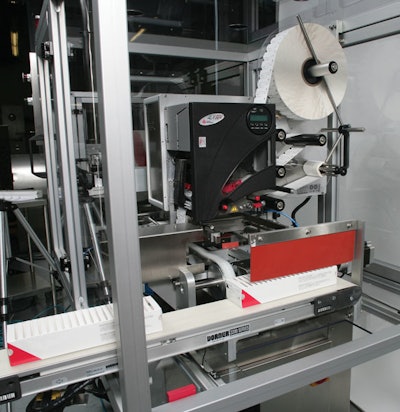
I needed a controls system that could match our requirements for extreme precision and flawless timing.”
That’s how Jerry Wierciszewski, owner of Wierciszewski Controls, describes the requirements leading to his recent decision to select a CP7202 Panel PC from Beckhoff (www.beckhoff.com) to serve as the controls centerpiece of a packaging and inspection system for an unnamed medical products manufacturer that makes blood-testing cassettes. But to understand the functionality delivered by the controls package, it’s best to know a little bit about the product being packaged and the sequence of specialized machines included in the packaging line.
The product being handled by Wierciszewski’s packaging system is a thermoformed plastic cassette used in clinical and diagnostic settings around the world for conducting blood tests. Each cassette holds six tube-shaped cavities. These cavities are filled and the entire cassette is sealed in an operation immediately upstream from what we’re focused on in this discussion. Held in each cavity is a mix of glass beads and fluid reagent. By adding a drop of blood to a cavity, the contents react in a way that answers certain questions about the blood being tested.
The medical products manufacturer producing these cassettes tasked Wierciszewski Controls with designing and building two machines. One machine is a tray erector that sets up paperboard trays into which 20 six-count cassettes are inserted. Between tray erection and before insertion of cassettes is a thermal-transfer print-and-apply unit from Avery Dennison (www.averydennison.com). It imprints a paper pressure-sensitive label with lot number, expiration date, and human-readable serial number. It then applies the label to the paperboard tray and discharges the trays on a Dorner (www.dornerconveyors.com) conveyor in the direction of the machine that fills the trays with cassettes. Also integrated into this section of the packaging operation is vision inspection system #1 to ensure there are no problems with the positioning, accuracy, or legibility of the information printed on the label.
The other machine designed and built by Wierciszewski Controls is an accumulation table that’s 4 feet square, holds 600 cassettes at a time in stainless-steel slots, and has a throughput of 80 cassettes/min. Integrated into the infeed section of the accumulation table is vision inspection system #2. It checks for fill levels in cassette cavities and inspects expiration dates, and it sends a reject signal if a fill level is off or an expiration date is not clearly printed.
Cassettes enter the accumulation table on a belt conveyor equipped with side rails that keep the cassettes standing upright. The accumulation table is essentially a series of stainless steel slots that advance in a direction perpendicular to the direction in which cassettes are fed in. As soon as 20 cassettes are hanging suspended from a slot, the table advances one position and cassettes start filling the next row.
At the opposite or discharge end of the accumulation table, each row of cassettes is sent out of its slot at a right angle and is conveyed to a star wheel that feeds cassettes beneath a flighted belt. It pushes the cassettes forward on a conveyor belt, past vision inspection system #3, and subsequently inserts them into a puck with 20 slots. When the 20th slot of the puck is filled, the puck advances to a station where all 20 cartridges are pushed out of their pucks and into a slotted mechanical device that gently lowers them into the paperboard trays waiting below.
Why the need for an accumulation table? Because the ratio of glass beads to fluid reagent in each cassette cavity can only be checked by vision inspection system #3 if the beads and fluid have had eight minutes to settle. The accumulation system provides this needed period of time.
Computing power required
Now back to the controls package that we set out to explore in the first place. Among the challenges it needs to address is that it must have enormous computing power in order to cope with all the data produced by three separate vision inspection systems: one checking labels at the tray erector discharge, one checking filled cartridges at the infeed of the accumulation table, and one checking the ratio of glass beads to fluid reagent just before the filled cartridges are placed in their trays.
“The communication speed between vision inspection to HMI and to the PLC can be a real bottleneck,” says Wierciszewski. “It’s difficult to pass the results back and forth to a traditional PLC fast enough and respond with the required control functions.”
