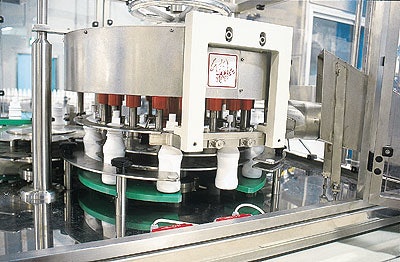
Coextrusion blow molding of IGI’s three-layer bottle is done in a separate room near the filling line on a Techne (Bologna, Italy) eight-cavity shuttle system that has an eight-second cycle time. It blows the bottles with air that has been steam-sterilized, says Techne’s Moreno Minghetti. It also leaves the dome on bottles after blow molding and then, immediately after cooling, seals the dome closed through an electric heating system. Minghetti calls it “aseptic blow molding.”
Bottles are pneumatically transported to an eight-compartment silo that is temperature-controlled to prevent the sterile air inside the sealed bottles from expanding or contracting, either of which could deform the bottles. Only one size goes to any one compartment, and the programmable logic controller that governs the system keeps track of which bottle sizes are in which silo cells. This important information is made available to the downstream filler so that it can draw bottles from whichever silo compartment it wants.
Bottles drawn from the silo are unscrambled and oriented by a Posimat (Miami, FL) unscrambler that discharges them into a neck trimmer from Maer (Massanes, Gerona, Spain) for dome removal (shown here). Now the bottles are ready for the aseptic filling system.
See the story that goes with this sidebar: Transforming the Egyptian dairy market