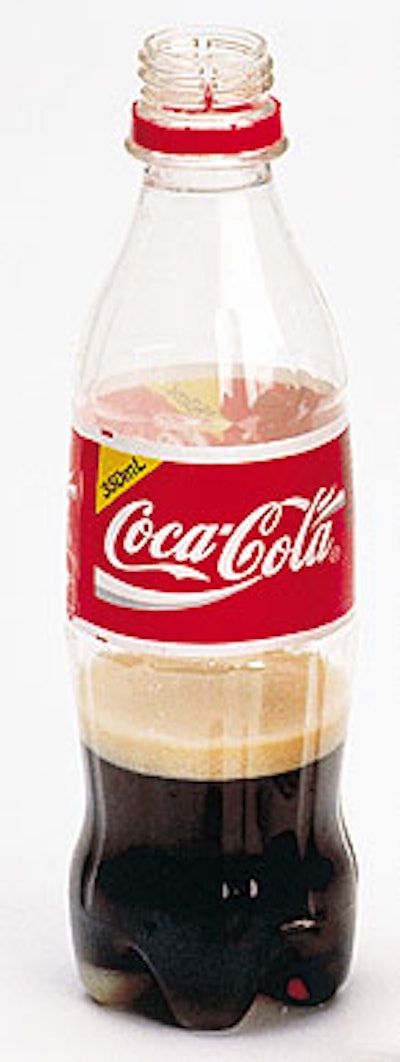
The Coca-Cola Co. rarely publicly endorses another company’s technology. But the Atlanta-based firm is endorsing the use of new mold-making technology for its global network of packaging suppliers. In October, it permitted Metallamics (Traverse City, MI) to issue a press release saying that Coke believes the process will significantly reduce the cost and improve the quality of preforms and plastic bottles used in its packaging. What makes this even more eye-opening is that Coke doesn’t have access to the technology on an exclusive basis.
Metallamics calls the technology SM?X™, which stands for shape-making heat exchangers. The company has won worldwide patents on its mold-making concept that transfers heat from the molded part back into the mold more rapidly and more uniformly than conventional molding tools.
Coke even allowed its principal engineer for package development and design, Chris Kjorlaug, to discuss the company’s findings. “We’ve taken our time thoroughly evaluating this,” Kjorlaug says. “And we’ll continue to look at it, in terms of new applications and improvements. There are definite benefits to the technology, both from the standpoint of processing, as well as part quality.”
Kjorlaug says the company did extensive lab testing before it initiated a commercial beta test, particularly for injection molding. Although he says he personally hasn’t had deep experience using the technology for blow molding, he says the company has done testing. Rob Baskin, a Coke spokesman, confirms that the beta-site testing was underway for more than a year before the announcement.
“Here, frankly, we are endorsing this process. In the last 18 months or so, we’ve relaxed our policy and allowed suppliers to make public this type of news,” Baskin says. “We think this will be good for our system.”
Better molds
Dr. Robert McDonald, president of Metallamics and a former Dow Chemical researcher, says that it’s taken his company about five years to establish the whole infrastructure to produce molds. It now has authorized toolmakers both in North America and Europe, and it also has partnerships with a variety of materials suppliers and machinery companies. “Our patent is about how to make a better heat exchanger and then form that into a mold,” he says.
Although McDonald says these molds can reduce cycle times by 10% to 50%, Coke’s Kjorlaug is reluctant to be specific. “The optimal improvement will depend on the part itself, from the standpoints of size, weight, and wall thickness. So it’s hard for me to say that a molder can go from this to that [cycle time]. I’m not in a position to say the improvement would be X-percent.” Even at 5% to 10%, McDonald says, if billions of performs are involved, it adds up very quickly.
Coke’s engineer has no reluctance to identify ElectroForm Industries (Vandalia, OH) and R&D Tool and Engineering (Lee’s Summit, MO) as the suppliers for the laboratory and beta tooling, respectively. Kjorlaug also reports that the commercial injection-molding tests were done on a molder by Husky (Bolton, Ontario, Canada). Some industry observers believe that Metallamics uses high-tech versions of ceramics in its molds. Kjorlaug says these molds achieve “turbulent laminar flow,” two often opposing characteristics.
Almost no trade-offs
Coke’s Kjorlaug confirms there are few sacrifices with the new mold technology. He admits that the first sets of molds probably cost about 5% more than conventional tooling, but he explains, ultimately the company expects the new molds to be priced at parity with conventional molds. “For now, it’s new, and toolmakers have to learn how to produce them, while they’re still making regular tools,” he says.
In much the same way, the first sets of tools probably took longer to make, but that, too, should disappear in the future. “We expect that, once the toolmakers have some experience, the delivery time will be the same as now,” Kjorlaug says.
He also doesn’t see any reason why the molds would perform differently from one molding machine to another. “I don’t think one type of molding machine would have any advantage over another, just because of the tooling design.”
Although the company is recommending the tooling for its global network of packaging suppliers for carbonated soft drinks, Kjorlaug believes the technology may have even more benefit for heavier bottles, such as those destined for hot-fill applications or bottles that will be returned and refilled.
“As the bottle goes up in weight and size, even in different preform designs, I think the injection molder will see greater benefits,” he says. “I would think that, for heat-set or refillable bottles, this technology will definitely be applicable. The benefits could even be greater for heavier bottles, rather than for carbonated soft drink containers.”
When asked about quality improvements, the Coke engineer pointed to improved uniformity, in terms of both stress distribution and heat distribution. “That uniformity will obviously improve downstream operations,” he adds.
Kjorlaug won’t predict how soon the technology will be used in the Coke network of bottlers. “Our role is to present to the bottlers new technology and offer our experience,” he says. “We’re just passing along information now; they’ll make their own assessments on whether to apply it to their operations.”
From the outside, Metallamics’ McDonald says the molds don’t look any different from conventional tooling. “Like Intel, it’s what’s inside,” he says mysteriously. “What we’ve done inside the mold changes the very nature of mold behavior.”