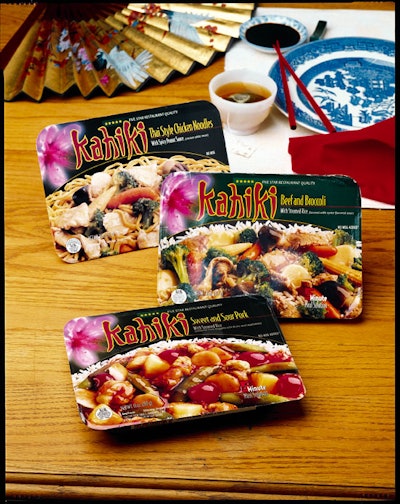
Hands-on packaging equipment often brings to mind the image of a slow, tedious process. But at Kahiki Foods, Columbus, OH, that’s hardly the case. In fact, the company runs its new rotary sealer at speeds averaging nearly 40 packs/min, doubling the top output of a sealer it had previously used. Kahiki’s line includes six different 11-oz Asian dinners that were introduced a year ago.
When Kahiki Foods installed the new sealer in September, it became only the second company (by just a few weeks) to employ the new RHS-6 rotary heat-seal machine from Gralex (Westerville, OH).
Operators fill the cooked foods into preformed trays and load them onto the rotary machine that automatically seals a paperboard lid to the trays. Food is hand-filled into Pressware® trays from Pactiv (Lake Forest, IL), formerly Tenneco Packaging. The 24-pt SBS board includes a clear polyester extrusion coating on its top flange area, as well as on its food-contact interior. The exterior is flexo-printed in three colors with a proprietary overcoat that resists external moisture.
The specialty Mylid™ lids come from Print Design & Graphics (Newcastle upon Tyne, England). Recently, Print Design & Graphics began shipping the lids directly to Kahiki Foods. Before that, the British converter had been distributing its lidding material through Pactiv.
The lid is 14-pt SBS with a proprietary film lamination that seals well to the tray, yet allows easy peel-off once the pack comes out of the conventional or microwave oven. Consumers place the tray into the oven. There’s no need to peel back part of the lid because as the product heats, the steam generated during the process loosens the seal area, permiting the tray to vent.
Alan Hoover, Kahiki Foods’ senior vice president of sales and marketing, explains: "When these frozen food products get hot, they release steam and moisture. When that occurs, a corner of the lid begins to lift to allow the steam to vent. That also makes the lid easy for consumers to peel off. Another key feature about the lid is that it peels off cleanly, without any fiber tear."
Hoover estimates that the use of the paperboard tray and lid, as opposed to a three-piece package consisting of a tray, film lid and folding carton, "saves us 20 to 30 percent in costs. We don’t have any equipment that erects and fills cartons, and purchasing such a machine would have cost us a lot more than buying the Gralex machine. And we don’t have to buy cartons. So overall, it’s less expensive to package the new line in a paperboard tray and lid."
Need for equipment
For the better part of a year, the new 11-oz Asian dinners were packaged on a machine that had been purchased about two years ago to seal lids to trays holding 39 oz of product. While it still is used for the larger size, it wasn’t well-suited for the new product line.
"One, we were only able to seal up to 20 trays a minute on it," says Hoover. "The other was that the machine’s supplier was based in Canada, and it was a very expensive venture to bring someone down to Columbus to keep the machine rolling. That vendor does a nice job and sold the machine to us at a reasonable price. But when we looked at the Gralex machine, we saw a machine that could greatly improve our line speed and output. And Gralex is only 20 minutes away, so that took care of our service concern."
Supplier connections
Before joining Kahiki Foods in May, Hoover spent 21 years working for packaging suppliers, the last 14 of which were at Pactiv (now Pactiv). "When I was there, I sold the trays to Kahiki. We also worked with Gralex, and we said to them, ‘You really ought to consider making machinery that can seal trays at maybe 20 to 40 per minute, and at a price tag below six figures.’
"At that time, you really only had two choices," he recalls. "You could buy a machine that was hand-operated and only did six a minute that cost less than $7ꯠ. Or you’d spend in excess of $100ꯠ for a high-speed machine. There wasn’t much in the middle." With the RHS-6, a new option became available for Kahiki Foods.
Hoover says he saw the machine run at Gralex’s lab "about a half-dozen times." He then brought in Kahiki Foods’ management. "We looked at it, and in about 30 minutes decided it was exactly what we needed."
Of course, economics played a central role in clinching Kahiki Foods’ decision to purchase the machine. Hoover’s relationship with Gralex helped the company purchase the machine at a favorable price. With all components, the complete unit sells for just under $80ꯠ.
Hoover is more than happy to relate the story of the RHS-6’s installation at Kahiki Foods’ frozen food facility in Columbus. "They delivered the machine to us September 10, 1999," he explains. "I walked in at about 10:30 in the morning. It never entered my mind that it would be in operation, but it was already running at the speed we wanted, which is about 36 a minute. It looked like the scene from the famous "I Love Lucy" episode because we had people having to keep pace with a machine running about twice as fast as the one they were used to running." It should be noted that the new sealer can be programmed to operate at three different speeds.
