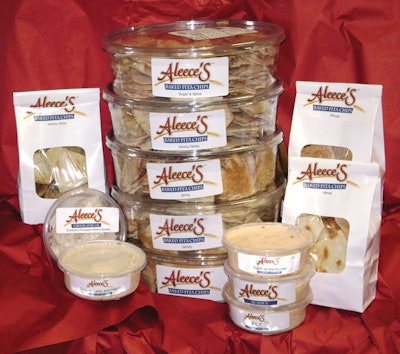
From unscramblers to case packers to scales to stretch wrappers to just about anything else in the packaging universe, people find the solutions they need when they attend Pack Expo. The experiences of Nathan Arthur and Alice Anthony are two good examples.
Arthur is the owner of Arcadia Dairy Farms in Arden, NC, bottlers of purified water and premium juices. A visit to Pack Expo International 2006 resulted in the purchase of a bottle unscrambler as well as a stretch wrapper and case/tray packer.
The need for new equipment was brought about by substantial sales growth. The only way to keep pace was to automate, and having been to Pack Expo in years past, Arthur knew it was the place to go. He identified three major areas in his facility for improvement: bottle sorting, case packing, and pallet wrapping. He also reached out to several existing suppliers that would have a presence at Pack Expo to start his investigation.
“Before the show we worked closely with Douglas Machine Inc. (www.douglas-machine.com) to identify a case packer that would suit our specific needs. We also spoke with Orion Packaging Systems (www.orionpackaging.com) and agreed on a pallet wrapper to complement our packaging line,” said Arthur.
“We worked with both of these companies in the past, so I had confidence that after seeing the equipment in person on site at Pack Expo, we could close the deals,” he continued. “It was quite convenient to only have to make one trip to Chicago rather than going to two locations to accomplish the same goal.”
Douglas Machine’s Axiom® Series intermittent motion servo case packer and tray packer features a patented Smartrak® Steady Stream infeed that facilitates efficient product handling. It moves products gently, helping reduce scarring and damage and maintaining product integrity.
The Axiom case packer was purchased as additional support to an existing line. With its ability to pack up to 45 cases or trays per minute, the system helped ensure products could be packaged in a timely manner. Arcadia also incorporated the optional Velocity™ high speed stacker, which provides continuous product flow at 600 products/min.
The second piece of equipment Arthur purchased was Orion’s Model MA-44 automatic stretch wrapping rotary tower for pallet stretch wrapping. A good choice for medium- to high-throughput applications like Arcadia’s, the MA-44 has a 5,000-lb load capacity, which provides greater flexibility for pallet size. The system uses specially designed rollers to accurately elongate film at a standard rate of 260%, thus allowing for greater film coverage.
A specially designed ‘prestretch system’ features an advanced noncontact film tension sensor helping protect against tangled wrapping. Orion’s unique Insta-Sense system pauses the wrap cycle if the stretch film breaks or runs out.
“Seeing the machinery operating on the show floor was essential in making the decision to move forward,” says Arthur. “However, Pack Expo also provided an opportunity to compare the benefits and features of alternative options we hadn’t been aware of before arriving in Chicago. By being able to take that step, I was confident we were purchasing the solutions that best fit our needs.”
On to unscrambling
But Arthur wasn’t done. Next on his list was a solution for increasing the efficiency of Arcadia’s bottle sorting process. While walking the show floor, he came across Kaps-All Packaging Systems, Inc. (www.kapsall.com) and learned about the company’s Kaps-All AU-6C bottle unscrambler.
The system can handle most container shapes including round, square, rectangular, or oval, providing Arcadia with flexibility to change between its different size bottles. Containers are randomly placed in the hopper and then move into the rotary prefeeder bowl. As the prefeeder turns, containers are single-filed and sent down an adjustable slide chute where they enter an exclusive stand-up unit that orients bottles to an upright position.
The model AU-6C automatically inverts, ionizes, vacuums, cleans, and stands the bottles onto the conveyor. Once upright, the containers exit onto a conveyor for the next downstream operation.
