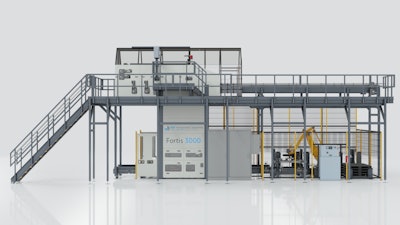
For decades, BW Packaging has offered high-level bulk depalletizing systems that get the job done. However, shared Eric Rohlf, product manager – Palletizing & Depalletizing, at PACK EXPO Las Vegas, the way in which they’ve gone about getting it done has remained the same. One longstanding challenge with this type of equipment has always been accessing the dunnage at the top of the machine following depalletizing. With its new Goldco Fortis high-level bulk depalletizer, the BW End-of-Line division has sought to optimize this process to improve worker safety and ergonomics and enhance production and reliability.
“We decided to design a machine from the ground up that meets the needs of our customers today and in the future,” said Rohlf. “So we packed innovations in a lot of the different areas. It still sweeps packages and sends them out onto a conveyor, but we’ve tried to figure out ways to solve all the problems we’ve seen over the years, even if they’ve always been accepted as something you just did.”
With traditional high-level bulk depalletizers, the layer pads and top frames from the pallet are loaded in a bin positioned around 15 feet off the ground. To collect the dunnage, a forklift driver must align the forks at the top of the depalletizer to retrieve the dunnage and then load a new pallet in its place. The process poses various ergonomic and safety concerns and requires the machine to be stopped, leading to lost productivity.
The Fortis, however, streamlines this process by accumulating the sheets and top frames at the top of the machine in a dunnage stack. Once depalletizing is complete, these materials are transferred back to the empty pallet, which then moves to the ground level via a four-chain hoist. Once the materials have been moved to the floor, operators can use BW’s standard sortation option of robotic sorting of the sheets, top frame, and pallet, whereby the robot picks them and places them into separate bins.
“Try to picture driving a forklift up to a bin 15 feet in the air and picking up a stack of 1,000 pounds of sheets—the sheets are heavy once you stack up enough of them,” said Rohlf. “And now you’re backing out, what happens if that thing catches and things fall? You can bump into the machine and knock a sensor out of alignment, now you’re down. By bringing it all down to floor level, all those problems go away.”
Furthering the effort to reduce downtime, BW introduced sheet levelers, which are particularly beneficial when layer pads become misshapen. If a layer pad isn’t straight, products like cans or bottles can tumble and cause obstructions. The sheet levelers employ fingers that adjust these pads, ensuring a smooth transition and preventing potential jams.
The introduction of sheet grippers with built-in detection is another notable feature. These grippers ensure that if a layer pad inadvertently moves along with the products, it can be promptly identified, thus preventing a jam further down the line. “We can stop it right away and address it, so that it doesn’t cause extended downtime,” said Rohlf.
Moreover, the grippers are adjustable via a panel view screen or HMI, eliminating the need for manual adjustments and further boosting operational efficiency.
Another feature highlighted by Rohlf is the machine’s servo-controlled sweep bars, which enable changeover flexibility for a range of packages. “Depalletizers are expected to run many different types and sizes of containers,” he said. “Where Fortis differs is the ease with which we can switch between container types. Fortis can change from size to size with the push of a button. Servo-controlled sweep bars and automatically adjusted grippers can adjust to the size of the package being run, they can operate at different speed profiles to support cans as they make a transition, and they don’t require anyone to enter the machine and make any manual adjustments.”
The speed of the Fortis is also noteworthy, Rohlf shared. Compared with the industry-standard speed of 2,000 to 2,500 cans per minute, the Fortis depalletizer can handle up to seven and a half layers continuously, for a speed of 3,000 12-oz cans/min.
Regarding the design of the operator interface, Rohlf says engineers prioritized intuitive use. Operators can access all necessary functions within just two clicks, and in the event of a fault, visual cues guide them directly to the problem area.
Concluded Rohlf, “In every area of the machine, we tried to make it forward thinking and not lose what was good about what we did before, but we brought new things to the table that didn’t exist before.” PW