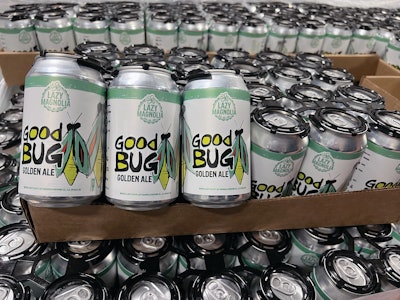
It’s not every day a brewery breaks onto a scene unoccupied since before prohibition. But that was the case for Lazy Magnolia Brewing Company in Kiln, Mississippi.
Opening in 2005 as a small family brewery, Lazy Magnolia was the first in Mississippi to enter the packaged beer space after the state repealed a slew of old regulations that had prevented this type of business.
Fast forward to late 2022, when the brand was sold to investors out of Utah. Lazy Magnolia’s name and character stayed the same, but its packaging horizons widened significantly.
The new owners have made significant investments in new equipment, “upgrading our packaging equipment, upgrading our fillers, upgrading our depal,” says Christopher Maros, general manager at Lazy Magnolia. “And we’ve picked up a lot of business due to getting to the fully automated stage.”
Both canning and bottling operations were treated to equipment investments, but the new can filling equipment has been the biggest game changer for the brewery. A twin set of rotary fillers now sends triple the product down the line every hour, with quality control leaps ahead of the legacy equipment.
Lazy Magnolia’s focus on cans keeps the brand in line with the growing popularity of cans as a packaging format. “Cans don’t take up as much real estate, they’re lighter to ship, and they’re easier to package in my mind,” Maros says.
All that extra canning capacity and convenience has driven Lazy Magnolia’s own portfolio growth, paving the way for plans to introduce eight new styles of beer in 2024.
Lazy Magnolia is far from the only brand benefitting from the new equipment, though. Contract packaging makes up most of the company’s operations.
About 80% of Lazy Magnolia’s packaging operations are done for Richard’s Rainwater, a water brand whose product runs perfectly well on craft brewery equipment. Another 5% of the business is for contract brewing and packaging of craft beers, leaving about 15% of packaging operations for the brewer’s own beer. The new equipment has allowed Lazy Magnolia to take on even more contract packing work, with two new contracts to package for other brewers set to begin by the end of March.
“The co-packing in world of craft brew is heating up. Everybody’s wanting to come up with some kind of new innovative product,” says Maros. “Being a primarily co-packing facility, [the investors] saw the opportunity in co-packing, that is most of the drive to put the capital into this facility.”
Front-of-Line Automation Boosts Productivity
Lazy Magnolia’s upgraded canning line begins with the unloading of Ardagh brightstock cans with a new full-height CIB automatic depalletizer from Ska Fabricating, which replaced an older Ska depalletizer. Maros says the new machine has no trouble keeping up with the recently increased speeds further down the line.
“It’s fully automated, that’s what I love about it,” Maros says. “You throw the pallet of cans in there, cut the straps, take the top frame off, and the depal does all the work itself. It’s pretty much hands-off, so I don’t need to have an operator there.”
A single-filer organizes the depalletized cans into a Ska S-Grip straight lowerator, and a GR-X ionic air blade rinses the empty cans as they drop down to the lower level. A Videojet inkjet coder also date-codes the bottom of each can during the lowerating process.
An operator interacts with the HMI on the GAI monoblock bottle filler and crowner.Lazy Magnolia
The seamers can be adjusted for a maximum of three seam sizes, and Lazy Magnolia standardizes around 200 mm, 202 mm, and 206 mm. This range of can end/lid diameters allows Lazy Magnolia to seam seven different can varieties; an 8-oz sleek, a 12-oz sleek, 12-oz standard, 16-oz standard, 19.2-oz standard, a 21-oz “Arizona-style” can, and an 8.4-oz “Red Bull-style” can, Maros explains.
Each seamer can be changed over within about 30 minutes to run whichever can size Lazy Magnolia needs on a given day, with functionality to pull product from a single tank into two different sizes at once, one on each line.
“With both of those fillers behind one depal, we’re able to feed both of them consistently at speeds of 4,000 per filler, or 8,000 an hour total,” Maros says. That’s 133 cans/min, compared to the roughly 40 cans/min Lazy Magnolia produced with its legacy filler.
These fillers have been not only faster, but “very high quality, they’re very well put together, very user-friendly,” Maros says.
Just before lids are placed on each can, an undercover gasser injects CO2 inside. The lidded cans are sent to the seamer within two to three seconds from there, limiting trapped oxygen in the cans to virtually zero. That translates to low dissolved oxygen the bear, meaning high quality and shelf life.
