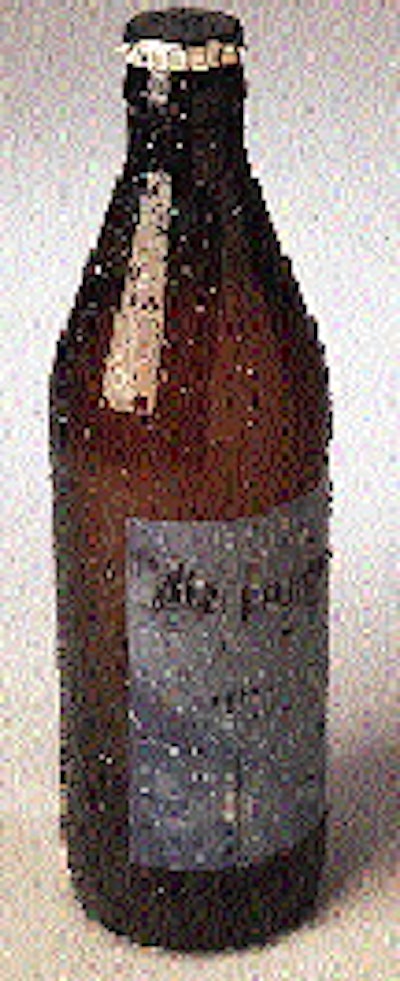
Polyethylene naphthalate (PEN) continues to intrigue food and beverage marketers. They like its clarity, resistance to heat and chemicals, and gas barrier properties (see PW, July '95, p. 26). With the recent U.S. Food and Drug Administration approval of PEN homopolymer for food contact applications, U.S. firms are said to be chomping at the bit for similar approval of PET/PEN blends and PEN copolymers. Such approval will allow users of PEN to dial in only as much of the costly material as they need, thus keeping packaging costs in line.
Near-commercial applications involving PEN are surfacing in greater numbers. Also, steady progress in the commissioning phase of Amoco's naphthalene dicarboxylate plant in Decatur, AL, makes it clear that sufficient feedstock for production of PEN will be availabe for future applications involving large volumes. In the meantime, a look at a few of the recent PEN containers to emerge provides a good measure of PEN's progress.
Perhaps the application closest to true commercialization is the jam "pot" filled by Arran Provisions Ltd. This small manufacturer on the Scottish island of Arran is an established marketer of branded premium jams, traditionally hot-filled in glass jars. But recently Arran began filling single-serve salad dressings in PET containers for British Airways. Unlike the jams, the dressings can be filled at ambient temperatures, so PET is perfectly adequate.
Now Arran would like to grow its business with the airlines, and management believes that packaging its jam in a lightweight jar made of a PET/PEN blend could be the way to do just that. (In Scotland, as in the rest of the U.K., regulatory approval of PET/PEN blends for food contact has been issued.) The jar is injection stretch/blow molded on an integrated single-stage system by PET Partners (Etten Leur, The Netherlands). The PEN is supplied by Shell Chemical (Akron, OH), says PET Partners' Koos Gommars. But he declines to reveal the ratio of materials in the pellet-to-pellet blend. The empty jar weighs just 10 g, while the glass jar currently used by the airlines weighs 62 g.
PET Partners is financing part of Arran's project, which consisted of a 10ꯠ-unit production run. These units are being used by Arran for sampling purposes, not only in the offices of British Airways but also for other customers that may be interested. It's likely, however, that the airlines will see the strongest benefits in the jar since even the smallest weight reduction helps save fuel.
Supplier support
Also aggressive in promoting the filled jars are the three suppliers behind the jar: Shell Chemical, which provided the PET/PEN blend; Amoco Chemical (Chicago, IL), supplier of the NDC feedstock for the PEN resin; and blow-molder PET Partners. They helped Arran produce an elaborate windowed gift-pack carton holding four samples of the 28-g jams. These four-packs were unveiled at the Nova-Pack conference on polyester food and beverage packages sponsored by Schotland Business Research (Skillman, NJ), at interpack 96, and elsewhere. Copy on the back panel lists the three companies' contributions and points out that the jars are hot-filled at 85°C (185°F) by Arran.
