But what might be called a new generation of modern challenges has lately been occupying the attentions of industry, government, and academic food experts.
Modern challenges, like the threat of terror or counterfeit or substandard ingredients and products, raise an important question for food packagers: What, if anything, do I do to protect my company that I am not already doing?
Soon after the 9/11 attacks, FDA issued guidance documents to help importers and others in the food chain of commerce evaluate how they might harden their practices against intentional contamination. These recent efforts appear to be inspired by a broader set of concerns, including the prospect of terror tampering, yes, but also economically motivated quality issues and product counterfeiting.
It has always been true that quality assurance practices and procedures are designed to protect your company by assuring that the product is made correctly first time, every time. From a regulatory point of view, these concepts are embodied in ‘current Good Manufacturing Practice’ principles, and, for some products like meat and seafood and juices, Hazard Analysis and Critical Control Point procedures, and scheduled processes for acidified and low-acid canned foods and aseptic packaging systems.
But with the intervention of some sad realities, food makers and others had to start rethinking what they did to confirm not just the quality of their product, but its safety as well. The specter of terrorist interference with the food supply, and the reality of supplier unreliability especially regarding imported products and ingredients, have intruded to make packagers rethink what they do.
And the focus is more on the products and ingredients that they take in, rather than on what happens within the four walls of their own facilities.
Happily, there are excellent sources of assistance for companies large and small tackling this problem. The most recent, and sure to be among the most influential, is a “Food Supply Chain Handbook” from the Grocery Manufacturers of America.
The GMA is the largest trade organization for the grocery industry. In October of last year, they held a meeting in Washington, D.C. to gather ideas on attacking these issues. Over 150 attendees participated, including manufacturers but also importers, retailers, regulators, and trade officials.
As a result of such varied perspectives, the group was able to identify the most important issues and the most practical ways to address them.
The workshop confronted participants with several key questions:
• What programs should suppliers have in place to meet customer requirements for safety and security?
• How can buyers best verify the integrity of the products purchased and how frequently should this be done?
• How should the food industry best share testing results with the federal and or state agencies?
• What is needed to ensure letters of guarantee and certificates of analysis are meaningful and accurate?
• What are the components of and how should buyers implement a second and/or third party audit program?
The resulting handbook, which at press time was still in draft form, is a start-to-finish enumeration of recommendations to allow those in the food and beverage chain of commerce to evaluate their practices and make improvements where they seem warranted.
Not surprisingly, management of one’s suppliers is a major topic. Particularly where the concern relates to imported product, simply assuming that a supplier who guarantees the quality of its product will deliver every time is less possible than in the past. Product purity and quality are harder to consistently assure when the sources of supply are varied. And your foreign source might be more a broker than a factory, so even if you order from one entity you might be receiving product from a range of sources, sometimes without knowing it.
Some participants in the program also advocated a point of view that is desirable to have suppliers who have a complex and sophisticated understanding of regulatory requirements. Rather than only asking for certain specifications to be met or confirming them once the product is received, it’s often a good idea to stick with suppliers who can demonstrate to you that they understand the regulatory requirements in the first place. Amplify that with written documentation in the form of certificates of compliance and technical specifications, and you will have improved your measures of assurance.
Other segments of the handbook appear to cover similar ground to the good manufacturing practices regulations, addressing sanitation issues, employee training and label control programs.
FDA is certainly active in this area. In March, Dr. Stephen F. Sundlof, director of FDA’s Center for Food Safety and Applied Nutrition, told Congress that “changes in consumer preferences, changes in industry practices, and the rising volume of imports have posed challenges that required us to adapt our current food protection strategies.”
FDA is now asking Congress to give it greater authority to see documents during food facility inspections—right now they have access to such records if they have a reasonable belief that the food is adulterated and presents a threat of serious adverse health consequences or death. FDA wants to eliminate that requirement for a reasonable belief the food is adulterated, and they want access to records of related food products, too, such as those produced on the same manufacturing line. They also want the power to order companies to recall foods.
As for imports, FDA is hoping to change the focus from merely checking on the compliance of imported foods to helping assure that quality products are manufactured overseas in the first place. The agency has already put in place cooperative agreements with the Chinese government, and this emphasis on GMPs by foreign manufacturers should help reduce the quantity of violative products in the first instance. It is philosophically similar to industry efforts to pressure suppliers to be familiar with and comply with regulatory requirements.
One way manufacturers keep the pressure on their suppliers is by demanding that the suppliers issue letters guaranteeing the compliance of the products or ingredients they supply.
Though letters of guarantee passed down the chain of commerce are a common practice within food and packaging businesses, companies don’t always understand their full implications. When you receive a guarantee letter from a supplier that guarantees its product complies with the Food, Drug & Cosmetic Act, a common question is whether one should take any further steps to confirm whether that representation is accurate?
The legal answer is that you aren’t required to. But the prudent answer, depending on the situation, is often “yes you should.” After all, what the law requires of you is that you assure that all the product you put into commerce is in compliance with law, not adulterated or misbranded. The guarantee letter is simply a commercially common measure to allow different players to get the assurances they need that the product is in compliance. (It also can protect some players from FDA prosecution for trafficking in adulterated or misbranded products, but only in limited circumstances.)
