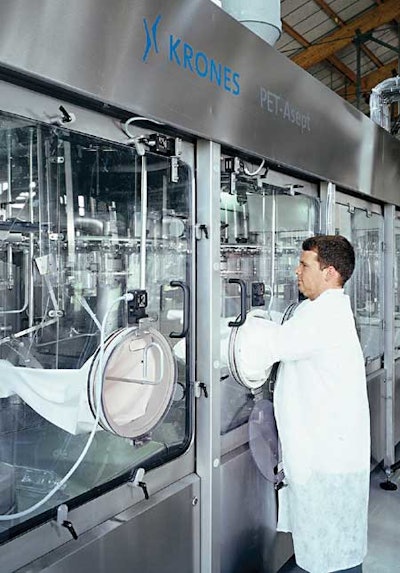
For Sursee, Switzerland-based Pomdor AG, the juiciest development in the past year was the addition of a turnkey aseptic bloc filling system from Krones. Called PET-Asept, the system is used for beverage syrup, carbonated juices, and noncarbonated fruit juices and teas sold in Switzerland.
PET-Asept was up and running last July, only seven months after it was ordered. The system fills PET bottles ranging from 33 cL to 2 L in size, with 28- and 38-mm neck finishes. Injection/stretch blow-molded bottles are supplied by Resilux Schweiz. Closures come from Alpla and Bericap. Shelf life is a minimum of six months for still juices, one year for carbonated beverages.
The aseptic bloc system includes a sterilizer, rinser, filler, and capper. PET-Asept also includes Krones’ Checkmat system that inspects for over- and underfills and detects skewed caps; liquid nitrogen dosing; an ultra-high-temperature sterile water generator; ventilation and exhaust system; pure steam generator; storage, dosing, automatic foam-cleaning unit; a reverse-osmosis water treatment system for bottle sterilization; and a cap feeding system. Krones’ system works in concert with the company’s existing flash pasteurizer and clean-in-place systems.
‘Ambitious’ upgrade
“In December 2002, we decided to replace our existing aseptic bottling line with the PET-Asept process from Krones,” says Dr. Norbert Bühler, plant manager at Pomdor, which is owned by Fenaco, a Swiss agricultural cooperative. “We evaluated the market for [aseptic] machinery, and [we had little] time [before we had to go online] with the new equipment. We felt Krones would best be able to provide us machinery that would fulfill our needs.”
Upgrading to the Krones equipment represented “a very ambitious project,” he recalls. “The first production run was scheduled for last July 25, and the deadline was met. We were confident we’d make it,” he continues, though acknowledging there were challenges. “We wanted to fill carbonated beverages in a semi-aseptic mode, plus still products in aseptic mode. And we have different neck diameters, plus we fill beverage syrup into a one-liter bottle. For syrups we use press-on closures that are sterilized by ultraviolet radiation.”
The new line replaced a previous aseptic line that’s now used at the company’s Elm, Switzerland, facility. That system “worked well for carbonated beverages, but we weren’t satisfied with the results for fruit juices and teas,” says Bühler.
“The problem was that those products were not always 100-percent commercially sterile,” he recalls. “We sometimes would have yeast, mold, or lactic acid bacteria. The machinery was installed in 1996, when aseptic filling technology wasn’t as advanced as it is today.”
Isolator
The new line runs five days a week, with annual production this year projected at 30 million bottles. Bühler says the line produces 33- and 50-cL bottles at 300/min speeds, 1-L bottles at 233/min, 1.5-L sizes at 167/min, and 2-L versions at 100/min.
Bottles are carried through the system by their necks via grippers and starwheels within the Krones’ “Isolator,” which provides hermetic isolation from the external environment. Within this Isolator are the sterilizer, rinser, filler, capper, and bottle-handling components. Operators can make adjustments at key machine areas by using glove ports affixed inside the Isolator wall.