Arran uses a 43-mm steel threaded closure on the jars, the same as its single-serve salad dressings in PET. A brightly decorated pressure-sensitive label includes a strip that runs over the edge of the cap and adheres firmly to the sidewall of the jar, thus providing tamper evidence.
A glass jar, by contrast, would not need the TE label. Its TE feature is the internal vacuum generated in hot-filled glass jars as headspace contracts during cooling. Theoretically, consumers are accustomed to listening for the "pop" that comes when this vacuum is broken. If they don't hear it, that's their evidence that the package is suspect.
The Arran jar, however, has no internal vacuum. Its sidewalls can't take the pressure. In fact, care must be taken to minimize or avoid creating an internal vacuum. Arran's solution is the injection of liquid nitrogen. The temperature of the hot-filled food product causes the nitrogen to evaporate, and in its gaseous state it becomes a counterpressure that cancels out most or all of the internal vacuum pressure.
While this counterpressure approach is certainly effective, some suggest that it compromises a food manufacturer's ability to use automatic seal inspection systems, most of which rely on a strong internal vacuum. Also gone is one's ability to hear the release of internal pressure that indicates seal integrity.
"That's not such a problem where a high-acid jam or jelly is concerned, because if spoilage occurs due to a bad seal it's likely to form mold, and that's not going to harm anyone," says Nina Goodrich of Guelph Food Technology Centre (Guelph, Ontario, Canada). "But what about a soup or some other low-acid food?" The possibility for growth of pathogens and resulting illness or death, she suggests, is certainly present in such cases if seal integrity is faulty, and consumers may not be forewarned by odor or discoloration.
Goodrich isn't saying that the liquid nitrogen approach isn't appropriate in some applications. There's certainly a precedent for it in noncarbonated fruit juices and teas hot-filled in aluminum cans. But at recent technical conferences she's been recommending that other alternatives should be explored. For instance, she thinks thermal stability in PEN containers can be maximized by paying closer attention to design features.
Forgotten lessons?
"Too many of the PEN containers I've seen haven't taken into account all that we've learned from hot filling of beverages in PET bottles," she observes. One specific lesson that should be explored, she says, is the use of stress panels to relieve pressure on a bottle's sidewalls. Or, she suggests, a flexible barrier lidding-foil, foil laminate, PEN film-could be heat- or induction-sealed to the container to become the equivalent of a stress panel; any sort of overcap could then be used for reclosure purposes. Goodrich also suggests that fill temperatures might be lowered slightly and the amount of headspace minimized as well, both of which reduce the internal vacuum pressure that's formed during cooling.
Goodrich and her colleagues at Guelph continue to test a variety of PEN applications in food packaging, including flexible films. At recent conferences she's shown a pouch made of 3-mil Kaladex®, the PEN homopolymer film from ICI Americas (Wilmington, DE), that was filled with carrot puree and then processed in a Lagarde steam air retort at 25°F for 40 min. "It retorted beautifully," says Goodrich. She adds that, judging by the number and variety of pouch-producing systems she saw at interpack 96, she's convinced pouches made of PEN could surface commercially before too long.
Goodrich believes that as soon as FDA clears PEN copolymers and PET/PEN blends for food contact, food companies will rush to market with new applications. She's already working on container trials to reassure food packagers that PEN can be handled in their processing, packaging and pasteurizing or retorting systems. "They know that marketing is going to want a PEN container yesterday as soon as approval comes," she adds.
Goodrich also thinks U.S. brewers are excited about PEN, and developments overseas suggest European brewers feel the same way. At interpack 96, for example, Greiner & Sohne (Kremsmunster, Austria) passed out samples of beer from the Mayr brewery, located near Greiner's Kremsmunster headquarters, that were packaged in half-liter refillable bottles made of Shell homopolymer PEN. While Mayr hasn't committed to marketing the bottle commercially, the interpack samples are a sign that commercialization of a PEN bottle for beer in Europe is probably not too far off.