However, it is often a good idea to take further steps, call them due diligence, to confirm the letters’ information. This can include demanding laboratory analysis of the product or conducting it yourself; asking for additional details about the product formulation; and even, on a longer term basis, inspecting the supplier’s facility and learning their level of sophistication in terms of compliance issues.
When it comes to packaging materials intended to contact food, it is also important to remember that while a supplier might issue a guarantee letter about a particular product, it is the intended use of the product that really matters, and it is important to assure that your intended use is within the scope of the conditions of use that the guarantee covers.
Dr. Craig Henry, senior vice president and COO for Scientific and Regulatory Affairs at GMA, was a central figure in the development of the handbook. He emphasizes that now, as the handbook is being finalized, GMA believes that industry has to take responsibility for what they buy and sell. He says that various companies’ commercial clout should be used to eliminate “high risk” products and producers. The effort and money needed to do this will offset the damaging costs and loss of goodwill associated with product recalls, reductions in consumer confidence, and in enhanced pressure from Congress.
One group is emphatically bringing together industry, government and academics to attack counterfeiting and similar economic hazards. John Spink, M.S., Faculty Instructor at the Michigan State University Food Safety & Toxicology Center, is spearheading the Packaging for Food and Product Protection Initiative. Its goal is to attack the product counterfeiting monster, combining packaging, food, drug, medical devices, general consumer products, chemicals, auto parts suppliers, and other industries, along with government agency personnel and other academics.
Spink says many companies are well along working on various anticounterfeiting strategies, but they can’t discuss them because they are, necessarily, confidential. He says that having an academic setting helps allow the development of these ideas, particularly when each product industry wants to hear what the others are doing. The Initiative’s work has begun, and the organizers will present a course this Summer on Packaging for Food and Product Protection.
Eric can be reached at [email protected],
and visit his firm’s Web site at www.ericfgreenbergpc.com.
Many sources of advice on enhancing supplier reliability
Food packagers always face challenges, of course.
May 12, 2008
Companies in this article
Machinery Basics
How Can You Honor a Leader?
Induction into the Packaging & Processing Hall of Fame is the highest honor in our industry. Submit your leader to be considered for the Class of 2024 now through June 10th. New members will be inducted at PACK EXPO International in Chicago
Read More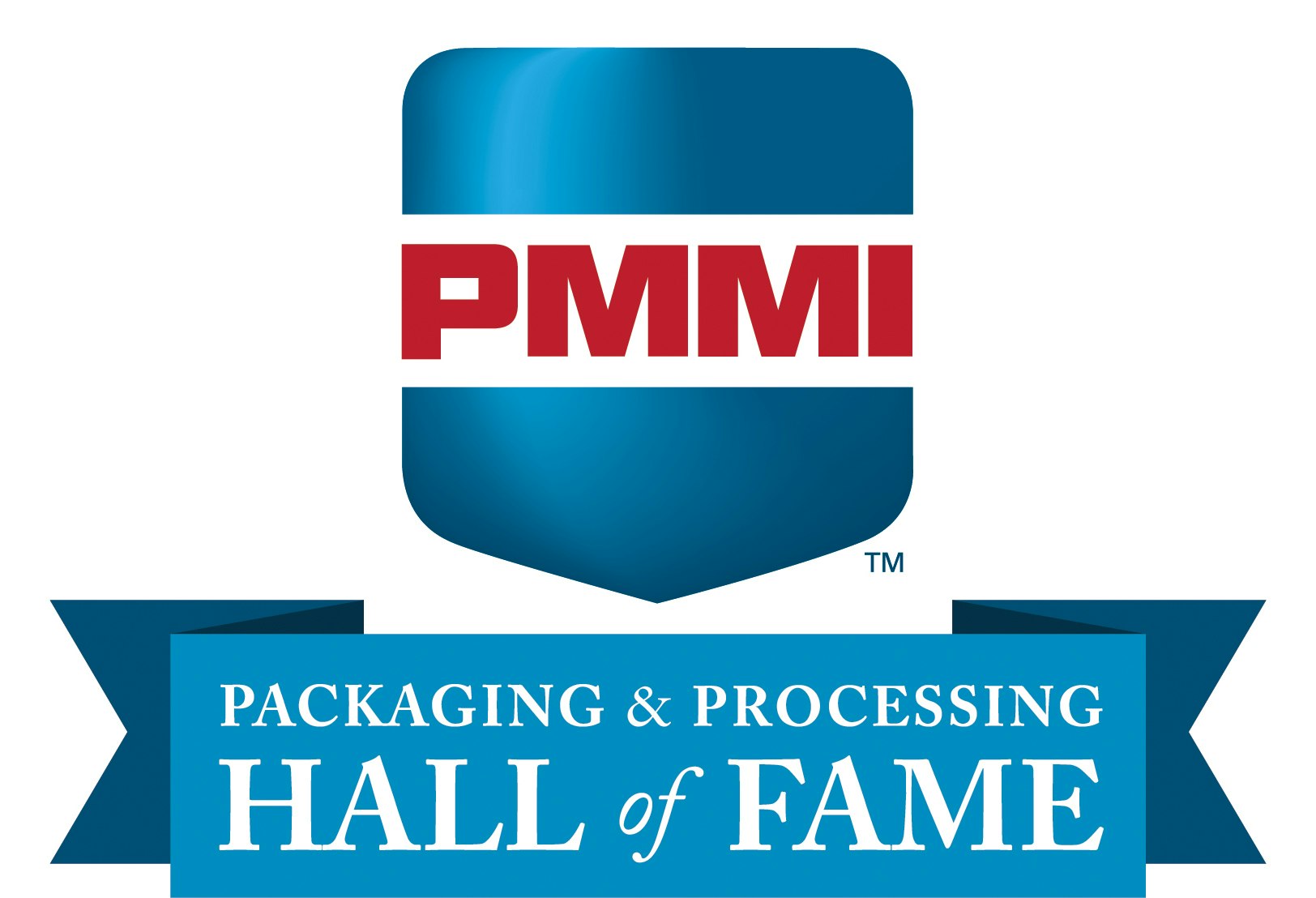
How AI is reshaping CPG manufacturing operations
Today’s CPG companies are faced with mounting challenges in their manufacturing operations. You have the data that could help you, but can you turn that data into knowledge? See how artificial intelligence can help. Learn what’s working for Pfizer, Post, and Smithfield.