Other controls challenges are at the tray erector and the accumulation table. Though the manufacturer always orders paperboard having the identical caliper and paper weight, minor variations from batch to batch are difficult to rule out. If there are materials changes, the timing to bend the flaps, fold the paperboard, and glue the flaps must change accordingly. And at the accumulation table, timing must be very tightly controlled as the filled cassettes move through the system or else the glass beads and fluid reagent won’t settle out as they are supposed to. This kind of control requires complex handshaking between motors and the control system.
In addition, the FDA requires rigorous electronic record keeping for all biotech companies, medical device manufacturers, and drug makers. So this system for labeling and packaging blood-test cassettes needed an SQL database for audit trails and detailed tracking for CFR 21 part 11 compliance. All changes in production must be kept track of and must be reflected in detailed reports that can verify regulatory compliance. “Who logged in, when did they log in, what’s the expiration date and lot number, who initialized the lot, who terminated the lot—all these things must be kept electronically, and it takes some computing power to do it,” says Wierciszewski.
To address these challenging requirements, Wierciszewski selected as his controls centerpiece the Beckhoff Automation Panel PC, a CP7202 with 15-inch touch screen that handles all automation, motion control, SQL database and HMI functions. The controller in this application is equipped with Beckhoff’s TwinCAT PLC software package.
“It’s sometimes referred to as a ‘soft’ PLC,” says Wierciszewski. “It’s PLC software running on the HMI. It’s a great solution in this case because I don’t have space for a dedicated, stand-alone PC to run the vision systems in this line. As an even greater space savings, I didn’t have to build an enclosure for the Panel PC. All I had to do was attach a movable mounting arm.
“The CP7202 is more than up to the task for the CPU-hungry vision systems plus every automated function on the machines, handled all at once. Also, ADS [Automation Device Specification communications protocol] in TwinCAT was a snap. With it, I can transfer huge amounts of data between HMI and PLC in real time.”
HMI software
Wierciszewski also developed his own HMI software using a Visual Basic.Net and C sharp platform. “The HMI can communicate very easily with TwinCAT PLC and display visual inspection results, counters, or any other system information,” adds Wierciszewski.
To handle motion control in such a limited space, Wierciszewski designed a stepper motor system from Beckhoff that includes KL2541 I/O terminals for stepper motor control that are wired directly to Beckhoff AS1050 and AS1060 stepper motors. This method does not require additional amplifiers.
Wierciszewski networks the system’s I/O via Ethernet TCP/IP using a Beckhoff BK9000 Bus Coupler. Additional Beckhoff I/O is also used for relay outputs, motor starters on the conveyor, and for solenoids carrying 1 Amp each. “In the past I was using separate analog outputs, thermocouple inputs, and heating control units from various vendors,” says Wierciszewski. “The 250-plus assortment of Beckhoff I/O terminals covers these functions in one compact I/O system.”
Wierciszewski finds that the IEC 61131-3 programming environment in TwinCAT is very efficient. “I’m even showing some colleagues who still program in ladder logic the flexibility of TwinCAT and IEC 61131-3. Some are surprised by what the system can accomplish with just a couple lines of Structured Text. To do the same in ladder logic, it would require a couple pages worth of tedious code.”
The two machines built by Wierciszewski benefited from a number of cost-saving initiatives. “Even with the integrated SQL server and comprehensive vision system, the Beckhoff control platform cost an average of 40 percent less than devices I’ve used previously,” says Wierciszewski. “Using one Panel PC to control two machines also saved considerable time and money.”
The flexibility of the I/O connections brought additional savings. “It’s the labor cost that can be a dominant source of expense, and Beckhoff has helped me greatly improve my assembly and wiring efficiency,” says Wierciszewski. “Previous methods of I/O wiring could take days. With Beckhoff I/O and Ethernet TCP/IP, there’s just one main wire to run. The potential cost and time savings is huge as an alternative to dedicated wires run to every sensor over a long distance.”
Wierciszewski can also save time by logging in and debugging online more often instead of traveling to the customer’s site. “Often, it takes just a few minutes to find and solve a problem,” he points out. “The PC-based architectures and wide range of Ethernet and Internet connectivity solutions are indispensable in this regard.”