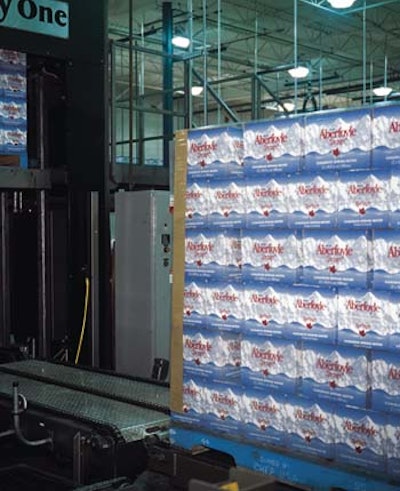
“We’re a low-cost producer with high-end packaging.”
That’s how Mike Eccles describes a key strategy at Aberfoyle Springs of Guelph, Ontario, Canada, where Eccles is plant manager. The packages that best exemplify this strategy are 12- and 24-count cases of 500-mL bottles destined primarily for the club-store market. About 75% of Aberfoyle’s total output is packaged in one of these two cases. “The aim is to sell a club pack, not individual bottles,” says Eccles.
Knowing that pallet loads of cases are commonplace displays in such stores, the company invests in preprinted linerboard for its corrugated cases so that sharp graphics can lure shoppers to the Aberfoyle pallet rather than a competitor’s. The added expense of preprinted linerboard could make profitability elusive. That’s why operating efficiency is all-important, says Eccles.
“We invest a lot in the best machinery we can find,” explains Eccles. “And we train our people like there’s no tomorrow. So we gain very high efficiencies in our plant. That’s how we can afford premium packaging and still keep our selling costs down.”
The “efficiencies” Eccles refers to begin with self-manufacture of polyethylene terephthalate bottles (see Packaging World, February '00, p. 60 or packworld.com/go/aber). Also impressive is the newest bottling line, which is dedicated to 500-mL bottles. Running since April ’98, the line fills PET bottles at 630/min. Most days there are two 11-hour shifts, and on a good day, says Eccles, the company fills 750ꯠ bottles.
Most of those bottles come from Aberfoyle’s own blow-molding operation. But home-blown or not, all bottles enter the filling line through the same Priority One (Waterloo, Ontario, Canada) depalletizer. After an operator removes stretch wrap and bands from the pallets, pallets move into the depalletizer on a powered chain conveyor. With each cycle, a carriage assembly moves into position over the top of the pallet load and then descends and closes in on the top layer on all sides. This assembly transfers the layer from its slip sheet onto a transfer plate, and from the transfer plate bottles are swept onto a matte-top conveyor. The slip sheets are automatically removed by vacuum pickup cups and stacked. Emptied pallets are also automatically stacked in a magazine.
The matte-top conveyor gives way to a tabletop conveyor that gradually narrows. Line pressure converts the bottles from a mass flow to a single-file orientation.
‘Huge challenge’
“As any bottler will tell you, single-filing empty PET bottles at high speeds is a huge challenge,” says Eccles. “Critical areas include close control over conveyor speeds and the amount of lubrication used on the tabletop conveyor.”
Two other “tricks” are employed at Aberfoyle. A water mist is sprayed on the bottles to help eliminate static electricity build-up, thus causing the bottles to separate from each other more readily. And, just ahead of the point where single-filing is complete, a short burst of air aimed at the bottles’ shoulder area helps prevent tipping and also serves to space the bottles out.
Once bottles are single-filed, they’re conveyed into an enclosed filling room that’s overpressured with HEPA-filtered air. Here the bottles enter a monobloc system consisting of three rotary machines: a Krones (Franklin, WI) 78-head Variojet rinser, a Krones 60-valve filler and a 15-head capper from Zalkin, which is represented in the U.S. by Fowler Products (Athens, GA).
Exiting the filling room, bottles are conveyed through a Filtec FT-50 gamma ray unit from Industrial Dynamics (Torrance, CA). It inspects for missing or cocked caps as well as for low fills, and it signals a kickout device to reject any bottle that is unacceptable.
Labeling is next. However, between the Filtec inspector and the labeler, a tabletop conveyor table provides up to seven minutes of accumulation should the labeler or case packer be down for any reason. Like the rest of the conveyor connections in the line, the accumulation table was provided by Priority One. “We like them because they make good, quality equipment and they’re located nearby,” says Eccles.
Just before bottles enter the Krones labeler, a pair of air knives from Sonic Air Systems (Fullerton, CA) blows any condensation off the bottles. “The product is about 50 degrees, so condensation can be a problem,” says Eccles. The difficulty it can cause is in the labeling area, he explains, where the bottle contacts the glue roller before picking a label from the label basket. If too much water is on the bottle when it contacts the glue roller, the water could begin to build up in the glue pot and contaminate the glue. “The air knives are quite effective in preventing this problem, especially in the warmer weather when condensation is heavier,” says Eccles.
Following the Krones Canmatic 24-station cut-label applicator, bottles are conveyed past a Domino Amjet (Gurnee, IL) laser coder that imprints date and expiration date on the shoulder of each bottle.
“The laser is neater and cleaner than other options,” says Eccles. “And there are no consumables. It’s about three times the cost of ink-jet coding, but it’s well worth it because it reduces downtime.” On a line designed to run 22 hours daily, seven days a week, downtime becomes costly.
Sixty cases/min
Next in line is a Douglas Machine (Alexandria, MN) wraparound case packer selected primarily on the basis of its speed. “We need 60 cases per minute,” says Eccles.
The continuous-motion machine picks flat blanks from a magazine and forms them into an L-shape. Bottles, meanwhile, are collated as they move down a track that parallels the path of the cases. When the proper number of bottles, 12 or 24, have been collated, they’re pushed onto the case blank, and the remaining flaps and end panels are folded and sealed hot melt.
Supplied by Atlantic Packaging (Toronto, Ontario, Canada), the 26 ECT B-flute cases have a 150# outer liner that is preprinted in four colors plus varnish. The case also incorporates a die-cut window on the front panel, so consumers can see the bottles inside, and two die-cut hand-holes.
Cases discharge onto an incline conveyor and then to an overhead conveyor that brings them to a high-level Patriot palletizer supplied by Priority One. Eccles says it’s practically a prototype, as Priority One has traditionally specialized in low-level palletizers. With the Patriot, Priority One seeks to meet the needs of customers operating high-speed lines.
The palletizer builds two layers of cases at a time, and it has a rated speed of six pallets/min. Photocells count cases as they move into the machine and signal a PLC that in turn “knows” where to direct a case and whether it needs to be turned.
When a pallet is full, it advances to an ITW Muller (Glenview, IL) stretch wrapper, the final piece of equipment in the line. Operators manually place corrugated corner posts on all four corners to protect the attractive cases during distribution. The stretch wrap holds them in place.
Since the new line was installed, says Eccles, Aberfoyle’s ability to meet club store demand has been greatly improved. Growth in the U.S. has been especially impressive, and it doesn’t appear the firm will slow down anytime soon. Already covering some 220ꯠ sq’, Aberfoyle’s Guelph plant is in the middle of a 100ꯠ sq’ expansion. As the company continues to grow, its fundamental emphasis is unlikely to change.
“We’ve built our brand around low pricing and premium packaging,” says Eccles. “It’s a challenge, but it’s worked.”
In a hurry? Request more info via Web-based reader service by clicking on the reader service number.
Or you can jump right to their Web site.