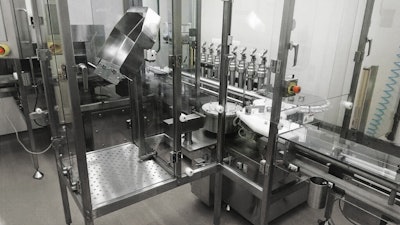
Allergy Laboratories, Inc. was established in 1929 in Oklahoma City for the manufacture of allergenic extracts needed to support the growing immunotherapy practice of founder Dr. Raymond Balyeat. Allergy Labs, as the company is more widely known, has since evolved into an FDA-licensed pharmaceutical manufacturer of more than 500 different biological extracts for the diagnostic testing and therapeutic treatment of allergies. Additional manufacturing and supply capabilities have been added over the years, including a parenteral production facility for contract manufacturing.
According to Allergy Labs, customer satisfaction is of utmost importance. “Every customer is a part of the business, not an outsider or a statistic,” it says. As part of this commitment, the company has dedicated itself to affordable products, excellent customer service, and high-quality, strictly controlled manufacturing practices for the production of sterile depyrogenated vials, sterile diluent, and injectable drugs.
In 2010, Allergy Labs turned to Bosch Packaging Technology – Business Unit Pharma for a new filling and closing machine for vials and infusion bottles. To satisfy Allergy Lab’s needs, two main requirements had to be fulfilled. First, the line needed to operate with peristaltic pump technology, and second, it had to fit exactly into the space that had become available when an existing machine was decommissioned.
Peristaltic pumps offer advantages
In recent years, the popularity of peristaltic pumps for the filling of liquid pharmaceuticals has grown. While initially used for small pharmaceutical batches, today the technology is a viable alternative to conventional filling systems for production-scale operations. Advantages of peristaltic pump technology include the elimination of cross contamination of product with exposed pump components, as pumped fluid only comes in contact with the inside surface of the system’s tubing; low maintenance, due to a lack of valves, seals, and glands; and precise filling tolerances, resulting from the technology’s low-pulsation volumetric flow.
“We work with piston pump technology on another line, which can lead to cleaning and maintenance difficulties,” says Lee Beaver, Director of Manufacturing at Allergy Labs. “So we started looking for a filling and closing machine that operates with peristaltic pump technology. We checked the market, and Bosch has a good reputation for this kind of technology.”
According to Bosch Business Development Manager Jamie Schroetter, among the other requirements for the new equipment were high throughput and efficiency. “A machine that was easy to change over was important, and once the machine was up and running, it was crucial for Allergy Labs to have an efficient run,” he says. “Because it was replacing an existing piece of equipment, machine layout and fitment were also important. Being able to adjust the Bosch machine to the existing footprint aided in making the change less costly and reduced downtime for the aseptic fill suite.”
For its operations, Allergy Labs selected the FLC 3080 filling and closing system, equipped with peristaltic pump technology. According to Bosch, its peristaltic pump combines the advantages of the traditional peristaltic concept with optimized dosing accuracy and a flexible operating concept. “With the mechanical design, we developed proprietary tubing that significantly reduces the ‘drift,’ or changes in fill volume due to tubing changes, that other technologies are known for,” explains Schroetter. The new tubing also makes the technology suitable for a range of filling operations.
Bosch adds that the offset alignment of the rollers reduces mechanical strain on the tubing and permits longer periods of use, making product and batch changeovers easier, faster, and safer. The pump can be opened and closed in two steps without removing any parts. The operator can open the pump with one hand, change the tubing, and close the pump again, saving time and increasing safety.
Allergy Labs primarily uses the Bosch filling and closing line for water-based, easily soluble products such as injectable, sterile drugs. The peristaltic pump is suited for filling volumes of 0.1 to 30 mL, and can be modified to handle even smaller sizes. “Allergy Labs operates with two-milliliter fills, so filling accuracy was a big concern for us. But Bosch met all of our specifications,” Beaver explains. “Filling operations are drip-free, and the single-use components significantly contribute to clean handling.”
Multiple improvements
The filling and closing line selected by Allergy Labs, the FLC 3080, is designed to fill, sample check-weigh, and stopper vials in a continuous-motion process at 200 containers/min. The FLC 3080 uses a vacuum star wheel to accurately position each vial for capping. Additional features include a “V-cleat” conveyor system that enables users to run different-size vials without changing parts. The linear conveyor system runs horizontally in continuous motion. The containers are carried freely in the laminar-flow stream in an upright position. “The FLC line not only provides the cleanliness we require for our filling operations, but it also handles the vials very gently,” says Beaver.
On Allergy Labs’ FLC 3080, the peristaltic pumps and a disposable tubing system are fully integrated with the machine’s control system, drive, and controllers. An integrated touchscreen ensures easy and automated operations. “At first, we were skeptical about the degree of automation of the FLC, but its setup was easy. Our operators quickly adapted to it, and it’s pretty much maintenance-free,” Beaver explains.
Since the new equipment was installed, Beaver says that Allergy Labs has seen improvements in its efficiency, speed, and product safety. “Quick changeover means less downtime,” he says. “We have also seen a 60-percent increase in speed over our previous fill machine.
“Contamination from stainless-steel particles is currently a hot topic within the pharmaceutical industry. With peristaltic pumps, we eliminated pump contact to product, therefore mitigating potential stainless-steel particulate within the product.”