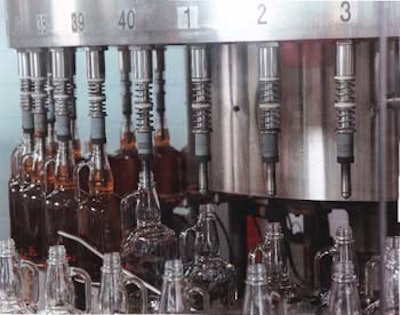
When it came time to modernize a 25-year-old bottling line in Clermont, KY, Jim Beam Brands anchored the new line with something previously untested in its three U.S. plants: a filler/capper monoblock.
"It's a first for Jim Beam Brands," says project engineer Pete Schamer. The 40-valve filler on the monoblock system was supplied by Horix (Pittsburgh, PA), while capping is done by a 10-station Zalkin rotary capper from Fowler Products (Athens, GA). The line is dedicated to four brands of distilled spirits in 1.75-L handled glass bottles.
In selecting components for the monoblock system, which is the very heart of the new line, Beam's engineers relied on past experience, says bottling maintenance manager Don Sympson.
"Having many Horix fillers in the plant gave me a benchmark for comparison with other filling equipment," says Sympson.
But it wasn't only past experience that led Beam management to the Horix filler.
"We selected Horix for a variety of reasons," says Johnnie B. Colwell, bottling operations manager. "They suggested a machine that was simple in design, adapted well to our space and floor-weight requirements, and had a tank that would fit our ceiling-height requirements. They also offered adequate speed and anti-foaming fill tubes, and the machine adapted easily to the capper we wanted."
The Zalkin turret capper features magnetic chuck capping heads that provide reliable control of torque, which is tested off-line every two hours. Beam has been especially pleased by torque consistency, and by the monoblock pairing in general. "The two machines work well together," says Sympson. "I have minimal problems with synchronization, starts or stops."
Synchronous handling of the 1.75-L glass bottles is all the more important because at the same time the new line was being designed, the custom handled bottle was lightweighted by 4 oz. It now weighs in at 32 oz when empty. The monoblock arrangement reduces the potential for jostling of the lightweighted bottle because the bottle is closely controlled between filler and capper. Bottles move smoothly through a single transfer starwheel in passing from one turret to the other.
Also helping to ensure synchronization is positive gear-to-gear power transmission between the starwheels, the filler's turret and the capper's turret. Finally, the bottle infeed conveyor was integrated into the monoblock's main drive gearing. As the filler speed ramps up or down in response to changing line conditions, the conveyor remains synchronized to the filler.
Additional measures
Measures to protect the lightweighted bottles aren't limited to the filler/capper block. Downstream, just ahead of the case packer, bottle conveying is divided into zones to minimize the buildup of back pressure.
"Instead of, say, a straight sixty-foot conveyor length, we break that into several separate conveyors," says engineer Pete Schamer. "So when the lead section is full, a photocell is blocked. That signals that particular conveyor section to stop and also blocks the progress of additional bottles from the next conveyor section until the photocell clears."
Yet another measure of soft handling is contributed by the Krones (Franklin, WI) slat lane divider just ahead of the case packer. It gently guides bottles into the two-lane orientation required by the drop packer.
Filling speed on the new Line G is 180 bottles/min, up from 100/min on the old line. Because Beam now can produce almost twice as many cases per shift on the line as it could before the modernization, the line only runs three days out of five. But in time, says Sympson, it's possible that other bottle sizes could join the 1.75-L bottles on Line G, and when that happens the additional capacity will be more valuable than ever.
Not that the new line isn't making important contributions already. "It wasn't just a matter of speed, but quality issues and reduced labor costs, too," says Sympson. More consistent fill levels and more accurate label placement are among the quality issues that have been addressed by the new equipment. And while four operators were needed on the old line, now there are three, even though output is almost doubled.
Actually the term "operators" has been replaced by "technicians." Whatever name they go by, they had to undergo some serious training as the installation proceeded. For instance, troubleshooting of the PLC-controlled equipment on Line G begins at touchscreen units. Technicians use computerized diagnostics to pinpoint problem areas, says Sympson.
