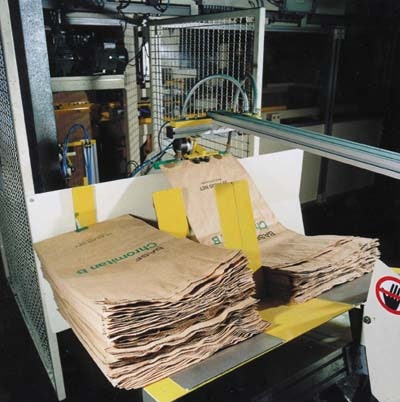
Unhappy with the inefficiency of a manual packaging operation, management at Elementis Chromium set out to modernize its multiwall bag filling system. The solution it came up with was a completely integrated line from Korsnas Paper Sacks, Ltd. (Northfleet, Kent, England), a manufacturing unit of Korsnas AB of Sweden.
Based in Stockton-on-Tees, England, Elementis Chromium produces chromium sulphate, a chemical used extensively in the leather tanning industry. The material is difficult to handle because of its small particle size and its hygroscopic nature. A whiff of moisture causes it to solidify.
Before the new line was installed, the firm filled its 25-kg (55-lb) four-ply paper valve bags with a hand-operated machine. The operator placed a valve bag on a scale and hit a switch to begin the fill cycle. The scale stopped product flow at 25 kg. The operator then lifted the bag onto a checkweigher. Next, he folded it and glued it closed. Finally, he placed the bag on a pallet, which later was stretch wrapped on a rotary platform system.
With this arrangement, filling speed was just fast enough to keep pace with the drying oven that precedes packaging. But packaging required an operator and an assistant. On the new integrated line, one operator is sufficient, a savings that looms large in a plant that runs around the clock every day of the year.
Speed remains about the same on the new line as on the old. “Our throughput is limited by the dryer that precedes packaging,” says Ken Fearns, operations development manager at Elementis Chromium. “The packaging equipment is specified for five tons per hour, but we actually pack about four.”
New bag style
In the new operation, the valve bag has been replaced by an open-mouth, pinch-bottom bag. Bags are supplied on stretch-wrapped pallets, about 2귔 per pallet. The operator removes the stretch wrap and feeds the bags in bundles to the twin magazines of a fill/seal machine made by icoma (Aachen, Germany), a manufacturing unit of Korsnas AB. Each magazine holds about 150 bags. When one magazine is empty, the two automatically switch positions so that bag feeding can continue unchecked.
The icoma machine picks a bag from the magazine with vacuum cups. Then a series of mechanical grippers and vacuum cups moves the bag to the fill station.
Above the icoma fill/seal machine is a Model BL160 twin-screw net weigher from T.A. Shore (Nottingham, England). It uses a twinscrew system to meter product into a weigh bucket mounted over a load cell. Both screws turn simultaneously until the bulk of the weighment is in the container. Then the small screw tops off the weight bucket until the proper amount is in. Gates close to prevent more material from dropping, and the weighed product is then dropped down a chute into the open bag waiting below. Specially designed shrouding keeps dust under control at all times.
The chute withdraws, and the platform vibrates the bag to help settle its contents. A mechanical clamp closes on the open end of the bag, and by this means, the bag is carried to the next station. Here, heat-seal bars close on the bag and its inner coating of polyethylene to create the first of three seals. The bag is then indexed forward to the next station, where hot melt is sprayed from a nozzle and the top is folded and held clamped shut a few seconds. This is the second seal. Finally, the bag is indexed to another station where hot melt and clamping are repeated, thus giving the bag top its third seal.
“Much of our production is for export to locations in the Far East,” says Fearns. “Our product can pick up moisture easily during such long shipments, so the three seals are much better than the seal we used to have on the valve sacks. Yes, producing three seals on our new machine is a pretty elaborate process, but it works well.” The solid build of the equipment, notes Fearns, is one of its more important features.
Checkweigher
Exiting the fill/seal system on a conveyor belt, the filled sacks move through a checkweigher from Mettler Toledo (Worthington, OH). An ink-jet printer from Alpha Dot (Belle Mead, NJ) imprints a lot number on each bag. Next is palletizing, which, notes Fearns, also has been automated.
The low-level palletizer was supplied by a European maker that recently closed its doors. Bags are conveyed onto a forming plate, which then lifts an entire layer and carries it to where the pallet waits. The forming plate withdraws, gently dropping five bags per layer, eight layers high. The full pallet is then discharged to the next component in the completely integrated system: a stretch hooder from Kurt Lach-enmeier, a Danish firm represented in the U.S. by Global Marketing Management (Charlotte, NC).
This machine is fed by a continuous tube of stretch film wound on a large roll. As a pallet load reaches the entry point of the machine, a sensor measures its height. Material is automatically drawn from its roll and the top is heat sealed to form a hood and cut from the roll.
Vacuum cups pull the stretch film open so that it fits over the top of the pallet. The film is then stretched mechanically from the top of the pallet to the bottom. When the film is released by the mechanical stretchers, it clings tightly to the contours of the pallet.
Like the fill/seal system upstream, the stretch hooder was selected for its robustness.
Fearns says he appreciates the firm support the stretch hood gives to the pallet, especially in view of the long distances the pallets must travel. Supplied by Visqueen Films (Stockton-on-Tees, England), the polyethylene hood material has a thickness of 130 microns (5 mils).
‘Total support’
“The design team from Korsnas provided total support throughout the installation and commissioning process,” says Fearns. “There were a few initial difficulties. But because one company was handling the whole system, including the sacks themselves, any problems were quickly rectified. When a number of different suppliers are involved, any problem always seems to be the other company’s fault.”
The Korsnas sacks Fearns refers to are made from a three-layered construction consisting of a 100-g layer of what Korsnas calls DFDC and two 80-g layers of semi-extensible paper. A technology called “micro-creping” in the machine direction is what Korsnas uses to give the 80-g layers of paper a measure of extensibility, and with extensibility comes added toughness.
As for DFDC, Korsnas makes it by joining two 50-g sheets of paper together in a duplex structure that is “squared,” i.e., properties in the cross direction are similar to properties in the machine direction. It produces a 100-g sheet that’s stronger than a single 100-g sheet. As Korsnas’ Torsten Sondell puts it: “It’s like adding one plus one but getting a total of, say, two-point six instead of just two.”
However it’s made, Fearns appreciates the impact of the Korsnas bag on his operation. The triple seal on the new bag means less damage to product due to moisture ingress. And it comes at a discount. “The new bags are roughly 30 percent cheaper than the valve bags we had before,” says Fearns.