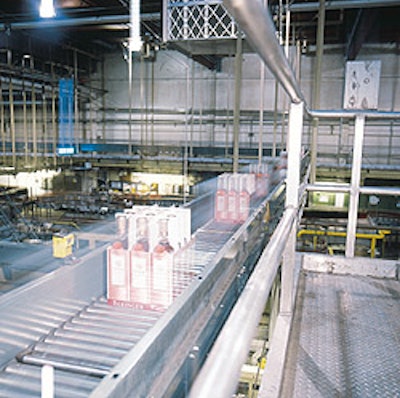
At the St. Helena, CA, facility of Beringer Blass Wine Estates winery, palletizing, conveying, and stretch wrapping equipment was causing costly breakage and product loss. So engineers at the Napa-based winery decided to replace the aging equipment.
As they explored their options, it wasn’t just gentle handling they were after. They also required speeds of up to 35 cases/min.
They found what they needed in a case accumulating system and palletizer from Alvey Systems (St. Louis, MO) and a stretch wrapper from Cousins Packaging (Tracy, CA).
“The old machines were really starting to show wear,” says John Clark, technical supervisor at Beringer. “We had a lot of breakage and damage to our product. Since we’ve updated the machines, damage has gone way down. That was probably our biggest reason behind buying new machinery. It was just to the point where it wasn’t worth putting more money into the old equipment, which was used when we bought it. We needed to buy new ones.”
Onto the pallet
“We’ve already begun saving money with the new palletizer,” Clark says. “We’ve saved just due to the fact that we are able to produce the capacity that we need to. Another thing that really helps the people here is that we can input Spanish language for the controls and trouble-shooting screens. If we were to have a problem, that would really help not only the operators, but also our mechanics.”
The new Alvey 881 was installed in October 2001. It replaced a unit that had been there for years, Clark says.
“We’re upgrading our facility constantly,” he continues. “It was time for a new palletizer. And we needed to improve our line in other areas since we are now capable of filling anywhere from 350 to 400 bottles/min. We needed a palletizer that could keep up with that output.”
Clark adds that while Beringer is capable of filling bottles at these rates, engineers try to keep the line running at around 325 bottles/min. Because filling machinery is also beginning to wear, Clark sees no reason to push the machinery at top speeds unless it is necessary. Following the expansion of current packaging facilities, Beringer is planning on replacing other pieces of machinery, including filling, to keep up with demand.
Feeding full cases to the palletizer is a new accumulating conveyor, also from Alvey. Clark says the Accuglide Plus was an ideal addition to Beringer’s facility because of its zero-pressure accumulation feature. The previous conveyor would back up continuously, forcing unnecessary pressure on the cases, ultimately causing product damage. The new 100’ of conveyor detects when cases are backed up and stops driving the affected portion of the conveyor. Broken into zones, the conveyor runs on a padded chain driven by air pucks. When the conveyor is running normally, the air pucks are inflated to have full contact with the pads that drive rubber rollers. Every zone has what Clark calls a sensor roller. The sensor roller detects the backup or slowdown of cases, causing the air pucks to stop or start driving portions of the affected conveyor.
“The conveyor has already paid for itself,” Clark says. “That’s absolutely not a problem. We should see a payback on all of our new machinery within the next two years.”
The conveyor moves cases to the overhead palletizer. A metering belt meters the cases into the palletizer. Depending on the box pattern, a turning arm will “kick” the cases to arrange them into the appropriate position on the forming table. Once the bottom tier is formed, it’s pushed onto a pallet that’s been discharged into the machine by a pallet dispenser. This first layer drops down by means of a pneumatic lift, to make room for the next layer. This process continues three more times until the pallet is complete. The four-tiered, 56-case load is discharged onto a set of rollers that feed it into the Cousins wrapper.
For Beringer’s club store “tray packs,” the palletizer also dispenses a corrugated top sheet when the pallet is completed. Because the pallets are often stacked three high, a barrier between loads is crucial to prevent scuffing or damage to the cases. Located above the pallet discharge, vacuum cups pick up the corrugated board from a magazine and apply it to a newly finished pallet.
All wrapped up
From the palletizer, pallet loads are conveyed to the Cousins 6100 Series automatic stretch wrapper. Also installed last October, the wrapper was chosen by Beringer for its small footprint, among other reasons.
“The old wrapper had been there for quite a few years,” Clark recalls. “It was getting to the point where it was time to replace it. So we did a lot of research. Because of our limited space, we went with the turntable model, which is the same as our previous wrapper, but there were some things we especially liked about the Cousins machine. The previous wrapper we had was belt-driven, and we had some problems with the belts breaking.
“This one is gear-driven,” he continues. “One of our other facilities bought a machine similar to it. They had good luck with the drive train, so that’s why we went with the gear drive. It’s really fit in well at Beringer.”
Once the pallet has reached the wrapping table, the stretch film is attached to the pallet via grippers. The table begins to turn slowly.
“One of the really nice things about the wrapper is that it will capture the load by turning slowly at first while the wrap moves from the bottom of the pallet to the top,” Clark explains.
The table then begins to turn faster, allowing the film carriage to wrap three times at the top before descending to the bottom where it again wraps three times around the load. Grippers close around the end of the film, a hot wire cuts the wrap, and the grippers return to their “home” position, ready to take the end of the film for another load.
Beringer’s new machinery is networked to work seamlessly via a PLC. Though the machines can run on a network, Beringer engineers have hardwired the two together for now.