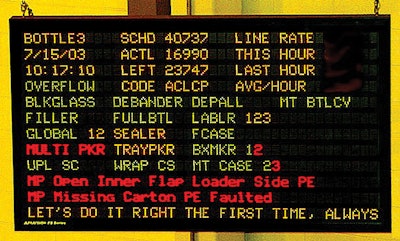
Our survey on p. 64 documents the pitfalls packagers have experienced in collecting data, converting it into knowledge, and acting on it. But there’s no question that the payoff—boosting line efficiencies and correcting quality problems early—is too great to ignore. In the pages that follow, we present several successful data acquisition implementations.
A case for data collection
User: Coors Brewing, Elkton, VA, facility, one of three Coors-operated bottling plants in North America.
Application: Box production machinery started up January 2002 for erecting and preparing corrugated cases for two bottling lines.
Data collected: Twenty different pieces of real-time information about each piece of equipment including status, alarm details, product counts, and machine cycles used for lubrication and maintenance.
Benefits: Track productivity, isolate maintenance
problems, help track scrap reduction and reduce losses.
Technology: Data is collected via Ethernet network
connection to an Allen-Bradley ControlLogix™ 5550
programmable logic controller from Rockwell Automation. Off-the-shelf data acquisition software from OSIsoft runs on
a dedicated PC. R.A. Pearson equipment was DA-enabled per Coors requirements.
How it works: Data from the PLCs on about 10
individual pieces of box-making and associated equipment from Pearson travels across an Ethernet network to the
supervisory PLC. These data are sampled every five seconds and downloaded to a dedicated database on a PC running the OSIsoft software. Data can be analyzed graphically
or converted into report form.
Who uses data: Production, maintenance, scrap reduction group, and quality control. Accessible via Ethernet to anyone in the plant with a PC and a password.
Networks: Overall architecture already in place,
augmented by minor additional expansion.
Unique: Three large “scoreboard” (above) displays easily visible throughout bottling area display key machine status using red, yellow, and green text. Messaging for alarms provides specific details such as “discharge jam on erector #4.”
Quotes: “It lets us zero in on specific problems and can be used to identify potential problems via trending. As a result, we’ve had a reduction in downtime.” —Ken Hoes, plant engineer, Coors-Shenandoah.
“It helps improve productivity and quality. We’ve grown so used to data acquisition capability, we’d be lost without it. And we don’t install equipment without it.” —Mitch Hofecker, control engineer, Coors-Shenandoah.