According to Greiner marketing manager Kenneth Boldog, PEN appeals to European brewers because it appears to provide all the clarity, gas retention, and oxygen barrier needed to get beer through the distribution system. Yet compared to glass, it's shatter-resistant and light. He says a half-liter returnable glass bottle weighs between 420 and 500 g, while the same bottle in plastic is 40 to 60 g.
Customized shapes
Also attractive, says Boldog, is that PEN would allow beer marketers to differentiate their packages through customized shapes. Currently in Europe, not much more than label graphics can be used to set a beer container apart. With plastic bottles, customized shapes can be achieved more readily than with glass, says Boldog.
Greiner is working with brewers large and small in Austria, Germany, The Netherlands and the U.S., says Boldog, to develop 0.3- and 0.5-L bottles that contain various levels of PEN. He expects some of these bottles to be on retail shelves in three to six months.
Greiner's objective is to have them capable of withstanding 50 trips. Thus, the bottles won't come cheap. He estimates they'll cost between two and four times as much as glass currently used. But by all indications, he says, brewers are prepared to pay the premium. (For more on the Greiner bottle, see p. 84).
Elsewhere on the beer front, SIPA (Vittorio Veneto, Italy) this month completes a 9-month test of 100% homopolymer PEN beer bottles made of Trevira Polyclear N-100(TM) resin from Hoechst (Spartanburg, SC). SIPA produced 1귔 of the 25-g 0.33-L bottles on its own integrated injection molding/blow molding ECS system. The bottles were filled with beer and capped at IFBM Nancy (Institut Francais Des Boissons De La Brasserie Malterie), a beer institute in Vandoeuvre, France.
Brown beer bottles are popular in Europe. So SIPA worked with suppliers of colorants to develop a liquid color concentrate that can be added directly to the throat of the extruder via a reciprocal pump.
Also of interest is the closure, supplied by Rical (Dijon, France). Injection molded of polypropylene, it incorporates a liner that includes a layer of ethylene vinyl alcohol for oxygen barrier among its seven laminated layers.
Filled at 5°C (41°F), after one hour the bottles were placed in a 40°C (104°F) bath that was gradually raised to 65°C (149°F). The bottles remained at 65°C for 20 minutes of pasteurization, and then they were placed 12 per case for storage at 23°C (73.4°F).
Tests by IFBM Nancy included chemical analysis of the beer, carbonation, permeation and quality of taste. SIPA's Giorgio Masini presented an update April 16 at Bev Pak '96, sponsored by Directions 21 (Sarasota FL).
"In general, the results from the test have been extremely positive in terms of carbon dioxide content after both one and two months at 23 degrees C...when compared to the glass bottle references," said Masini. Both glass and PEN bottles were also tested after eight weeks at 40°C, which is the equivalent of two years at ambient temperatures. Masini pointed out that beer would normally not require anything more than a 12-month shelf life, but the accelerated test was performed anyway for the sake of analysis. In this test, Masini told his Bev Pak audience, "Both glass and PEN bottles show degradation in taste and aroma, although it is slightly more apparent with the PEN bottle."
Not showing any signs of degradation is the interest in PEN.
"We're getting a lot of opportunities to quote or advise on our ability to supply for some applications, and we're pursuing these aggressively," says Jim Caldwell of Eastman Chemical. Also occupying a chunk of Caldwell's time is the newly-formed Naphthalate Polymers Council, where he's joined by representatives from Hoechst, Shell, ICI and others. High on their list of things to do is developing an identifying mark so that consumers and sorters can recognize PET bottles easily and quickly; the FDA calls for this mark in its regulation permitting the use of PEN homopolymer for food packaging.
Also intrigued by PEN is Coca-Cola Co. The Atlanta-based beverage giant announced in March that it plans to test a PET/PEN blend for a single-serve bottle sometime somewhere this summer. Corporate communications officer Carol Martel tells PW that plan still holds.
"We're definitely interested in [PEN's] performance characteristics, and this test initiative will let us evaluate them in the commercial marketplace," says Martel. As tests go, it's sure to be closely watched.