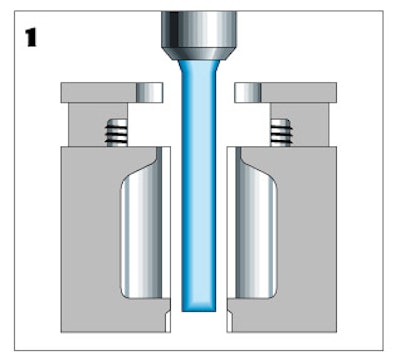
Vigorous sales growth of Dey Laboratories' liquid respiratory therapy drugs led this long-time user of blow/fill/seal technology to invest in three of the latest-generation aseptic b/f/s machines made in Germany. The machines, supplied by rommelag USA (Fords, NJ), are used to fill liquid inhalants into 3- and 5-mL single-dose, low-density polyethylene vials. The vials are molded (with integral twist-off caps), sterile-filled and sealed in one process at the Napa, CA, pharmaceutical company, which is affiliated with Merck KGaA of Germany.
Blow/fill/seal machines have been popular among pharmaceutical packagers because they eliminate the purchasing of separate containers and closures. The process also eliminates the labor involved with unloading, sterilizing, and filling and capping.
"We have several suites of rooms, and operators move around, visiting each one," says Ed Fried, director of manufacturing. Dey has used rommelag equipment for over 10 years, and 12 machines are currently in production.
But the automation comes at a price. Historically, b/f/s machines have been slow, since molding is the bottleneck. But with Dey's latest Bottlepack® 360 machines, output tops 180 vials/min, due to an expanded mold configuration of 40 vials per cycle instead of 30 previously-a 33% boost in output. The higher-output machines also cost more, too: $2.5 million apiece, versus about $1.5 million each for the previous models.
Dark/white side sterility
These latest machines are rommelag's first in the U.S. to feature what it calls a dark/white side configuration. The machine is built so that the support and auxiliary equipment maintenance points of the machine are segregated on a non-sterile side of the machine for easier servicing. The machine straddles a dividing wall in Dey's clean room that separates the clean room (Dey declined to identify the sterility level) from the non-sterile areas. "Accessing the machines is much easier," says Fried. "We can maintain many of these systems without getting gowned up and entering the clean room."
Another convenience is a redundant control panel mounted outside the clean room. It permits operators to check the machine and make adjustments, without having to enter the clean room. "For example, if we need to adjust vial wall thickness or fill volume," says Fried, "we can make adjustments through the remote control panel."
The new machines allow automated clean-in-place (CIP) and sterilize-in-place (SIP). That's made possible in part by a totally closed fluid path. "Between the formulation tank, the pipes leading to the machine, and the machine itself," says Fried, "there is literally a sealed network through which we can continuously pump pressurized cleaning fluid or steam. We don't have to take the machine apart, sanitize it, and reassemble it," says Fried. He estimates that CIP/SIP takes about four hours in an automated, mostly unattended process. Apart from "a very little bit" of manual operation, the most that's required is for an operator to occasionally monitor the control panel. That's compared to six to eight hours of manual labor required on the older machines. "So we can do it quicker with less labor and more assurance of consistency," says Fried.
Two machines in one
The Bottlepack system is actually two molding/filling/sealing machines-one on the left, the other on the right, flanking four parison extrusion dies. Each side alternates forming, filling and sealing 20 vials at a time, and a complete cycle lasts 13 seconds, with 40 vials-20 from each side-produced each cycle.
The process starts as resin is continuously extruded through four parison dies at a temperature of 320F. One set of molds slides and closes around the extrusions. A knife at the top of the mold cuts the extrusions and the molds retreat to allow the other set of molds to slide in around the newly forming extrusions.
Inside the first mold, a slight vacuum is applied so that the plastic conforms to the shape of the mold cavity. (Fried notes that Dey's vials are small enough to rely on vacuum forming without having to resort to blow molding. Blow/fill/seal machines rely on blow molding for applications that require larger container sizes, according to Fried.) The molds create four "cards" of vials, each card consisting of a frame of five individual vials.
Once the containers are molded, 20 filling needles descend into the open tops of the vials, while still in the molds. The aqueous product is dispensed for a preset time duration from a reservoir whose contents are kept under pressure. This time/pressure filling arrangement results in a very high filling accuracy, according to Fried, though he wouldn't reveal specifics. "Fill accuracy has been significantly improved over the years with rommelag," Fried says.
Both rommelag and Dey take sterility very seriously, relying on sterile filling conditions to achieve an aseptic fill. "We cannot terminally sterilize like in an autoclave because the plastic would melt," says Fried. "Therefore we need a sterile vial and a sterile filtered liquid and the fill area purged with sterile filtered air to achieve an aseptic fill."
Once filling is complete, the bottles are ready to be sealed. A secondary sliding head mold moves in around the exposed neck of the bottle, which protrudes from the main mold body. There the plastic is molded shut. The result is a totally integral one-piece container.
Next, a punch tool removes the flash. Although Dey sells the flashing to recyclers for non-pharmaceutical applications, it still represents a sizeable portion of material that becomes scrap. "We've worked with rommelag to minimize [flash]," says Fried. Dey is currently not permitted under its current FDA product license to reuse the scrap, though "in the future we may address that," Fried says.
Finished five-vial cards then emerge from the machine onto a takeaway conveyor. The packages are quarantined for seven to 14 days while they are tested by Dey's quality control departments. After quarantine, five-vial units are pressure-sensitive labeled, one label per vial, all five vials at once. Anywhere from five to 24 five-packs are then machine-loaded into chipboard cartons, which are then checkweighed, laser-coded and packed into corrugated shippers. Following final quality control testing and quality assurance review, the products are released for distribution.
The new machines have been running successfully since the beginning of the year. Even so, production capacity will need to increase even more. Dey Labs says it has relied on rommelag technology since 1985 and plans to continue the relationship as it further expands its manufacturing capacity.