"The new line was designed to use diagnostics and sophisticated software to maximize production efficiency," says Sympson. "This allows greater flexibility and improves quality as well as efficiency. Our old line involved 'reaction' responses to line problems. This proactive role involves the interpretation of causes of downtime through the software system, helping our Line G TQM [Total Quality Management] team make fact-based changes to minimize downtime. It represents a new technology and skill level for our employees."
No-tool changeover
The Horix/Zalkin monoblock was designed with a no-tool changeover feature. Currently, with the line dedicated to 1.75-L bottles, the main use of the quick-change feature comes during routine maintenance operations. All the same, bottling operations manager Colwell is glad the no-tool capability is available in the event another size is introduced at some point in the future. As he puts it, "You never know what the market might bring."
Well ahead of the monoblock is where Line G begins, with a machine found on packaging lines throughout the Beam organization: a decaser from A-B-C (Tarpon Springs, FL). It removes the corrugated reshipper so that bottles, supplied by Anchor Glass (Tampa, FL), are conveyed neck up toward the orienter. Reshippers then are transferred to the end of the line.
Bottles move next to another Jim Beam first: a bottle orienter from Krones that uses a machine vision system to identify the orientation of each bottle's handle and then rotates the bottle accordingly (see sidebar). After the orienter is a U.S. Bottlers (Charlotte, NC) 32-head rotary bottle cleaner. It inverts each bottle and sends an air blast inside to agitate particles so they can then be vacuumed out.
Filling is next. The Horix 764-40/10 gravity/vacuum filler has an "annular" filler tank shaped like a big donut measuring some 80" in outside diameter, 70" inside diameter. A small tank in the center of the ring receives product from the processor and distributes it through valves that radiate out like spokes in a wheel. Compared to filler bowls that don't have this ring-style shape, the annular filler bowl holds less product at a time. This minimizes product exposure, says Horix, and helps prevent proof loss in the distilled spirits.
Product foaming during filling is minimized by Horix's Screen-Flo valve. Reduced foam permits faster filling with fewer valves, which in turn reduces maintenance and parts costs.
Also, minute fill level adjustments can be accomplished simply, by raising or lowering the filler bowl with a lever located on the tank motor controls. Fill valves are attached to the filler bowl, so if the bowl is raised, the air vent port in each valve is raised along with it. That means liquid will flow longer before the air vent port is covered and liquid flow stops. Conversely, lowering the bowl lowers the position of the air vent port, causing liquid flow to stop sooner.
Inspection station
Leaving the filler/capper monoblock, bottles pass through a Filtech unit from Industrial Dynamics (Torrance, CA) that checks product level in each bottle and also checks for high or missing caps. Bottles that fail inspection are rejected.
Paper labels are cold glue-applied by a Krones 19 Series Solomatic labeler designed to handle the difficult challenge of applying front, back and neck labels. Equipped with 20 bottle plates, the labeler is capable of speeds as high as 250 bottles/min. But Beam's line tops out at about 180. Colwell has been impressed by the accuracy and reliability with which the labeler operates.
"That's a difficult application, especially on the neck," adds Colwell. "There's not much room for error."
Leaving the labeler, bottles are conveyed through the Krones slat lane divider into a drop packer supplied by Standard-Knapp (Portland, CT). "It's built like a tank," says Schamer when asked why it was selected for the new line. "It does a fine job."
Immediately after the case packer is a hot-melt case sealer from A-B-C and then a second Filtech inspection system that checks for missing bottles. Cases then pass through an ink-jet system from Marsh (Belleville, IL) that applies date and production codes to one side of each case. With that the case is conveyed to palletizing at a remote station.
The line has been running steadily for just over a year now. The planning and design stage that preceded installation is a classic example of packager/supplier teamwork.
One big help was assigning B&J Machinery (Cincinnati, OH) as coordinator of the installation. Not only did the firm help orchestrate the complex project, it took shipment of several suppliers' machines for mechanical synchronization and preassembly.
"B&J Machinery integrated the equipment and ran a series of debugging tests to determine final changes prior to shipping the equipment to our facility," says Sympson. "We went to their plant for a test run and final inspection." This preassembly step paid big dividends when the equipment was moved to its home in Clermont. "Everything came off without a hitch," says Sympson.
Colwell concurs. "The installation was smooth, with production starting right on schedule."