suitability and will provide you with throughput parameters of their machines with respect to your application. We can also help design customized product handling systems and can recommend appropriate reject mechanisms for your application.
Summary
X-ray food inspection is a relatively new technology with hundreds of promising applications. As a tool for reducing levels of all types of contaminants from merely undesirable to potentially dangerous X-ray inspection provides excellent quality control assurances able to reduce costs and potential liability.
About Safeline
Since its formation in 1988 SAFELINE has become the largest metal detection manufacturer in the world with operations in the U.K. U.S.A. and Europe with over 30 years of design and manufacturing experience supporting a worldwide distribution network.
You will find SAFELINE metal detectors reliably and effectively eliminating all types of metal contamination from foods destined for the global marketplace.
All Safeline Detectors offer advanced microprocessor-based technology incorporating digital-signal processing. Automatic setup Balance Control and optimized detection standards are integrated into all SAFELINE units to minimize false rejects while maximizing durability and operator productivity.
SAFELINE's newest technology offering the ClearView Intelligent Inspection System combines high-resolution low energy X-ray technology with innovative hardware and high-performance image processing software. ClearView systems can be configured to inspect for:
· Product Count
· Product Mass
· Container Fill Level
· Broken or Damaged Product or Packaging
· Presence of Package Inserts
· Contaminants (including metal stone glass bone and certain plastics)
· Product Attributes (to ensure optimum quality)
For more information:
Telephone: 800/447-4439 or 813/889-9500
Email: [email protected]
E-Quotes on the WEB: www.metaldetection.com
[This advertorial originally appeared in Packworld.com's supplier-sponsored content area.]