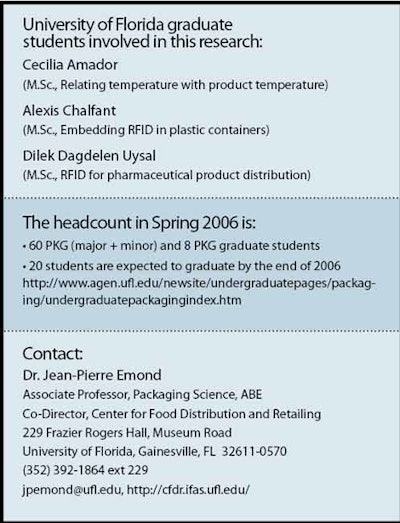
In Packaging World's initial visit to the University of Florida back in 2004 (see UF juiced for RFID), we were impressed by the research and development projects that were part of the university's fledgling packaging program.
During a recent interview with UF associate professor Jean-Pierre Emond, Ph.D., known as JP, we found that the program's R&D momentum continues. JP is codirector of the University's Institute of Food and Agricultural Sciences (IFAS) Center for Food Distribution and Retailing (CFDR) and is right-hand man for the school's packaging program run by professor Bruce Welt, Ph.D.
Here are some highlights:
PW: How is the program going?
JP: Fall 2006 has our biggest class in terms of number of students. When I started, the average number of students in my classroom was 15 to 20, now it's between 50 and 60 (see graphic p.64). Some of my courses have waiting lists. That's very thrilling. At the start, some students were coming to packaging as a last resort, now they are coming to UF with packaging in mind. We know we are sending the right message to community colleges.
PW: How are things with the CFDR?
JP: The CFDR is growing very fast with now 28 UF researchers and 8 external researchers. In order to answer the demand we need to consolidate many projects together. People come to us seeking advice because of the unique environment we can provide at UF. Our external advisory board comprises top 10 food retailers, food service and restaurant chains. We receive inquiries from India, Europe, Australia, all over.
PW: What's the latest on UF's RFID research?
JP: RFID is huge for us. We are working on a process to embed RFID tags in both large and small plastic injection-molded containers. As expected, RFID tags are getting smaller (see image above right) and cheaper. We are using tags ½” square and are working with embedding new generation near-field/far-field (NF/FF) RFID tags. We have worked with RFID for two years and with the new NF/FF tag
technology for six months.
PW: What does that mean exactly?
JP: Near-field design—reading done within 12 inches of the tag—permits reading through water, though that is still an issue with far-field designs. These are UHF 915 MHz frequency tags. [Ed. note: The distinction between near-field and far-field technology, which use the same silicon chips, is in the antennae design]. For example, NF tags in or on small containers allow water bottles to be read by a cashier or on an RFID-enabled “smart shelf.”
NF uses a different antenna, but all new RFID chips are capable of having this feature today.
We use chips made by Impinj in tags provided by Avery Dennison, very outstanding products. And we are using a new, more powerful reader-antenna from Symbol Technologies.
The containers that we are testing are in two sizes and primarily molded of polypropylene: A large 24x16x12”H reusable plastic container (RPC) and a smaller 48-oz container used for produce.
PW: What does this technology provide?
JP: Thanks to the technology, we have less concern with placement and orientation of the tag on the container as before. We used to struggle to get reads with tags, especially around water. Now we can embed it anywhere in the container.
PW: How is this project funded?
JP: Our sponsorship is from IPL (www.ipl-plastics.com) of Canada. Besides a major supplier of RPCs, IPL is also a huge supplier of single-serve containers such as for yogurt and dips. I've been working on IPL research [including in previous work] for 12 years and know them pretty well.
PW: Do you have other RFID projects in the CFDR?
JP: Yes, one called V2 Visibility Project. We try to show product visibility of the RFID Electronic Product Code in a simulated EPC network that links packager, retailer, and RFID network provider. We post the event on the PC “dashboard”—a graphics interface from Franwell—so participants can see when a product is tagged related to a purchase order from a retailer. In this case, the retailer is Publix. There is some monitoring of tagged cases on production lines, and some monitoring in the supply chain. No matter the incoming source, all have challenges to ensure that the container can be read when it arrives at Publix and provide real time information about the status of the shipment. A weekly conference call involves 30 people.
PW: What's the project's status and results?
JP: After one year, we completed Phase 1 in August and are compiling results from a lot of data. What is interesting is the kind of problems we can encounter within the system and supply chain. We have seen that sometimes you read a tag where you don't want to read it. For example, someone at a warehouse can carry a box near a reader-antenna and it is caught as a movement that messes up the data.
Phase 2 started in October. It will be at the store level and include temperature tracking with RFID. For Phase 2 we will include more retailers and suppliers.
PW: Can you tell us more about that?
JP: You can place a sensor tag on a box, but the temperature that the sensor reads is not that of the product inside the box. We are developing a model of what the tag temperature means for the product temperature inside the box. We are working with tropical fruits and other produce, and will soon work with meat.
For years CFDR member Dr. Cecilia Nunes (faculty, Food Science and Human Nutrition) has developed a large number of prediction models for shelf life and quality of produce, with a database of more than 40 products. If you can provide us the temperature history during transit for those products, we can predict the remaining shelf life and, for example, decide what to do when the product reaches the distribution center.
We can show people how a product should look like at a DC—using our picture database of products—and if doesn't look like that, then it is a problem.
PW: What role does packaging play in this modeling?
JP: Packaging plays a big role. The model varies depending on the type of package and the packing density of the product inside. A corrugated box behaves differently than an RPC with vents. We have two graduate students working on this and have just added a third. We are also working with pharmaceuticals.
PW: Are you working with UHF or HF for pharma?
JP: We test both frequencies, not to see what is best, but to measure different challenges for each. We are spending a lot of time with drug wholesalers, like McKesson and H.D. Smith, and observing when and how they apply RFID tags to packages.
One of our problems in the past was not knowing exactly how tags are applied in the real world rather than in a lab. Now we understand that better and have improved the wholesaler's efficiencies with RFID by making it more seamless for them.
We are also developing RFID technology to deal with orders with a mix of packaging. For example, 150 different orders at a wholesaler may have 150 different package configurations. Interaction in mixed loads makes it a big challenge to read all the RFID tags. And with drugs there are a lot of blister packs, foil, and liquid products, all randomly mixed together—nothing like any real pattern. Tag placement on each kind of product and package affects all the others.
It has proven to be much more challenging than we expected. It is fairly easy to read a single product, but mixed loads get very tricky.
PW: What else have you learned?
JP: That some products we didn't think would be difficult to read were huge challenges, such as a certain bottled contact-lens solution, which seems to draw all the available RF energy and leave none for the tags. Wherever we put the tag, even at distance from the bottled solution, it seems impossible to tag this kind of product.
Pre-injected syringes of vaccine are equally challenging. Even far from the syringe, it's very difficult to read the tag. What is mind-boggling is that there is a lot of free space in the package, which usually means good reads. However, even a tag an inch from the syringe is impossible to read.
All this pharma research is done internally without a sponsor company. We “borrow” real product from these wholesalers, test it, and then return it.
PW: What other research are you working on?
JP: One thing in the development is weight reduction of RPCs without compromising the structural integrity, plus with a flat area on which to apply an RFID tag. We are close to reducing the weight by 40%, all done through structural design changes.
We are also working on another project that involves adding barrier to double the shelf life for
single-serve products in molded containers. The process is seamless and adds only nominal costs. It combines current technology in a unique way. I expect the sponsor, IPL, to make this technology available before the end of 2006.