With all of the Arcadia products being either sorted or packaged with the new equipment, seamless integration into the company’s existing line was critical.
“It was important for us to find solutions that would strengthen our manufacturing capabilities moving forward but would not require extensive changes to the existing line,” said Arthur. “Since incorporating the new technology, we have seen our overall productivity increase nearly 40 percent and have decreased downtime by 20 percent.”
With business continuing to grow and several new projects in the pipeline, Arthur will be among the 45,000 attendees when Pack Expo hits Chicago’s McCormick Place this Fall.
“Like any business, we look to be as efficient and productive as possible, while still producing the highest quality products,” says Arthur. “Being able to achieve those goals requires innovative, modern equipment that is flexible enough to accommodate changes in our business. Pack Expo is the place to find what we need to keep our business thriving.”
Same story at Aleece’s
Alice Anthony’s experiences at Pack Expo have been similarly successful. Anthony is the owner of Aleece’s Pita Chips in Peoria, IL, a maker of pita chips and a select variety of spreads. Her visits to the last two Pack Expo shows led to the purchase of a new conveyor system as well as weighing and pita cutting equipment that has helped increase productivity by 50%.
Offered in five flavors, the chips come in either 6- oz bags or 14-oz tubs. They are sold in natural food stores, high-end grocery stores, gift shops, and supermarkets, mostly at the local level. But broader distribution via the Internet is now being explored.
As was the case at Arcadia, an influx of large orders made investment in automation an absolute necessity. The search for increased automation led her to Pack Expo Las Vegas 2005, where more than 1,700 exhibitors were ready and waiting with solutions for all levels of the packaging value chain. After meeting with several vendors and executing some diligent research, Anthony learned that WeighPack Systems Inc. (www.weighpack.com) was the vendor she was looking for.
“Following the show, a WeighPack representative visited our facility and helped us decide on what would work best with our product,” says Anthony. The visit resulted in the purchase of a new incline infeed conveying system and WeighPack Tiger Scale™.
Available in 1-, 2-, 3- and 4-lane configurations, WeighPack Tiger Scales™ can accurately weigh products from 5 g to more than 11 lb. The scales are modular in design, USDA approved, and meet all HACCP criteria. In tandem with the incline infeed conveyor, the system allows for near seamless production.
“Prior to purchasing the new equipment we’d bake the chips, hand pack them in single-serve bags, and weigh them on a small scale. Everything was done manually,” recalls Anthony. With the purchase of the new system, chips are now dropped into a hopper and carried by the infeed conveyor to the scale. With a press of a foot pedal, a precise amount of chips is dropped into waiting bags. The bags are then packed in boxes and shipped.
The current operation requires only one person to manage the scale and fill the bag. “In a matter of minutes, the job is complete. Our productivity has increased nearly 50 percent,” claims Anthony.
With the new system, Aleece’s Pita Chips were efficiently manufacturing the increasingly popular snack faster that ever. But there was one more issue to overcome—cutting the chips. “We had to find a more efficient way of cutting the pita bread,” says Anthony. “This would also provide a way to trim additional production costs, since this process was also being accomplished manually.”
Returning to Pack Expo International in 2006, Alice met with FoodTools, Inc. (www.foodtools.com). Working with the engineering team, the two companies determined that the TS-1 Tortilla cutter provided the best solution to improve pita cutting and fit Aleece’s specific requirements.
“Previously, we often had to shut down our oven while the pita was being cut, which significantly lengthened our production cycle,” remembers Anthony. The addition of the TS-1 eliminated the problem, allowing for the production line to flow without any starting and stopping.
As orders steadily increase, Aleece’s Pita Chips has begun planning for its next step towards minimizing manual operations and streamlining production. “We intend to visit the upcoming Pack Expo International in Chicago to explore the latest in automation technology,” says Anthony.
“Pack Expo provides attendees with a valuable opportunity to meet with industry experts and discuss solutions pertinent to their own businesses,” comments Anthony. “As we continue to expand, we know that the show will help us find new ways to improve the efficiency and productivity of our operations.”