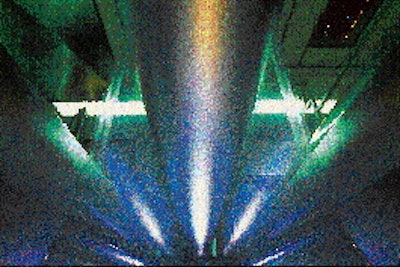
One is a tiny blister holding a single pharmaceutical tablet covered by a push-through foil lidding. Another is a large deep blister holding a sizable hardware product like a bicycle pump backed with heavy paper. What these two diverse product packs likely have in common is that the thermoformed blister, regardless of size, is made from calendered plastic sheet.
Manufacturers of calendered plastics typically ship rollstock or sheets to thermoforming companies or directly to packagers that thermoform the material before filling the blister and sealing it.
Plastics are usually calendered into film or sheet with thicknesses ranging between 2 and 45 mils, but primarily in the 7.5- to 30-mil range. Polyvinyl chloride is the most common material processed on calendering equipment. Blended polyesters and acrylonitrile butadiene styrene sheet are also produced on calendering lines.
Characteristics
Consistent thickness and economics are the primary advantages that the calendering process brings to the table. Consistent thickness translates into greater machinability during thermoforming since heating and forming can remain constant throughout the length of the roll. Plastics that vary in thickness require more adjustments and consequently, downtime.
Since processors calender mass quantities of plastic, at healthy output rates, there are generally economic advantages for purchasers of the materials. "Calendering is a much faster processing operation than extrusion," points out David Flynn, vp of operations for thermoformer Crystal Thermoplastics (Cumberland, RI). "That means there are economic advantages in purchasing calendered sheet." Crystal Thermoplastics, says Flynn, "uses sheet in the 10- to 40-mil range for blisters that you might find in Radio Shack or other retail stores for hardware, batteries, electronics, and so on.
"We order calendered material by the truckload," he explains, "with each truckload carrying about 40ꯠ pounds. About 99 percent of the material we buy is calendered. Over the years, we've only ordered extruded PVC a few times and that might have been because we needed a quick order of about 1ꯠ pounds. There's no way you'd use such a small amount of material on a calendering line."
Flynn notes that "the few times we did opt to use extruded material, we'd try to call the supplier back only to learn that the company was no longer in business." The point is that it's difficult for suppliers of extruded sheet/film to compete with those using the calendering process, at least in terms of sheer volume.
Self-supplied
One of the more noteworthy developments in calendering (see sidebar, p. 30) is thermoformer Alloyd's (DeKalb, IL) adding equipment for captive production. It may be the only thermoformer with its own calendering line.
"Calendering lines handle rather large volumes," says Dale Meyer, president and chief executive officer for Alloyd. "It doesn't make sense economically to install a calendering line unless you use enough material to justify it. In our case, we use substantially more material than the output of one calendering line, so it benefits us."
In many cases, the use of calendered plastics is so well established that users have a difficult time describing its advantages. Mary Shepard, a senior research associate for American National Can's (Chicago, IL) Neenah, WI, plant, provides such an example.
"We've used calendered sheet for so long that it wouldn't be fair for me to compare its benefits to that of extruded materials," she says. "But we do benefit because the calendered material is so thermoformable. There are few variables, the gauge control is consistently excellent, and optically the material has a glass-like gloss."
Examining the process
A calendering "line" (see diagram above) usually involves blending resin with specific ingredients that may include: stabilizers to prevent thermal degradation; modifiers for clarity, heat stability or opacity characteristics; pigments to provide color; lubricants and processing aids to enhance slip and denesting properties; improved thermoformability; anti-static agents; UV inhibitors; and flame retardants.
Mixed ingredients are then plasticized or "fluxed," often in a kneader or planetary gear extruder. Through heat, shear and pressure, the dry powders are fused to form a homogeneous, molten mixture that's constant in temperature and uniform in composition.
The extruder feeds the material in a continuous process to the top of the calendering section of the line, in between the first two chrome-plated calender rolls. Typically, heated rolls are configured in an "L" shape (see diagram on bottom of p. 28). These cylindrical rolls vary in size to accommodate different film widths. Rolls have separate temperature and speed controls.
The material proceeds through a gap between the first two rolls. Rolls rotate in opposite directions to help spread material across the width of the rolls. The material winds between the first and second, second and third, third and fourth rolls, etc. The gap between rolls decreases in thickness between each of these rolls so that as the material proceeds, it is thinned between the sets of rollers. Scanning equipment traverses the web to measure thickness during this process, which is carefully controlled by computers.
After passing through the calender section, the material moves through another series of rolls where it is stretched and gradually cooled. The material is carefully controlled as it proceeds through these rolls to manage shrinkage and tension, as well as cooling. All of these factors help optimize thermoforming performance. The cooled material is then usually wound into master rolls, which can later be slit into customer-designated widths, or cut into finished sheets.
Long history
"Plastics have been calendered since the ᅎs in Europe, and in the U.S. since the ᅢs," estimates Tom Goeke, chief operating officer for Klockner Pentaplast of America (Gordonsville, VA). Klockner is recognized as one of the three major producers of calendered sheet and film, along with Nan Ya Plastics U.S.A. (Wharton, TX) and American Mirrex (Delaware City, DE), whose stock was recently acquired by Sheboygan, WI-based Vinyl Plastics Inc.
With so much history behind it, why haven't we heard more about the calendering process? One reason is that much of the output from calendering lines is used in non-packaging applications.
Michael Buchanon, product manager at American Mirrex, offers another explanation. "In comparison to the number of extruders in operation, there are very few calenders." There's a good reason for that, too. A complete calendering line, including equipment, land and plant space, can exceed $30 million.
Gauging demand
That kind of financial investment requires a definite commitment by calendered plastics makers to the market. How sizable is the market? How has the use of calendered plastics grown, and what does the future hold for its use in packaging?
The Society of the Plastics Industry's (Washington, DC) Committee on Resin Statistics, Annual Major Markets Survey shows that in the five-year period between 1991 to 1995, PVC consumption increased from 711 to 841 lb. What percent of that is attributable to calendering, though, is not identified. As to the distribution of PVC by major market, packaging progressed from 546 million lb in '91 to 743 million lb in '95.
"We've steadily increased our use of calendered materials, and we see that continuing," says ANC's Mary Shepard. Alloyd's Dale Meyer concurs, saying, "We see the market for calendering film growing, not at a dynamic pace, but rather at a steady one."
The comments from these thermoformers reflects something that we've noticed at Packaging World. In the past six months, we've received a handful of press releases denoting calendered film. And while these releases are too few to indicate a definite trend, they do point to the fact that thermoformers see the marketability of calendered plastics. At the least, calendered plastics' use in packaging represents a development that's worth keeping an eye on in the future.