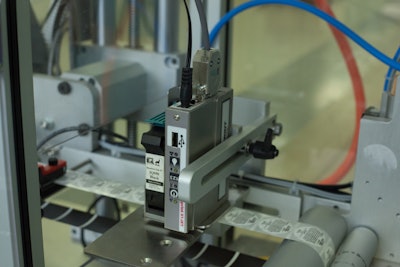
The Contemporary Cosmetic Group, Inc. of Little Falls, NJ, has been formulating, manufacturing, and packaging private-label cosmetics since the mid-’70s, offering items such as lipsticks, powders, eyeshadows, cleansers, toners, and moisturizers, as well as many other makeup and skincare products. Customers include salons, spas, online retailers, and home shopping channels, looking for short runs of custom products.
As with any packaging business, whether producing short or long runs, speed is always an issue, with customers looking for faster and faster turnaround times for finished products. For CCG, the manual application of preprinted product labels on its cosmetic compacts had become a long and cumbersome process. Working with its equipment supplier, Custom Pak Solutions, CCG was able to minimize the steps and maximize the speed of its compact labeling and coding, while also eliminating label waste, through the use of a semi-automated solution.
Speed & flexibility
Before automating the process, CCG was ordering labels preprinted with product information and lot code numbers—a process that could sometimes take weeks. Operators at the Little Falls plant then manually applied the labels to the cosmetic compacts, and unused labels were discarded.
To meet CCG’s requirements, a new system needed to not only provide greater application speed, but also the ability to print lot codes on demand. Another requirement was flexibility. Says CCG President Ivonne Ruggles, “We wanted the capability to work with multiple label and compact sizes as well as multiple ink types.”
The solution recommended by Enzo Lofaro, owner of Custom Pak, was an enclosed system comprising an ink-jet coder, the Autoprint X1JET HP from AT Information Products, coupled with the LABELEX® JR TPM label applicator from Labelpack. “With the machine I proposed, which they eventually bought, everything is done on demand, and in one single step, and most importantly, there is no waste of labels,” he says.
The compact X1JET thermal ink-jet coder, based on Hewlett-Packard technology, integrates a controller and printer in one unit. Programming of the printer for different label sizes can be done through several methods: data transfer using a USB stick, by connecting Ethernet and EIA-232, through the PLC, or via a web interface. Ruggles says CCG uses a USB stick to upload the recipes for the label sizes. Equipment changeover from one label size to another involves just a couple of small adjustments, she adds.
One of Ruggles’ favorite features of the machine is its use of the HP ink-jet cartridge, which she says, “can just be popped right in and out” of the printer. It also requires no maintenance. The cartridge is available in a range of water- and solvent-based inks and can print on coated and uncoated materials.
The second machine, the LABELEX JR TPM, is activated by a foot pedal and applies the preprinted label with the lot code to the cosmetic compacts. The applicator is an entry-level model that provides an easy and linear path for the label reel and a compact footprint.
Streamlined operation
With the new system, an operator manually feeds the compacts into the infeed of the coding/labeling system, where the lot-coded labels are applied. Once the compacts exit the machine, operators glue the powdered product to the inside of the package. Ruggles says the speed of the system is limited only by the operators’ ability to keep up with it. Average run lengths, she adds, are between 1,000 and 2,000; runs from 100,00 to 200,000 are “doable”; and runs from 1,000 to 100,000 are “the most viable.”
Since its installation in Fall 2014, the system has met all of CCG’s requirements. Says Lofaro, “When we integrated the ink-jet coder with the printer, it was a perfect fit for their application. It also has a very small footprint so that you can basically fit it anywhere. The machine is also highly flexible for any future job that they might have. And, the applicator is enclosed in Plexiglas with two electronic barriers, which keeps the operators safe from injury.”