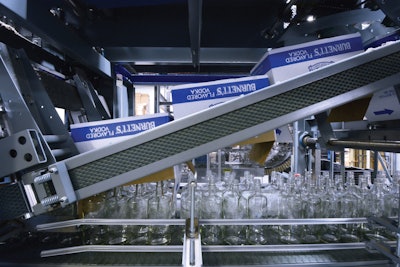
A twin-bowl gravity filling machine at the Bardstown, KY, facility of Heaven Hill Distilleries has made it possible to boost filling speeds from 180 to 220 glass bottles/min.
“It was time,” says Mike Monroe, Manufacturing Maintenance Manager, when asked why the new machine was installed. “Not only was the previous filler over 20 years old, it didn’t have an integrated capper. The capper was downstream, so we had some problems with splash and inconsistent fill levels. With this new filler we gain not just speed but accuracy to within 1⁄32 of an inch.”
Supplied by Fogg Filler Co., the Twin F6 Filler has two six-foot-diameter bowls each feeding 36 valves. It’s capable of 280 bottles/min, but limitations on other machines on the line make 220 the top speed at Heaven Hill.
“We believe we’re the first to install one of these twin-bowl systems,” says Monroe. “Our specific requirements made this a perfect fit for us.”
The requirements to which he refers have a lot to do with desired speed, narrow bottle necks, and a lack of available real estate in the plant. Increasing filling speeds to the 220/min mark was essential as new fillers were explored. But getting there with a conventional single-bowl filler is problematic because many of the glass bottles being filled have a long neck and a narrow internal diameter. This limits the size of the valve that can be used, and regardless of how big the valve is the flow of liquid is always somewhat choked off.
Also a factor is that some of the Heaven Hill spirits have considerable sugar content, which means there’s some foaming that takes place. “With a twin bowl approach,” says Monroe, “once we do half or two-thirds of the fill on the first bowl, the bottles then pass through a series of star wheel exchanges before they reach the second bowl. During this time, the foam has a chance to settle.”
But of all the requirements at Heaven Hill that made the double bowl filler a good fit, the system’s relatively small footprint was the most important. “A single-bowl filler with 72 valves would have been too wide,” says Monroe. The Fogg system measures 11’ 8’’ W, 25’ 2” L, and 11’ 4” H.
CIP IS ATTRACTIVE
Monroe also likes the fact that Fogg, with so much background in the dairy industry, has such thorough Clean-In-Place capabilities. Finally, he adds, the machine is rugged. “It just runs and runs,” he says. “For distilled spirits like what we produce, having the most sophisticated technology in the world is not what counts. You just want something that’s rugged, something that runs.”
Bottle sizes filled in the line include 700-mL, 750-mL, and 1-L, and they come in a variety of configurations, including square and round. Supplied primarily by Ardagh and Berlin, the bottles arrive in corrugated re-shippers.
“It would be difficult for us to handle bulk glass on pallets because our product mix is so diverse,” says Monroe. “Some lines have several different bottles in a number of shapes and configurations. Changeover might be twice per shift, as our orders can be as small as 100 cases. We sacrifice some efficiency operating like that, but that’s just the nature of the business. Fortunately, one thing about this filler is that once you have the change parts in place, you hit the green button and it runs immediately. There’s no tweaking needed.”
UNCASER
Also added to the Bardstown plant along with the new filler was a Model 49 decaser from A-B-C Packaging. “They’ve been doing it longer than just about anybody out there, and we already have several of them,” says Monroe when asked why A-B-C was selected. The machine picks 12 bottles per cycle from a corrugated reshipper and places them on the conveyor leading to the filler. Running at about 21 cases/min, the machine has all the capacity needed.
Conveyor connections, including the single-filing system just ahead of the Fogg filler, were part of the upgrade, too, and these came from Sentry Equipment. That firm also handled integration responsibilities.
Capping is also part of the Fogg machine, as it includes an integrated 12-head capper. The 28-mm injection molded caps come from Berry Plastics and Closure Systems International.
Pressure-sensitive labels applied to bottles can be either film or paper, depending on the brand that’s in production. A Master Modular Labeler from P.E. Labellers is used for labeling. Depending on the brand, labels might go on front, back, and neck. The modular label stations are a big help, says Monroe. “We try to run nonstop, so a backup label station can take over when one runs out. Then the operator reloads the empty one.”
Downstream from the filling system, a Hartness International Global Laner orients the bottles for their entry into a Standard-Knapp drop packer.
The next big upgrade planned for the Bardstown plant, says Monroe, is in the area of palletizing. Six new Model SPLX high-level palletizers from Von Gal, a brand of Premier Tech Chronos, were scheduled for installation early this summer.
All photos by Jacob Zimmer