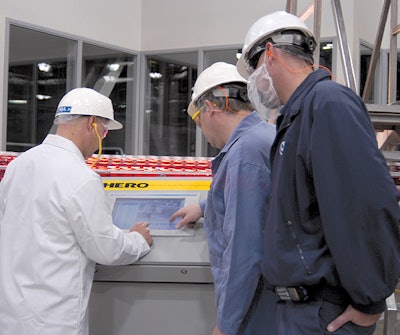
To solve a production problem, you first have to identify what it is. Watching a problem occur is likely the best way to know how to troubleshoot. Ocean Spray Cranberries uses a multicamera digital video system at its Henderson, NV, plant, to do just that.
The Hartness Error Recording Online (HERO) system from Hartness Intl. permits small cameras to be mounted on and in packaging machinery to provide automated monitoring. The PC-based system consists of four compact, 30 frames/sec digital cameras and a human-machine interface with touchscreen panel. The HERO captures and stores a video record of events that can later be reviewed.
“It puts a picture on the problem,” sums Michael Wright, Ocean Spray controls and automation engineer. “We gather the information and then view it frame-by-frame to home in on the true issue with a machine. It’s a tremendous time saver.”
Installed in late October and after only six weeks of use, the system has already seen the otherwise unseen, giving Ocean Spray personnel a clear, video-enhanced view into problems.
“The initial feedback is that it will be an excellent tool,” says plant manager Paul Altimier.
“The system is user-friendly, easy to set up, and is portable and mobile,” says Wright. Ocean Spray can move it to trouble spots throughout the plant’s two packaging lines, one for single-serve containers, the other for multiserve (larger) containers.
Seeing the unseen
“Once we realize we have a problem with a machine such as a multiserve case packer, we are able to set up the HERO system to help us define the root cause,” says Wright.
That case packer was the company’s first test of the system.
“We were having a problem with bottles jamming in the grid, but could not identify the exact problem because it was an infrequent occurrence,” explains plant engineer Mark Tysdal. “Very soon after installing the HERO, we discovered that once every hour or so, one downed bottle caused the grid to jam. We were able to see that the problem was caused by a rail out of adjustment at the laner that had previously gone unnoticed.”
Next, Ocean Spray used the HERO system on the single-serve bottle labeler that had experienced recent problems that were confounding personnel. It was an example of how the HERO system “allows us to quickly study why a machine’s performance has changed when no known variables have changed,” says Altimier. With the help of the HERO system, it was determined—with input from the vendor’s labeler technician—that the problem was likely related to the label materials.
“Our original intent was to identify root causes of issues, but now we see it as a tool to help keep vendors on their toes,” says Wright. “We also see it as a tool to identify when an operator may need additional training for certain pieces of equipment.”
It might also help them fine-tune equipment. “While the system is relatively new to us, in the short time we’ve had it, we like the functionality it offers,” says Wright. “I can also see it being used to fine-tune equipment.”
Mobile movie-making
The system consists of a portable NEMA4X cabinet with HMI touchscreen panel, Microsoft Windows 2000-based specially configured Pentium-4 processor with a 80 Gigabyte hard drive and 512 Megabytes RAM for the cameras, and four NEMA4X cameras that can be used in washdown environments. The system has LAN and Ethernet connections; Ocean Spray hopes to go wireless with the cameras.
The total time for relocating the HERO system from one machine to another by one technician takes about two hours, according to Wright. The process includes establishing connection to the packaging machine’s PLC. The continuous video stream is buffered such that a preset amount of video before and after a fault occurs is stored for review; the fault signal is from the machine PLC such as for a downed bottle.
The system could be used on essentially every piece of equipment on Ocean Spray’s two lines, according to Wright. From fillers to tray packers to palletizers, that totals 20 machines.
Altimier hopes that this new “operator tool” will help to improve throughput. “This is an on-the-line tool that provides real-time troubleshooting capability,” says Altimier. “We should be able to increase throughput and uptime in a very efficient manner.”