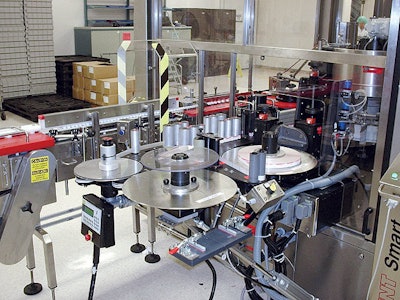
Wherever a patient’s blood or urine sample is being tested, diagnostic controls play a key role. They’re sent through the same analyzing system that the patient sample goes through to help verify the quality and accuracy of the analysis.
At Bio-Rad Laboratories in Irvine, CA, diagnostic controls are filled into glass vials and then stoppered, capped, labeled, and tray packed. In August, a new cap, label, and tray-loading line went into production capable of 550 vials/min.
“Demand for our product was rising,” says Lindy Vejar, project leader at Bio-Rad. “At the same time, our existing equipment was starting to show its age. It was time for a new line.”
At this time, Bio-Rad is preparing for the installation of a new filling/stoppering machine (see sidebar) scheduled for a May 2004 startup. For now, Bio-Rad continues to operate the two filling machines it has had for some time, feeding their combined output through the new cap/label/tray-load equipment.
Vials come in two sizes: 5 mL and 10 mL. But fill volumes can be adjusted in just about any increment that a Bio-Rad customer wants. Made in France, the vials are from Saint-Gobain.
Once filled and stoppered, the glass vials are either freeze-dried prior to secondary packaging or sent directly to secondary packaging with the vial contents still in a liquid state. Either way, the vials encounter a Bi-Flo® accumulation table from Garvey Corp. It receives vials in one of two ways. If the vials have gone through freeze drying, the operators bring trays of vials on carts to the Garvey Bi-Flo infeed system. An operator gently pushes the vials out of the trays and onto the Bi-Flo system. When vials don’t go through freeze drying, they’re conveyed from the filler directly onto the Bi-Flo table.
Heading for the capper
In either case, the vials are merely passing through the Bi-Flo table, headed for a Model CAS-16/480 Fowler/Zalkin capper from Fowler Products. It applies a 20-mm threaded closure that’s injection-molded of polypropylene.
The Fowler/Zalkin capper is a rotary system with 16 capping stations. A feedscrew feeds bottles on-pitch to an infeed star that delivers them to the 16 pockets of the main turret. The vials rest on a rotating table as they move through the capping process.
Ahead of the cap placement station, a photocell checks to see if each vial has a stopper in place. If not, a signal sent to the PLC prevents a cap from being placed on that vial. Later, another photocell inspection station checks for cap presence or cocked cap. Faulty vials are automatically rejected.
How vials are rejected is a bit different than what’s found in most conventional systems, where the PLC notes the position of a faulty vial and then signals a downstream pneumatic device to kick that vial off the conveyor line when it comes by.
“With that kind of technology, if the line experiences a sudden surge, or if it slows down, or if you need to jog the line for some reason, it’s conceivable that the downstream pneumatic device might kick off the wrong vial,” says John Augsburger, Bio-Rad lead engineer. “Remember, at that point, the vials are not positively controlled. They’re loosely aligned on a conveyor. With the system provided by Fowler, if a vial is faulty, it’s sent down the reject path as it is released from the discharge starwheel. The vial remains in positive control until after the discharge station.”
Next is a 21-station Autocol labeler from Krones that applies a pressure-sensitive paper or biaxially oriented PP label. Labels are preprinted with product identification and expiration date. Augsburger says the labeler’s redundant-head feature is a welcome one
“As soon as one roll is empty, the second one kicks in,” says Augsburger. “That means no downtime, not even a single missed vial, at speeds of 550/minute.”
Overlabeling
The redundant-head feature brings another big benefit, says Augsburger. Part of each lot must be segregated and given a second label right over the primary label. This second label is clear and has imprinted on it the words “value assignment” in large type. Customers use the value assignment vials differently than the rest of the lot, and until the redundant-head labeler was installed, this second label had to be applied by hand. “Now all we do is load those labels on the redundant labeling head and turn both heads on at once,” says Augsberger.
Before vials exit the labeler, they pass through a laser coder from Lasertechnics. According to Vejar, quality control protocol sometimes requires that a “sub batch” of vials be coded around the thread area. But the need for this code is infrequent, which makes laser coding technology a good fit, says Vejar. “It’s clean and it doesn’t clog, so it’s always ready to go even though it’s only needed occasionally,” says Vejar.
Exiting the labeler, vials enter a custom-built, semi-automatic tray loader supplied by Garvey.
“Pick-and-place tray loading was certainly an option, but it’s relatively expensive,” says Vejar. “The system Garvey came up with is simple, cost-effective, and works well. They just seem to have a knack for this sort of thing.”
Basically it’s a matter of massing vials on a 24”-wide mat-top conveyor whose left and right rails are shaped in a way that encourages the vials to nest snugly together without any voids. The right side also strokes forward and back gently, a motion that further induces the vials to nest tightly together. When enough vials have been accumulated, an operator pushes a button that stops everything. He then pushes a parting knife through the massed vials to form the wall of that tray load. Then all he has to do is pull a handle to rake the accumulated vials toward him and into a waiting plastic tray. As soon as the full tray has been taken away, the operator pulls the parting knife back and the machine starts up again so the cycle can be repeated.
“It’s a unique concept,” says Augsberger.
The same could be said about the entire line.