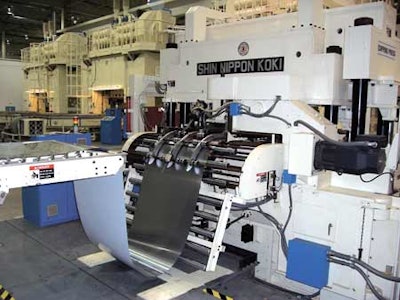
From the uncoiler to the presses to decorating and palletizing, the twin can-making lines at DS Containers (www.dscontainers.com) in Batavia, IL, are marvels of power, precision, and automation. The finished product—two-piece steel cans currently used for aerosol products, though later uses outside of aerosols could include such things as lotions and gels—are every bit as impressive. No side seam mars the sidewall, an integral dome adds a touch of elegance, and litho printing in up to eight colors delivers shelf impact galore.
DSC’s 236ꯠ sq’ plant is special, too, largely because of what’s missing: noxious emissions. Because the firm makes its cans from PET-coated steel, the coatings typically found in can-making are not involved in the process. And with no coatings comes no ovens to cure those coatings. Thus, far fewer emissions are produced.
DSC based its coil-to-can proprietary technology on similar methods used for the revolutionary “bottle can” introduced about five years ago by Daiwa Can Co. That container, however, is PET-coated aluminum rather than steel.
The connection with Daiwa helps explain DSC’s name, as the DS stems from Daiwa-Seikan. “Seikan” is the Japanese word for can-making. DSC is an affiliate of Japan’s Daiwa Can Co.
Another connection behind the scenes is that Bill Smith, chairman and CEO of DSC, was executive vice president of American Can Co. in the 80s and helped manage the technology and licensing agreements between Daiwa and American Can. Later, as CEO of U.S. Can, Smith stayed in close connection with Daiwa and served in an advisory capacity as the aluminum bottle can was being developed by Daiwa. It was Smith’s idea to bring the bottle can to the U.S.
Steel’s price advantage
In bringing this proprietary technology to the U.S., DSC switched from aluminum to steel because the cost of steel is so much lower, roughly in the 20% range. The PET-coated steel comes from Corus Packaging Plus (www.corusgroup.com), an Anglo-Dutch organization that applies the PET coating as part of its coil-making process.
To fully appreciate the significance of this container, it helps to point out that most aerosol containers in use today across the U.S are three-piece steel. Making them requires multiple steps and involves a lot of work-in-process logistics, including:
• Converting coils of tin-plate steel into sheets
• Printing sheets of steel and cutting them into individual blanks for can bodies
• Making can ends
• Forming cylinders with a welded side seam
• Seaming on the ends
• Coating and curing
DSC, on the other hand, makes its two-piece cans in a single pass that takes about 20 minutes from uncoiler to palletizer. Even eight-color offset decorating is included inline. According to Ron DeSimone, director of corporate marketing at DSC customer Chase Products Co. in Broadview, IL, the simplicity of this in-line can-making process greatly shortens time to market. He says that where it might take six weeks to get a shipment of three-piece steel aerosol cans, it takes about two weeks to get their two-piece steel counterparts from DSC. Other advantages, notes DiSimone, include these:
• The elimination of the welded seam necessary on three-piece steel cans produces a much sleeker container and also eliminates any chance for rust along the sidewall.
• The PET coating on outside and inside prevents rust from forming along the can bottom
• Minimum orders for three-piece steel cans run around 50ꯠ with its logistically simpler in-line process, DSC can produce in quantities of 4ꯠ.
For these and other reasons, Chase Products was among the first to commercialize DSC’s two-piece steel aerosol container (see sidebar).
Made in America
Watching the container-making lines in action is impressive partly because the very thought of making anything at all in the U.S. has become so unfashionable. The sight of sleek new containers rolling through the line is a satisfying reminder that “made in America” is not so far-fetched after all.
But beyond that, the two lines are also impressive because it’s hard to imagine how a coil of steel can be drawn so deep with such precision and at a speed of 600 containers/min. A can-handling system from Fleetwood, a subsidiary of Barry-Wehmiller (www.bwdesigngroup.com), combines vacuum and magnetics to play a key role in moving containers from one machine to the next. Can shaping, trimming, and curling equipment all comes from Daiwa subsidiary Shin Nippon Koki (www.snkc.co.jp).
“Where it might take six weeks to get a shipment of three-piece steel aerosol cans, it takes about two weeks to get their two-piece steel counterparts from DSC.”
The process begins when the 8-mil steel passes through a cupping press, which uses six-across tooling to turn the coil-fed sheet into large cups about 5” in diameter and about 2-3” deep. In a second press, the cups are drawn to a depth of 6” on the line making the 211/604 (18-oz) can and 7” on the line making the 211/713 (22-oz) can. A magnetized conveyor carries them through an oven.
“The oven does some work chemically to the polymer coating, almost like a curing process to ensure coating integrity,” says CEO Smith.
Exiting the oven, a trim station trims the flange on the open end. At that point, the containers are ready for decorating, which is done on one of two offset litho Rutherford decorators from Stolle Machinery (www.stollemachinery.com). A curing oven shortly after the printing room cures the inks.
“One big bottleneck in manufacturing conventional three-piece steel aerosol cans is in decorating,” says Smith. Because it’s an off-line sheet-fed process, it’s not practical to produce in anything but long runs. Short runs would involve too much time spent on changeover. At DSC, that’s not an issue.
“Each line has two high-speed decorators,” says Smith. “To change to a new label, we swing a gate and resume running.”
Next in line is the third press. Here the sloped shoulder and neck are formed. Another oven follows, again to cure the PET coating. A mass conveyor section leads to a trimming station that trims the flange on the open end a little more. An overhead conveyor then takes the containers to a combination machine that cuts the top off the neck, curls it, curls it again, and then curls it a final time. A four-camera vision system checks for flaws in the curl and any can that’s flawed is automatically rejected.
Shaping the bottom
Cans exit this first combination machine and are conveyed to another one. This time, it’s the can bottom that is the focus of attention. Once again, four distinct stations are used for necking in, creation of the flange, application of the bottom by way of an initial seam, and then final seaming of the end to the body. Ends are fed automatically to the seaming machine by a Fleetwood feeder.
Two vision systems are used to check the container at this point. One examines the integrity of the flange, while the other looks at the interior of the container. If any dents or scratches are detected, that container is rejected. A short distance downstream is another opportunity for rejection. An air-testing device subjects each can to 120 psi, and any can with a pinhole will be detected and rejected.
End-of-line operations are every bit as automated as the actual can-making process. A Goldco palletizer from Barry-Wehmiller neatly layers the cans on pallets, two Signode (www.signode.com) strapping stations stabilize the layers, and a Lantech (www.lantech.com) stretch wrapper finishes off the pallet.
Responding to an observation that the two lines are a lot like the aluminum bottle can lines that Daiwa runs in Japan, Smith agrees but emphasizes that with steel as the can material, there’s a lot more draw and redraw involved and only very little ironing.
“Ironing is what thins out the aluminum bottle can, but here we are more concerned with keeping the thickness in the body to give it strength,” says Smith. “Remember, it has to hold pressurized aerosol products. We want this thing to be like a tank.”