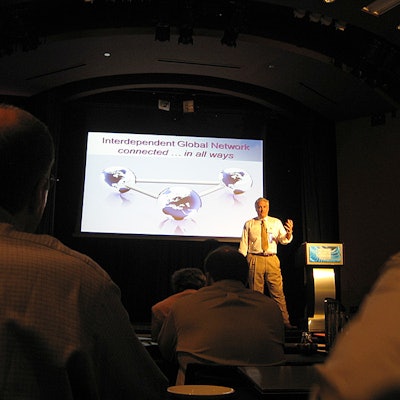
This content was written and submitted by the supplier. It has only been modified to comply with this publication’s space and style.
At the recently concluded Packaging Automation Forum in Chicago, a surprisingly strong turnout of packagers, machine builders and automation suppliers heard loud and clear what’s need from automation technology to make packaging operations more effective.
Kraft touts OEE
Kraft Foods’ worldwide performance indicator program manager, Mark Hanley, opened the session with case studies that “supply data that means something.”
Hanley says first to identify the critical asset – what’s shutting down the line? It may be a machine fix, balancing the line. Various lines he’s worked on have benefited by Zarpac’s OEE (Overall Equipment Effectiveness) system. It provides more granularity of data needed to properly analyze root causes. The SAP Catalyst module also requires the additional granularity.
Catastrophic failures don’t happen that often – it is the frequent and recurring stoppages he’s focused on. He used the analogy of stop and go traffic being harder on machinery than highway driving.
Data collection and reporting must fit the budget and level of automation on the line. China, India and Malaysia plants are very manual, whereas some plants in the US, data acquisition gets much deeper than others.
The operators must own the OEE system, Hanley asserts, and if they do, they won’t want you to ever take it away. It gives them a view into how their lines are running, it can astound them at times, and it helps them fix the problems immediately, right on the floor. Operators like it because their job is actually much easier if the lines are running smoothly.
Next? Hanley plans to use data now to drive finite element analysis on new equipment and improve how they set up lines. The five year plan calls for OEE to be installed on new machines, once a standard is agreed upon.
TMI – too much information -- was a problem at first, eight years ago. But finding the right information rather than raw data, standardizing to achieve comparability, and providing reports for each level has created a powerful tool. OEE shows how a line, a plant or SKU has done over time. At the plant level, they can look at individual machine performance for action by lean, Six Sigma and Kaizen groups.
And with tight capital budgets, Hanley concludes, OEE allows packagers to improve the lines they have now, with what they have on hand.
Edson applies innovative, supportable ‘off the shelf’ technology
Edson Packaging Machinery president Rob Hattin showed how his company paired its case packing innovation and application knowledge with the technology and global support of Schneider Electric’s ELAU packaging automation specialists.
The machinery in question is a robotic case packer. Part of a compact, cellular concept that allows for flexible siting and reconfiguration, Edson’s RDp 270 combines ‘off-the-shelf’ subsystems readily supported by Edson using Schneider Electric’s worldwide presence.
By replacing traditional mechanical components that Edson must fabricate itself with off-the-shelf mechatronic modules, the company has created what Hattin refers to as the Dell manufacturing model for packaging machinery.
Hattin created a ‘skunkworks’ outside the company’s normal design process. No one on the team of five had more than eight months with the company, and therefore no preconceived notions.
Recognizing that a world class machine demonstrates form and not just function, he brought in an industrial designer – who sketched out the machine frame the way that sports cars are concepted.
Core to the design, mechatronics would replace conventional mechanical parts wherever possible with software and servo motion.
Next, robotics and servo modules would supplant conventional servo motion to cut the electrical cabinet in half, make the machine smaller, more flexible and less dependent on custom-made parts.
The machine itself would be modular – allowing a second complete robot cell to plug into the first and doubling throughput as needed. Unlike the company’s conventional monoblock designs, case erecting and sealing are individual cells that are much easier to install around pillars and obstructions common to existing facilities.
The details were equally critical to the global design – from all metric fasteners to Category 4 safety system to easily cleaned surfaces to international programming and network standards.
With Schneider Electric, Edson can source a complete, integrated solution, from the electrical cabinet to robot arm to operator interface, incorporating the world’s only automation platform purpose-built for packaging.
It would simply not be commercially viable for Edson to develop the infrastructure it would take to diagnose, manufacture, ship, stock and install the many individual wear parts of a conventional machine in many different countries.
Through his automation supplier’s network of 114,000 people in over 100 countries, Edson can ensure support for all the major components of its mechatronic packaging systems, wherever a consumer goods maker decides to locate its plants. And that includes the emerging economies that continue to grow under adverse economic conditions, where Schneider Electric derives fully 32% of its revenue.
Pfizer calls for pharma to adopt OMAC standards
In pharmaceutical, automation is designed in silos, explains the senior manager of global manufacturing service for Pfizer Inc., Murugan Gavindasamy. Even if major industry standards are introduced, pharma tends not to adopt them.
New technologies are subject to interpretation by different parties. There is minimal connectivity to IT systems. It takes a lot of expensive reengineering to reinvent the technology that’s required.
Automation has also been seen as a cost of compliance to regulatory requirements, not an opportunity to become more efficient. Efficiency in pharma averages 20 to 40%, compared to 80% in consumer packaging.
But these paradigms are shifting in a global manufacturing and supply environment that has brought pressure to reduce cost, reduce waste and become green.
Gavindasamy says the control system must be seen as an enabler to address gaps in data acquisition, to better understand and improve processes, to minimize errors and maximize quality/throughput.
Gavindasamy says his company recognizes the need to ROI-justify automation, and to develop flexible, modular automation systems because one solution does not fit all. What’s more, equipment may need to be moved from site to site, or even between countries.
Standardization’s role is to improve time to market, reduce inventories from 100 days to JIT, to maintain consistency and reduce total cost of ownership. Standardization reduces the need for custom applications that are difficult to support. It makes installation, integration and validation more cost effective, it improves uptime and reduces spares and training requirements.
Gavindasamy proposes formation of a users group to list and agree upon requirements, starting from a high level, and to develop standard specification documents that will be acceptable to users, OEMs and automation suppliers.
The granularity would depend on the need, and the resulting Guidance Document would be endorsed, adopted and promoted.
The elements would include standardized architecture, simplified integration, and standardized interfaces for uniform exchange of data, both horizontally and vertically. Common documentation methodologies are needed, and standardized protocols such, as OMAC Packaging Guidelines, RFID and PAT.
Gavindasamy said that the pharmaceutical industry needs OMAC as a base value to build on. Pfizer has embedded OMAC standards in their specifications. He says it is necessary to drive OMAC adoption from the user up.
About Schneider Electric ELAU Packaging Solutions
Schneider Electric ELAU Packaging Solutions is the only automaton system in the world purpose-built for packaging machinery.
Schneider Electric ELAU Packaging Solutions equips over $1 billion worth of packaging machines annually, with over 45,000 systems already deployed worldwide.
The market demands packaging operations that are more flexible and efficient to fulfill marketing, supply chain and global business strategies. Schneider Electric innovations have enabled a revolution in mechanical, software and hardware modularity to deliver these agile packaging systems.