Read More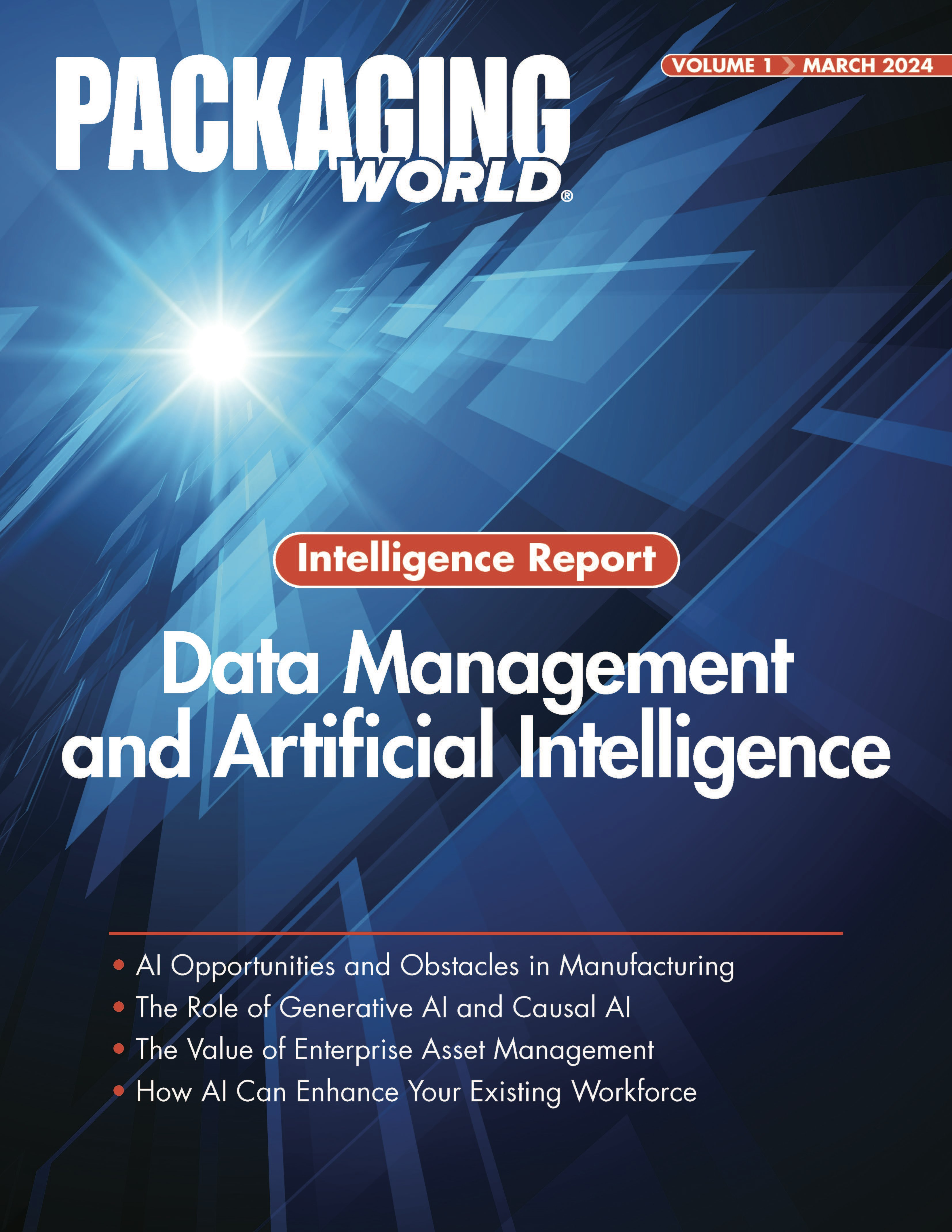