Once seamed, the cans are transported and combined via MCE conveyors into a single, foot-wide mass follow-style conveyor. The belt sends the cans through a Hermis TP-HRW 5 pasteurizer for a 42-minute dwell time.A single pasteurization tunnel with a 42-min dwell accommodates both cans and bottles at the same time.Lazy Magnolia
The pasteurizer ramps up to a temperature capable of killing any potential pathogens or spoilage organisms before cooling the cans back down to room temperature on exit. It can also be used simply as a warmer, Maros explains, “so the cans come out the other end dry. It’s very humid here in Mississippi, so we usually have to run it at a certain temperature just so the cans don’t sweat.”
The pasteurized cans are then single filed and sent through a series of in-house-fabricated air jets to further ensure removal of any moisture.
Once past the air jets, the cans can either be sent to a CVC Technologies Inc. labeler, or to an accumulation table if the cans are pre-printed.
Lazy Magnolia uses pressure-sensitive labels for its own cans, but also accommodates printed and sleeved cans for its contract packing customers. The brand aims to switch to printed cans for its own products once volumes are high enough though, “just because there’s gigantic money savings there,” Maros says.
Secondary packaging for cans is currently done by hand, with plans for automation soon. The brand’s current setup for beer products includes Pak Tech four-pack can carriers for 16 oz products, and six-pack carriers for 12 oz products. Trays are hand-folded, and multipacks placed in them by hand.
Further upgrades on the bottling line
Not to be outdone by the canning line, Lazy Magnolia’s bottling line received its own upgrades to help scale operations.
Lazy Magnolia can run 12-oz bottles of various shapes, as well as a 750-mL bottle usually reserved for specialty beers. The bottles are amber for in-house beers and most contract packing customers, and clear for Richard’s Rainwater. Bottles for the brewer’s own product are supplied by Colorado-based Owens-Brockway Glass.
The bottling line starts with another Ska depalletizer, this one a bit older with an infeed at the filler level instead of overhead. From there, the bottles are sent to a GAI 16-head rotary filler with a three-head capper/crowner, which runs up to 5,000 bottles/hour, or 83 bottles/min.
The GAI filler is new to Lazy Magnolia, but it’s not the first time it’s been on a packaging line, as Maros explains, “our old [filler] was just very neglected, so we actually found this used one from a brewery out of New York.”
After filling and capping, the bottles are sent through the same pasteurizer that services the two canning lines, allowing the brand to pasteurize bottles and cans at the same time. “We run everything through the pasteurizer and pick off the cans after the pasteurizer at the accumulation table,” Maros says.
Bottles run through the same CVC Technologies labeler as the cans, where they are also date coded before heading to secondary packaging.
Room for more automation in secondary packaging
Now that front-of-line operations have been automated to allow for new business, Lazy Magnolia’s eyes are on its secondary packaging optimization, keeping a similarly quick pace as with earlier upgrades.
That starts with automating case packing for bottles, with the brand currently waiting for upgrades to arrive.
Currently, an offline master case erector from Eagle starts the process by assembling 24-count master cases of bottles. Six-pack carton carriers need to be manually erected and placed into the master cases. The cases with cartons inside are then manually added to an APE drop packer, which picks and places 24 bottles at a time.Bottling operations will soon get an automation upgrade by way of a box shop that will erect 6-pack carton carriers and the 24-count master cases that hold four carton carriers each. This upcoming box shop installation will then feed the drop packing operations.Lazy Magnolia
That process will be taken out of workers’ hands soon though, explains Maros, “we’re waiting on one new piece that’s going to be able to erect the six-pack carrier, put the four six-pack carriers into the master case, and then drop the bottles into the six-packs [with the APE drop packer], and then tape the cases as well.”
The master cases are palletized by hand, but the brewer plans to purchase a palletizer in 2025.
The canning line has its own automation upgrades in the pipeline as well. “Toward the end of the year, we’re going to get a Pak Tech machine that automatically puts [can carriers] on. We’re either going to get that or a HiCone machine, the plastic ring applicators,” Maros says.
This year’s plans also include a “continuous motion packer that makes the tray and then places the six-packs or loose pack in the tray,” Maros says. The brewer is specifically installing a DMM Packaging T300 tray former packer, as well as a DMM CTC 40 can carton packer, in about a year.
The brand’s 12-oz and 16-oz standard cans require trays with a different footprint than its 8-oz and 12-oz sleek cans, so its focus is on flexible equipment to accommodate the different sizes.
A bit further down the road in 2025, Maros also aims to have shrink bundling capability for cans.
Even as Lazy Magnolia finds itself in the middle of an upgrade plan, Maros sees major benefits to operations from the brand’s current progress. “Going to full automation, where you take the human factor out of it, you can literally cut your labor costs in half, especially on the packaging side,” he says.
As front-of-line productivity boosts are coupled with plans for further end-of-line automation, Lazy Magnolia continues to cement its legacy as Mississippi’s pioneering packaged beer brand, poised for growth in its own portfolio alongside its contract packing partnerships. PW