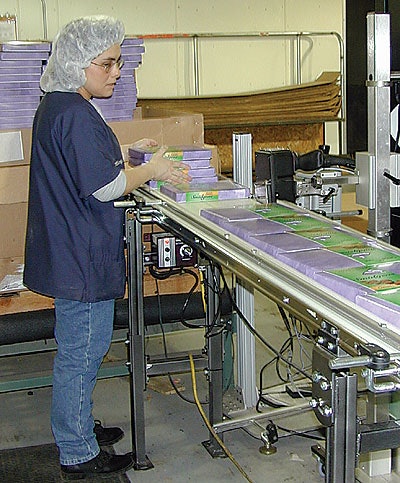
When you’re making and packaging quality chocolates, packaging lines can’t be frequently down for conveyor maintenance. Yet Dunmore, PA-based Gertrude Hawk Chocolates’ maintenance crew was spending lots of time maintaining and replacing conveyor belts.
So three years ago the plant decided to try one 6100 Series Sanitary conveyor from Dorner Manufacturing (Hartland, WI). The experience was so good that the plant purchased 13 more. Six of the new conveyors replaced the high-maintenance ones, and eight were purchased to accommodate the company’s growing production demands.
“We’re definitely getting longer belt life with these new conveyors,” states Matt Zaluski, plant maintenance manager. “Plus, we’re saving a minimum of 10 hours per week on belt maintenance.” In the past, cloth belts on the replaced conveyors wouldn’t stay on track and the edges would fray from abrading on the conveyor sides. Zaluski’s crew would have to remove the belts, trim the frayed edges, and put the belts back on again. After a few cycles of trimming, the plant would have to completely replace the belt, adding downtime.
“The new conveyors incorporate a V-belt system at a good price, and that virtually eliminates any tracking problems,” Zaluski reports. A V-groove in the center of the conveyor frame keeps the belt firmly in place. That means the belts don’t fray and rarely require replacing. The plant has not had to change a belt on the conveyors because of fraying of the edges, Zaluski tells Packaging World. “In the food industry, that’s a tremendous improvement,” he says.
The plant uses the new conveyors in many different operations from handling raw, unpackaged candy, to the packaging lines where candy is packed into boxes, coded, and overwrapped with shrink film.
The 6100 Series conveyors also feature a belt scraper that removes any residue on the belt. “In a chocolate factory, the product is sticky and tenacious by nature,” Zaluski states. “With the scrapers, any product residue is removed as soon as the belt goes around one of the end rollers. Anything that keeps the product off the belt is a big help to us.”
In addition, many of the conveyors at Hawk are engineered to withstand frequent washdowns, employing sealed bearings and watertight gear motors and controls. Plus the retractable ends permit easy release of belt tension so workers can get below the belts to clean the debris pans.
Finally, Zaluski says the compact design allowed these conveyors to be compatible with the plant’s packaging equipment and line footprint. “These conveyors are a great improvement for our plant,” he says. —AO