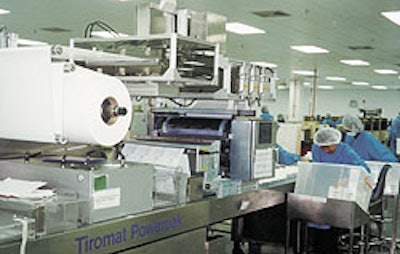
Cutting costs makes financial sense virtually anywhere in the world, including Rayong, Thailand. That’s where Allegiance Healthcare, a wholly owned Cardinal Health company, opened a plant last year to produce sterile, disposable surgical gloves. The plant employs six thermoform/seal machines, all equipped with a special drive system that allows the use of plastic lidding film rather than the paper that had been used for the glove packs when they were produced at another facility.
The paper-to-plastic switch saves Waukegan, IL-based Allegiance hundreds of thousands of dollars annually and helps avoid cost increases to customers as energy and other costs go up. Before the switch could be made, one key concern had to be addressed, says Nick Fotis, director of the company’s packaging technical center in Round Lake, IL. “The thin-gauge plastic lidding has the potential for [excess] stretching immediately after it’s heat-sealed to the bottom web, which can disrupt the seal,” Fotis says.
So Fotis and his colleagues looked to machinery suppliers for a solution. They discovered the Powerpak thermoform/seal machine from Tiromat Medical Packaging (Avon, MA), a subsidiary of Convenience Food Systems. Its patented Infrsync process compensates for film extensibility.
Allegiance placed six of the Tiromat machines into the Rayong plant. According to Fotis, the all-plastic packs would have presented several problems for the machinery used in other Allegiance plants. After the lidding film had been sealed to the forming web, both webs would have been advanced by a chain that grips the bottom web only. Because the seal would still be fresh, this process would potentially have caused a break in seal integrity because the bottom web would have been pulled along at a different rate than the lidstock.
“It would be like a rubber band. It would just pull,” Fotis says.
Multiple rubber rollers
Tiromat’s Infrsync attachment uses multiple rubber rollers to advance the lidstock at the same rate that the side grippers are advancing the bottom web. The lidstock is actually pushed instead of pulled, which takes all the pressure off the newly created heat seal. The end result, Fotis says, is better seal integrity, registration and film strength.
Just before the webs are heat-sealed, the rollers push the film along against a backing roller. As the sealing platen descends from above the lidding web, the rollers that advance the film separate from the backing roller, holding the film taut.
“It’s almost like you’re making your bed. Just before you smooth it out, you tug it a little to get the wrinkles out,” Fotis explains.
Both forming and nonforming webs, supplied by Rexam Healthcare (Mundelein, IL), are 4-mil high-density polyethylene. The forming web is clear and the nonforming web is white.
The prefolded surgical gloves are delivered manually to the machine in totes. The machine advances the forming web into a preheat area and then over the forming cavities that form the 4”x4” packs, each ½” deep.
Fotis wouldn’t say how many cavities are formed per cycle. But he does indicate that the machine operates at 20 cycles/min and that thermoformed cavities are filled manually by three operators. Each pack contains one pair of gloves.
As the top web unwinds, special tools die cut a tab that makes the package easy to open in the hospital setting. Also, flexo-printing equipment from Greydon (York, PA) prints company name, glove size, quantity and other descriptive information on the white lidstock. Lot number and date code are printed as well, but this information is done by a dot-matrix printer that also came from Greydon.
Continuing past the printers, the film reaches the Infrsync drive, meeting up with the formed and filled cavities just before arriving at the sealing station. Pneumatic cylinders push the sealing die down to create the seal.
The cylinders then retract and the packages are moved to a cutting station where cross-cut knives cut between the rows. Shear knives cut out individual packages. Operators at the end of the line inspect each unit, making sure the seal is good. The finished packages are hand-packed, 40/pack, into folding cartons and then into corrugated boxes for gamma sterilization.
Solutions
Another advantage gained with this approach to packaging is that the latex gloves are less susceptible to damage caused by ozone. Ozone is created within the glove pack during sterilization when the gamma rays turn ambient air to ozone. The ozone may cause the latex to become brittle over time. To counteract this, Allegiance evacuates most of the air just prior to sealing. This keeps the gloves intact longer than when paper lidding was used and no evacuation took place.
The Tiromat machine is also equipped with alarms that sound should the temperatures in the forming and sealing stations move outside their preset ranges. If the optimal temperature is 140? F, but good seals can still be made at 138? F, Allegiance operators can program the machine to stop running only when sealing temperatures exceed ±2? F of the acceptable range, Fotis says.
“That way, if for some reason a heater coil goes out and the temperature drops below the acceptable range, the machine shuts down. So, it’s impossible for us to make product outside our validated process windows,” Fotis explains. “This is crucial when you consider the clinical use for surgical gloves.”
The availability of such safeguards is one of the reasons that the company decided to go with Tiromat in the first place. Assistance in training of operators also played an important role.
“The overall service we’re getting from Tiromat is very good,” Fotis says. “It’s really been exciting.”
See sidebar to this article: Local service, validation yield dividends