Efficient operation
The new line of Kahiki dinners is packaged at a 7ꯠ sq’ USDA frozen food facility located next to the Kahiki Supper Club in Columbus, an award-winning restaurant. Some entrees on the restaurant’s menu served as the "inspiration" for the new Kahiki dinners.
For the short term, Hoover says operators use an old hand gun to apply tiny pressure-sensitive paper labels with Julian dates to the tray bottoms. "The labels aren’t placed where they’ll affect graphics, but it’s a very laborious process, and I’m hoping that in the next few months we’ll install machinery to put the date code on the side of the tray."
At the facility, the packaging process begins as Kahiki Foods "associates" hand-load rice, meats, vegetables and sauces into trays on a belted conveyor. Trays are conveyed downstream to the RHS-6. The machine includes a rotary turntable. Machined into the top of the turntable are six recessed areas referred to as carriers. Spaced at specific intervals on the circular turntable, each carrier accommodates two cavities that hold two filled trays as they rotate from station to station on the machine. The turntable and carriers are made from anodized aluminum; much of the rest of the machine is stainless steel.
Operators place two filled trays into the two open cavities on the first carrier. The intermittent-motion machine indexes the two trays 1/6 of a revolution to the second station. Currently, this station is a spare that could be used in the future as a second tray-loading position if Kahiki Foods deems that necessary.
The turntable indexes another 1/6 of a revolution to the third of six stations, where lids are delivered to the filled trays. Photoelectric sensors are used at this stop to detect two filled trays. Once they’re detected, a vacuum lid dispenser, at this station, uses vacuum cups to pick lids from two magazines. (If a tray is not detected in either cavity, the machine will not place a lid in either of the two cavities.)
The mechanical dispenser delivers the two lids down onto the two product-filled trays. Accurate placement of the lids on the trays is ensured by a series of dowel pins that are machined into the carrier, along the borders of both tray cavities. The dowel pins help the lids remain in position on the tray as the turntable indexes to position four, where the sealing is done.
Forceful sealing
The C-frame sealing unit, according to Gralex, functions like a pneumatic punch press. Mounted to the unusual frame is a steel plate that’s attached to an air cylinder. The plate includes cartridge heating units in the machine’s upper tooling. After sensors determine that both tray and lid are in place in both cavities, the sealing process initiates. (If sensors do not detect lidded trays in either of the two cavities on the carrier, the sealing function will not be engaged.)
To seal the tray, the cylinder brings the steel plate into the exact position on top of the lidded, product-filled trays. The heating units are then used to simultaneously heat-seal the two lids to the two trays.
The seal is made using a combination of pressure, heat and dwell time. For the Kahiki line, however, the pressure portion of the equation is vital. The thickness and insulating property of the paperboard lid, coupled with the fact that the lid includes printed copy on the area that needs to be sealed, makes this application rather challenging.
According to Gary Alexander, Gralex’s CEO, pressure, temperature and dwell time are interrelated. In other words, if temperature is decreased, dwell time or pressure have to be increased.
To avoid scorching the printed lid, temperatures "are kept relatively low compared to some machines," says Alexander, who estimates the temperature for this application at about 350°F. Dwell time is also kept to a minimum to help prevent damaging the print. Presumably, a shorter dwell time hastens sealing speeds.
"The way we compensate for the lower temperatures and short dwell times," Alexander explains, "is by using a tremendous amount of force—in the neighborhood of 10ꯠ pounds."
Once the two lids are forcibly sealed to the two trays, the steel plate and heaters return to their home position for the next two trays. The sealed packs are indexed on the turntable past a cooling station. Kahiki Foods’ Hoover explains the significance of the fifth station: "We learned at Pactiv that the lids need anywhere from two to five seconds to cool from the heat before they’re ejected, so this part of the process is important."
Also important to achieving a good seal is the sixth and final station on the turntable. At this ejection station, pneumatic cylinders drive a mechanical device that lifts trays up about a foot from their two cavities on the carrier. The device tilts the two trays on roughly a 45° angle, and they descend along a short product slide onto a discharge conveyor. The cylinders then retract to their home position.
The ejection method differs from some discharge devices that use vacuum cups to pick up filled trays by their lids, a procedure that could possibly disturb the seal. The combination of time and gentle handling allows the seal to completely cure.
Kahiki Foods associates load eight trays into a corrugated shipping case, which is automatically taped top and bottom on an older machine. Cases are manually palletized, stretch-wrapped by hand, with pallets delivered to frozen storage. Frozen pallet loads are shipped by truck to grocery retailer distribution centers around the country.
Quick payback
Kahiki is a Polynesian name that translates in English to "sail to Tahiti." All six Kahiki meals sell for $1.99 to $2.69 at supermarkets, carrying a one-year shelf life. The meals will likely replace another product line called General Tsao, named after the company’s president, Michael Tsao. That line, Hoover says, is currently sold at only one or two supermarkets and may be discontinued. That decision seems to indicate that Kahiki Foods has high hopes for the new line. Hoover estimates that by the end of the company’s current fiscal year, the line could account for 50% of the company’s total frozen food sales.
Those strong sales helped Kahiki justify the equipment investment. "We paid for the carriers right off the bat. The rest we’re paying off during an 18-month period," he concludes.
In a hurry? Request more info via Web-based reader service by clicking on company name.
Or you can jump right to their Web site.