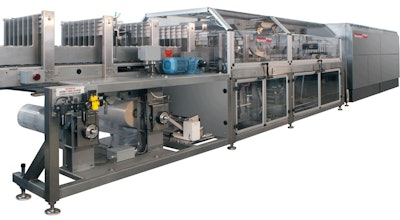
The Multipacker then sends the packs through an energy-efficient heat tunnel to tightly shrink the film around each multi-pack producing a consistent, wrinkle-free bull's eye and bottom seal.
The Tritium provides a low carbon footprint with an energy-efficient heat tunnel, and a reduced amount of overall packaging material used. The modularly constructed, stainless steel multipacker is flexible and adaptable, and comes equipped with easy-access "gull wing" guard doors. These transparent, safety-interlock guard doors provide a clear view of all moving belts and chains, enabling "walk-by-maintenance" by maintenance personnel.
The Tritium Multipacker features both an innovative Robo-Wand wrapping section and precise servo-driven film cutting system. These features allow wide product range capabilities, as well as increased speed and reliability. To facilitate machine maintenance, many steel chains have been replaced with timing belts, which require no lubrication and create a quieter machine.
The 597 Tritium series includes a pull-out film feed module. Operators can now quickly pull the film feed out on rollers for convenient inspection and maintenance. Printed or registered film is used to wrap each multi-pack, which provides a larger area for product information and allows retailers to stock their shelves faster and with less waste. Marketing message can now be printed on the translucent film to promote the cost-saving multi-pack purchase.
The Tritium comes equipped with Standard-Knapp'sOperator Interface, as well as the Zero-Gap II Infeed. The Operator Interface utilizes color touch-screen technology to offer intuitive machine control. Through computer-aided fault recovery, the Operator Interface reduces Mean Time to Recover (MTR), and increases efficiency for a broad range of 24/7 applications. Zero-Gap II Infeed employs electronic sensors to monitor and control product movement, maintaining a constant low line pressure and maximizing machine uptime.