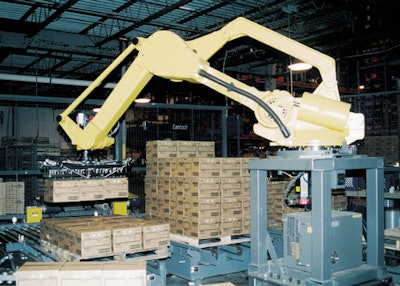
Schroeder Milk’s robot received a chilly reception when it started up in October ’00, but that was by design. It was crucial for the Maplewood, MN-based dairy that the new palletizing robot perform tirelessly in an area kept at 38°F. While those conditions keep product fresh, they also took a toll on operators who had to palletize cases of cartoned milk for hours on end on three production lines.
After initial research, personnel at privately held Schroeder quickly warmed to the idea of upgrading from manual palletizing. A robot that operates during two or three daily shifts replaces hand palletization for those three lines.
Robotic automation was necessitated by a growing demand for corrugated cases for milk, says vice president of manufacturing Carl Schroeder, Jr.: “Some days, we’d have three people per shift stacking cases on pallets. Five or six days a week, they’d spend 95 percent of their time stacking. With ergonomic considerations and workers’ compensation issues added, it was an easy sell to the board of directors and ownership group.”
The expected payback period is 18 months. “Selective attrition” was used to reduce head count in this area, according to Schroeder project manager Bob Banken.
The ‘work envelope’
Installed by integrator Brenton/RAM Center (Alexandria, MN), the system is anchored by a Fanuc (Rochester Hills, MI) four-axis robot. Mounted atop a frame, the robot operates within a 20’-diameter ‘work envelope’.
The robot moves cases of cartoned milk from three infeed conveyors and palletizes them on three corresponding outbound pallet stations. The three lines can be used for identical or different stockkeeping units. Sensors on each conveyor apprise the robot’s controller of case location and status. Packaging World is told that the majority of sensors used are Allen-Bradley photoeyes from Rockwell Automation (Milwaukee, WI).
Prior to a production run, an operator selects on a portable alphanumeric display keypad what product SKU is going to be palletized on which line. The system knows what the case dimensions are, how many cases/layer, how many layers/pallet, any slipsheets are needed and whether cases require any “gapping” for stability. Schroeder can choose from 13 different preprogrammed pallet load set-up sequences. The robot operates using Fanuc’s application-specific “PalletTool” software as the core programming. Operating in the background is an Allen-Bradley 50/4 programmable logic controller from Rockwell.
Schroeder’s robot handles seven cases/ line/min, or a total of 21 cases/min when all three lines are in operation. Schroeder reports that the robotic upgrade required no changes of its RSC cases, which convey into the robot cell from case sealers.
The robot builds the pallets by lifting and then assembling three cases at a time. Designed to handle payloads of up to 220 lb, the robot’s array of 27 vacuum cups can easily lift three cases, each weighing up to 36½ lb.
The robot’s arm, or end effector, is also designed to pick up and accurately place pallets and slipsheets.
For pallets, it uses pneumatically retractable fork-style grippers. Pallets are picked from one of two automatic pallet dispensers used to present the stacked pallets one at a time to the robot. Each dispenser is controlled by an Allen-Bradley Micrologix™ PLC with interface to the robot via discrete I/O.
To pick up slipsheets from a supply magazine, the pneumatic grippers used for picking up and moving empty pallets are swung inward and out of the way. The robot tool then uses the vacuum cups to lift and move a slipsheet to the preprogrammed location.
Depending upon the product, pallet loads are completed on an average of one every seven minutes. The completed loads advance from the three pallet stations on chain conveyors to a common powered roller conveyor that leads to a newer Model Q100 automatic stretch wrapper from Lantech (Louisville, KY).
Automatic ‘shifting’
The robot is also programmed to run automatically at a slower speed for more challenging cases, such as those containing taller cartons. That solves issues related to controlling the hydraulic force of the liquids inside the cased cartons.
For example, when one of those types of cases is run on line A, the robot moves line A product at 80% of full speed, yet accelerates to full speed on the return stroke. It will then operate at whatever speed is programmed when it is handling product on Lines B and C. This programming is done on a per-SKU basis through PalletTool.
The Fanuc Model M410IHFRJ3 robot was selected based on Schroeder’s needs including speed, case weights and palletizing patterns. “A plus was that Brenton’s location is close,” adds Banken. “Also, RAM had been in business installing robots longer than most other companies had.”
Brenton acquired RAM (Robotic Aided Manufacturing) last summer, essentially finishing off the project Schroeder started with RAM. That makes Schroeder the first installation for Brenton/RAM.
“Brenton handled the problems common to project installation with professionalism and a sense of urgency,” comments Banken. “It is refreshing to see people take ownership and pride in the work they do and the results they achieve.”
According to Banken, one of the key challenges Schroeder addressed included educating personnel that all upstream functions need to work 100% of time. “It’s the old garbage-in, garbage-out rule. If boxes are not formed or sealed properly, it can cause problems,” he states. “If pallets are damaged too much, it can cause problems.” Banken says that they were pleased that the robot could also accept rebuilt GMA 40’’x48’’ pallets.
Banken reports that the robot has performed very well, and is “extremely accurate and repeatable. It allows more consistent results from our stretch wrapper,” he adds.
Lovable robot
“Our personnel in the area love it,” he emphasizes. “It makes operators’ jobs better because they do not have to hand-stack 30-pound boxes for eight hours daily.” He says the operators learned to run the robot “very quickly. It is very user friendly . . . the screens pretty much tell you what to do.
“Production likes it because it is here everyday and does not look for breaks or days off. It has yet to go on vacation, call in sick, or be tardy,” he jests.
Banken says that the robot has even been a positive for customer relations: “They know that we put the system in to pay for itself and keep our focus on trying to be a low-cost producer as we stay on the cutting edge of technology.”