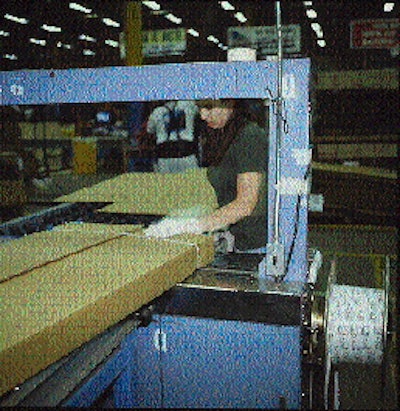
Occupying a mind-boggling 3.1-million-sq-ft in Romulus, MI, Ford Motor Co.'s Parts Redistribution Center is the very heart of the Ford Customer Service Div. Continuous improvement of processes and updating of equipment has been a cornerstone of the PRC since its completion in 1971, and the latest example is the recently completed Strapping Machine Project in the sheet metal packaging area. This is where door panels, fenders, tailgates and other metal parts are packaged for shipment to a network of distribution centers both domestic and foreign.
The three-year project involved a phased-in installation of 20 machines from Ovalstrapping (Fort Payne, AL) that has brought significant improvements in areas such as worker safety, energy consumption, package consistency, labor costs, maintenance, and reduced damage to parts shipped.
"Our biggest problem before these machines arrived was downtime," says materials handling engineer Juan Lucaire. "If one of our old strappers jammed, it was a long time before we could get it running again."
Safety was an issue, too. The previous machines used metal fingers to hold the polypropylene strapping in position between cycles. To clear a jam, the fingers had to be manually opened to remove the strapping in the track. This put the worker in close proximity to the heater bar.
The new machines have a single track system that leaves no strapping exposed. To clear a jam, the operator pushes two buttons and the strap is ejected or a loose end is drawn back into the machine for use in the next cycle. No fingers come in contact with the banding or the heater bar.
Four machine clusters
The new strapping machines are clustered in four groups of five each. Right down the middle of the machines-10 strappers on one side and 10 on the other-runs a continuously moving conveying system equipped with hooks on which parts to be packaged hang. Stacked beside each Ovalstrapping unit are the corrugated shipping containers used for packaging.
Each packaging cycle begins with placement of a scored corrugated blank on a flat table. As one of the two workers does this, the other walks to the parts conveyor, gets the necessary part and places it on the blank. When needed, inner corrugated components are inserted to immobilize the part. Workers fold the corrugated blank around the part, tuck in flaps (if the blank has them), and the container is pushed forward into the 90" x 24" yoke of the strapping machine. The corrugated container rests on wheels the whole time, which makes it easy to push it forward once the part is loaded in place.
To activate the strapping mechanism, the operator can either step on a foot pedal or press a button and the PP strap automatically wraps itself once around the package. An external tension control switch lets the operator regulate the tension to the correct level as determined by the material used and the part type. As soon as the band reaches that preset level of tension, heat-sealing and cutting are automatically activated.
According to Lucaire, the corrugated specifications vary considerably from one part to another. Virtually everything from 200#-test single-wall to 500#-test triple-wall is used. The band tension needed to effect a secure closure varies from one box to another. With its former equipment, Ford couldn't adjust the tension without a mechanic making an internal adjustment. To avoid this downtime, workers set the band tension at a midpoint for all packages. Thus, some banding was too loose and some too tight.
With its ability to regulate tension according to the part and box material encountered, the new machine eliminates at least one damaged part per week per distribution center served. This in turn results in significant savings by eliminating rework, repair, reordering and/or transportation. It's also making the PRC a hero at Ford parts distribution centers all over the world.
More benefits
Additional benefits now enjoyed by PRC since the strappers were installed include these:
*Energy. While the old strappers' motors ran constantly, the Ovalstrapping machines run only on demand. According to Lucaire's estimates, a typical part requires three bands taking 7.5 seconds of motor time. He estimates an energy savings of $1.38/machine/day because the new machine's motors run only on demand.
*Speed. Cycle time on the new machines is 0.5 seconds faster than on the machines that have been replaced.
*Waste. The new machines cause little or no wasted strapping material.
*Maintenance. All functions are controlled by a single belt-driven cam. An interior diagnostic panel shows if an area of the machine needs attention, eliminating time-consuming tear-down and inspection. Also, heater and cutter bars can be replaced without the use of tools and in less than one minute.
Ford declines to quantify the dollars saved since the new strappers were installed. But Lucaire figured on a two-year payback on the investment when he presented top management with his cost justification figures prior to the machines' installation.
He's quick to point out, however, that as important as cost savings was, it wasn't the only motivation behind the project.
"Each machine provides a high-quality, uniformly secured packaged part," he concludes. When the firm's motto is "Where quality is job one," what could be more appropriate?