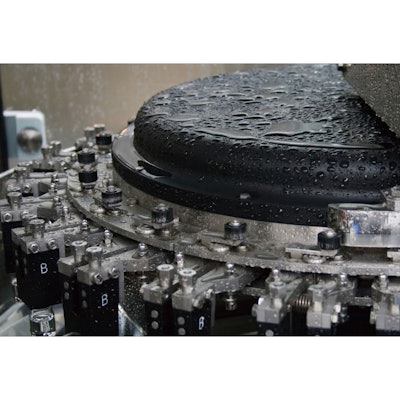
Griping about increased enforcement, aggressive inspections, and more frequent Warning Letters from the U.S. Food and Drug Administration is easy, but taking a proactive approach to the present regulatory environment is a much sounder tack for Philips Healthcare.
The Andover, MA, company’s Web site says that Philips’ “focus [is]on the fundamental health problems with which people are confronted, such as congestive heart failure, lung and breast cancers and coronary artery disease.”
“The FDA is in a difficult position,” says LeeAnn Rogus, vice president, quality and regulatory compliance, Philips Healthcare. “The general public and the House and Senate want tougher rules, while the industry doesn’t want its hands tied down by regulation.”
Rogus presented “Lessons Learned: How Product Failures, Recalls and GMP/QSR Problems Trigger FDA Enforcement Actions,” during a Sept. 22 conference session entitled, “Surviving a New Era of FDA Enforcement,” at Medical Design & Manufacturing Chicago.
Rogus made it clear that the more muscular FDA is striving for speed as part of an effort to safeguard the public from potential harm. “Facilities have been hit with very aggressive FDA inspections in the U.S., Europe, and China. They expect more corrections and removals, more recalls, and are making the process much more visible. If the agency finds a problem, they want you to issue press releases in a day.”
She believes the FDA is initially focusing its regulatory aim at larger companies where the agency can “get its biggest bang for the buck with so much exposure related to public health.”
During a candid, informative presentation, Rogus provided the following insights:
• The 15 days FDA gives a company to respond to a Form 483 inspectional observation has always existed, but the agency would usually let you have extra time. Not any more.
• Philips responds to every 483 with information related to the matter’s root cause and corrective action, and even provides the FDA with monthly written updates that continue until the issue is settled. “Sometimes I’ll drive an update and hand-deliver it to a compliance officer at the district level,” said Rogus. “It’s good to have a relationship with a compliance officer so [he or she] can see the whites of your eyes, and to see that you understand, that you’re taking their input and saying [acknowledging] there is something you could have done better. That way there is not an adversarial relationship.”
Again, speed is of the essence with Warning Letters. She said, “FDA wants problems corrected in six months, which isn’t much time when your company has large systems in place. We have used outside services to help us,” Rogus added.
• The FDA would prefer that manufacturers resolve issues.
• Drilling down to find the root of a problem can be complex, particularly when multiple vendors supply parts for your company’s product. In one instance, a problem related to a switch provided by an outside supplier took three months to pinpoint.
• Developing a top management strategy to deal with tighter enforcement is imperative. Management must understand the consequences of a problem and respond immediately, even if that means taking the painful step of contacting customers by sending them a warning letter about your product before you’ve actually identified the root of the problem and determined how to solve it.
• Besides seeking faster action, the FDA wants greater media scrutiny for companies. You need to have an emergency response communications team, and you may need to involve other functions, including legal, public relations, sales and marketing, service, and quality teams.
Rogus said, “Every company wants to produce great, safe products that customers will love. But the FDA doesn’t always see that. They see your Medical Device Reporting, the corrections and removals reported to them, and how many of those are still open. And, the FDA is not good at closing recalls. We try to sit down with district officers from the agency to get some recalls closed.”
Living with a more aggressive FDA that demands swift action is challenging, but Rogus advised companies to be conservative: “When In doubt, fill it [a document] out and report malfunctions. If you don’t meet requirements, you’ll get a Warning Letter. And don’t wait to learn the ultimate root cause before taking action. Make timely decisions about corrections and removals associated with these actions. Leave a voicemail message for the FDA district person about the status of closeout. Review the situation with the FDA.
“Remember, with the new aggressive FDA, your district office is the middleman. They work with you and understand you’re doing your best, but they’re getting pressure from FDA’s center regarding enforcement.”
• To minimize the chance of enforcement action, she summarized, “assess your priorities. Use metrics and learn where you have the highest risk exposure. Put an improvement plan together. Get executive support. Determine what’s needed to sustain long-term success. Don’t cover the problem with bandages.”
• Don’t fret over who the investigator is—assume they’re really good.
• Recognize there is a possibility that your facility’s quality system may be in need of an extreme makeover.