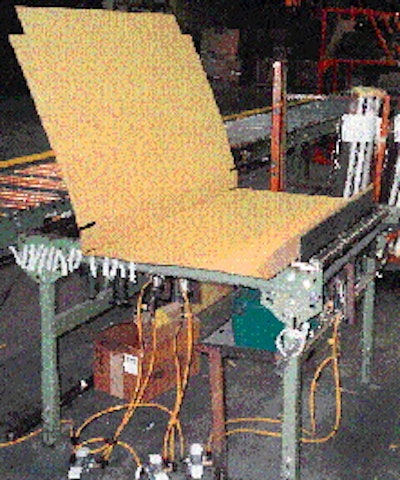
By its nature, packaging is designed to protect the product it holds. But by accident of design, it sometimes doesn't protect the operator. Workers at Steelcase, Inc., Grand Rapids, MI, learned this the hard way. After years of trying to fold the doublewall corrugated tray blanks for large metal desktops, workers in the packaging department ended up with plenty of sore wrists. That in turn affected productivity. "At any given time, about four out of 16 people were on light-duty type jobs," says John McCrackin, senior packaging engineer at the world's largest manufacturer of office furniture. The problem? Cut score lines on the 200#-test, doublewall B/C-flute corrugated die-cut tray blanks were troublesome for Steelcase workers to break, particularly during the summer months, when the humidity negatively affects the corrugated cut-scoring process. And it wasn't just a case of bad corrugated from one supplier. "No matter what supplier ran them, they all had problems cut-scoring the materials," attests McCrackin. "So it was just a bad package design." Charged with finding a solution, McCrackin gave serious thought to which areas actually needed the most protection. The flat desktops weigh from 100 to 250 lb and measure 30" to 120" long, 25" to 30" wide and 3" thick. Two other metal components in the package are packed flat, on top of the desktop. "I asked myself what are we really trying to protect?" explains McCrackin. "It's sheet-metal office furniture which can stand up to a lot, so all we're really trying to do is protect the corners. If that's the case, then why are we putting it in a multi-walled, multi-layered corrugated tray?" he asks rhetorically. With corner protection in mind, he began to consider different materials and package designs. However, he ended up coming back to one of Steelcase's main corrugated suppliers, Pactiv Inc. (Evanston, IL), formerly Packaging Corporation of America. Working with a corrugated designer at Pactiv's Grandville, MI, facility, McCrackin developed a unique corrugated corner that provides the requisite protection. One thing that makes the corner unique is that it doubles as a corner post for pre-assembled desks. The 200#-test, C-flute corners, with a nonabrasive coating, are shipped flat. At Steelcase, the corners are assembled in batches by a worker who folds them and inserts them into a 3M-Matic(TM) S-857 "L" clip applicator from 3M (St. Paul, MN), which applies a 4 1/2" piece of filament tape to the corner, locking it into shape. With protection beefed up in the corners, Steelcase scaled down body protection where it wasn't needed. The company switched to a singlewall five-panel folder, a standard wraparound case design made of 200#-test, C-flute corrugated. It is also supplied by Pactiv. The result is a package intelligently designed to put protection where it's needed and reduce it where it isn't. The benefits: * Repetitive stress injuries to workers and the need for light duty have been eliminated. * Corrugated consumption has been reduced by 274괌 lb/yr. * Cycle times required to assemble each case has been reduced by 90%. * Savings from materials and labor total $179ꯠ annually.