Mechanical, electrical and electronic, and pneumatic portions are outside of the aseptic zone so that they can be maintained without breaking asepsis. Two-stage filters and overpressure in the aseptic area prevent germ penetration as bottles enter the Isolator through airlocks, and when they are discharged out of the Isolator.
Pomdor can run the line for 72 hours before conducting a major cleaning with caustic spraying, external caustic foam spraying, and peracetic acid spray. Every four hours a less-extensive chemical cleaning is done.
System process
Once bottles enter the aseptic zone, they are conveyed to the sterilizer. A peracetic acid solution cleans the bottle exterior while a combination of steam and peracetic acid is injected to clean the bottle interior. Bottles are not inverted during this process. The sterilizer is designed to minimize water and chemical usage, which cuts costs for Pomdor.
Next, bottles are rinsed with what Krones refers to as a “jetting” system that injects bottles with a combination of sterile air and water. Like the sterilizer, the rinser is designed for low water consumption.
Bottles are conveyed by their neck rings from the rinser to a 60-head volumetric flow-meter filler. Carbonated beverages are bottled with a counter-pressure process; noncontact filling is done for still products. Change parts allow Pomdor to switch from one filling process to the other. To reduce the amount of oxygen in the headspace of apple and orange juice, and some teas, Pomdor injects liquid nitrogen prior to closure application.
Closures go through an immersion bath for disinfection treatment followed by sterile rinsing and sterile air treatment. Caps are submerged open-side-up in a peracetic acid bath. They are moved through a spiral conveyor before they’re flushed with sterile water, blown dry with sterile air, and fed to the capper’s pick-and-place station for application to the bottle. Change parts are required to accommodate the 28- or 38-mm neck finishes.
Custom closing
According to Krones, Pomdor is the first company worldwide to install a new type of screw capper. Krones patented the capper’s aseptic design, relocating the cam support and closing elements for optimal microbiological safety. Specifically, Krones reduced the number of components above the bottle to minimize the risk of contamination from any liquids or moisture on the machine that could drip down to the filling area.
In most cappers, sealing heads and drive units are located above the bottles, particularly for open bottles waiting to be capped and during closure transport. That can increase the possibility of germ formation and product contamination, says Pomdor.
“Krones’ chief designer came up with a stroke of genius there,” says Bühler. “I think the design eliminates all the risks.”
After filling, an existing Krones labeler glue-applies a label to the bottle prior to downstream packaging and distribution steps.
Benefits
Asked to quantify the advantages of the new aseptic filling system, Bühler says the primary improvement is that “we’ve achieved 100-percent commercial sterility, and we’ve had no problems with the bacteriological sterility of our products.”
Speed was not a concern, he says, though he does note, “we’ve been pleasantly surprised how well it’s worked. We can run the line as much as one-third faster than was actually guaranteed.”
Bühler points out that there are labor savings “since the machinery hasn’t required troubleshooting and results in secure products.”
There are also environmental benefits with the new system. First, the process reduces water consumption. Bühler explains, “We use ultra-high-temperature water for the reverse-osmosis process. For juices and some teas, we also use sterile liquid nitrogen. A single drop of the sterile liquid nitrogen is put into the bottles before closing.” The process causes nitrogen to expand and drive out ambient air in the headspace.
PET-Asept is designed to require only a small amount of cleanroom space, thanks mainly to the Isolator concept. “The Isolator itself was highly persuasive,” says Bühler of the company’s decision to add the bloc unit that requires a relatively small footprint.
The bottle system also fits into the PET recycling process in Switzerland where consumers return bottles to retailers. Bottles are collected from retail outlets and delivered to recyling facilities where they’re shredded into flakes, treated with soda lye, and washed. Clean PET flakes are shipped to PET preform producers.
The turnkey system has made an impression on Bühler. “There are lines that are suitable for bottling still fruit juices in cold aseptic mode with sufficient safety. But what those lines can’t do is also bottle carbonated beverages. A line like this, which can do both, is to my knowledge something you can only get from Krones at the moment.” —JB