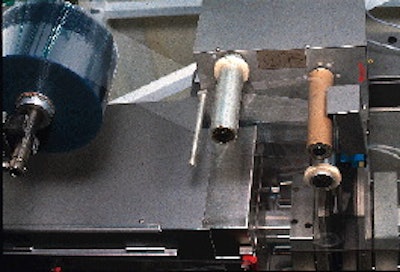
To out-source or to package in-house? That was the question pondered by Gumtech Intl., a Phoenix, AZ-based maker of chewing gums containing vitamins, minerals and/or dietary supplements. These gums are also referred to as nutraceuticals, combining the words "nutritious" and "pharmaceutical" to describe their "functions."
"Whereas you buy most chewing gums for taste, or to freshen your breath, these gums serve a purpose," explains Gary Kehoe, Gumtech's chief operating officer. "They provide functions such as helping to deliver antioxidants to your system, or acting as an appetite suppressant, or giving you energy for working out," he explains.
From its inception six years ago until last spring, Gumtech relied on a contract packer to pack its nutraceutical gum products using a thermoform/fill/seal line. Last spring Gumtech invested in a Compacker-3 thermoforming machine from Klockner Bartelt Medipak (Clearwater, FL).
The machine now runs 12 hours/day, five days/week, producing 14 gum products. These are sold over-the-counter from pharmacies, as well as in gum sections of drug stores, supermarkets, chain stores and discount merchandisers. Shelf life is one or two years, depending on the product.
Gums are marketed in three pack configurations: square packs with either 10 or 12 gum pieces, each piece within a separate blister, or a rectangular pack containing 12 pieces within 12 blisters. Depending on the product, the machine produces as many as 135 packs/min.
Before adding the machine, Gumtech's products were packed at times when they fit into the CP's schedule. "When you work with a contract packager, there's always a lead time," notes Kehoe. "That was usually two to three weeks.
"We elected to thermoform the blisters in-house to gain production flexibility and improve the quality of our package and product," he says. "We can decide that if we're low on a particular product we can schedule it to run right away.
"We purchased three sets of thermoforming tools for our different product formats," Kehoe adds, "all from Klockner, all built to our specifications. We can do a tooling change in about 30 minutes, so we can change over to run a different product later that day or the next day."
Those advantages more than offset purchase costs and training expenses. "Yes, we did have to purchase a machine, and we sent two people to Klockner in Florida for a week of training," admits Kehoe, "but we expect to earn about an 18-month payback, which we feel is quite reasonable."
Barrier qualities
Products are filled into blisters formed from a web of Penta-pharm® 170/01 pharmaceutical-grade polyvinyl chloride from Klockner Pentaplast of America (Gordonsville, VA). Sheet thicknesses are 7.5 or 10 mils, depending on the product.
"Our use of sensitive vitamins and ingredients requires that we protect our products with blister packs," says Kehoe. "Vinyl film makes both an affordable and functional barrier. We chose the Klockner material primarily because of its barrier against moisture."
Gumtech tried another grade of vinyl with the CP-3 before switching to Pentapharm. "But we noticed that the material didn't track well on the machine," he says. "It had a tendency to wander, leading to indexing problems. Since we switched to the pharmaceutical-grade film, we've noticed about 12-percent reduction in downtime associated with indexing problems."
Tf/f/s process
A motor-driven powered un-wind drives the PVC rollstock into the intermittent-motion CP-3's preheat station. Upper and lower plates heat the material until it's pliable. Material then indexes into the forming section. An aluminum plate is mounted within the upper section. Air is blown downward through holes within this plate, causing the base material to conform to the female mold in the bottom of the forming section. No plug assist is necessary, and no vacuum is drawn. Both the preheating and forming sections of the machine are water-cooled.
The formed sheet then indexes to the filling zone of the machine, where gum pieces are filled into formed cavities by a Klockner Bartelt Medipak brush box system. Product is filled in 10- or 12-counts in the machine direction for each cycle. The number of blisters per cycle across the web depends on the forming tool being used.
Gums are coated and protected with waxes and resins before proceeding through a sorter that culls out odd-sized pieces. Quality gum pieces are suspended in a woven polypropylene sack supported by a stainless steel frame. Gum is conveyed along a vibratory feeder that delivers the product through two stainless steel hoppers. Sensors detect volume within the second hopper to maintain the proper product level.
Another vibratory feeder delivers gum to the brush box system. The system includes four planetary gear drive boxes that use a series of brushes to orient the pieces into the formed blister cavities. The filled thermoforms pass by a Klockner MediVision inspection system that checks for missing or damaged product.
Next, foil lidstock unwinds to the sealing station. The 0.0008-mil unprinted blister foil lidstock is supplied by Hueck Foils (Man-asquan, NJ). The foil provides excellent water and vapor barrier. As the foil rollstock unwinds, an Adolph Gottscho (Union, NJ) platen printer prints the Gumtech logo, lot number and expiration date onto the foil. The foil is then hermetically heat sealed to the base web.
Depending on the product, blisters may or may not be perforated by cam-driven knives. Kehoe says blisters are perforated when the specific product calls for more than one piece of gum per "serving." That allows consumers to easily tear the recommended number of pieces from the blister and carry them separately rather than carry the entire carton. "The CP-3 was, and remains, the only machine that gives us the flexibility to produce either a perforated or nonperforated pack," says Kehoe.
A die-punch unit then punches out the individual blister packs from the web. Separated packs are conveyed to manual cartoning.
Kehoe considers the cartoning of these gums something of a work in process. "We're not completely sure which direction the market will take in terms of the packaging format consumers prefer. We have paperboard sleeves and cartons." Presently, a Tisma (Elk Grove Village, IL) machine automatically puts two blisters at a time into a sleeve.
"We're waiting to see if our large, economy-sized boxes will be popular in cartons," he continues. "We will buy an automatic cartoning unit if consumers determine that's the proper format for the product," he continues. "But since this is a newer market segment, we're not sure. It doesn't make sense to commit the dollars to buy a cartoner until we know for sure what the best packaging format will be."
Cartons are loaded by hand into corrugated cases, stacked on a pallet and manually stretch-wrapped prior to shipment. Kehoe estimates that 65% of shipments are within the U.S., with the balance distributed to more than 30 different countries.
Market-driven products
The CP-3 is used for products such as: CitrusSlim for weight control, DentalHealth for oral hygiene, VitaACE with antioxidants, Repose PMS relief for women and Gumtech's original BuzzGum with natural guarana for alertness and energy. Two new products were scheduled to be launched this year, one an antacid gum, another for allergies.
According to company research, gum provides a more effective delivery system than pills or capsules. "Gum offers better and faster absorption into the body," Kehoe says, "because it is less altered by digestive juices and less diluted than pill and capsule delivery systems."
Delivering gums to market is a process by which Gumtech now enjoys greater control, thanks to the tf/f/s machine. "We liked the idea of a medium-output, low-cost machine like the CP-3 giving us the production flexibility to keep up to date with changing market demands for our range of new and existing products," Kehoe summarizes.