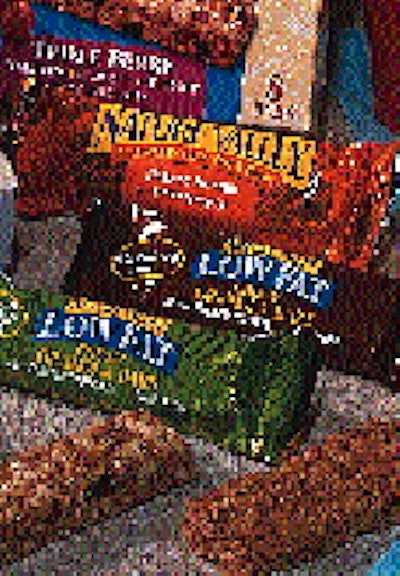
For General Mills, Minneapolis, MN, high-barrier, cold-seal films represented an opportunity to save money, improve graphics and potentially increase packaging speeds for its venerable Nature Valley Granola Bars. The product had been wrapped in a paper, polyethylene and foil combination largely unchanged since its late '70s debut. The switch was completed last summer. The barrier component that makes the new film possible consists of 60-ga Torayfan® PC-1, which is a metallized oriented polypropylene film supplied by Toray Plastics (North Kingstown, RI). Printpack (Atlanta, GA) converts the structure, adhesive laminating PC-1 to an outer 75-ga OPP from AET Packaging Films (Wilmington, DE) that Printpack reverse prints via flexo in six colors. The new structure is 1.6 mils compared to 4 mils previously, and material costs have dropped by more than 10%, according to Linda Cook, packaging engineer for General Mills. Barrier was critical for General Mills' application, especially for the moisture-sensitive low-fat variety. (The same structure is used for its regular variety.) From converting through packaging and distribution, the moisture vapor transmission rate--.01 g/100" sq/24 hr--is said to remain constant throughout the life of the film, since it resists flex-cracking. Cook conducted simulated shipping tests and confirmed that the new package significantly reduced the problem of flex-cracking during distribution. The company won't divulge shelf life, although it does confirm that it hasn't changed. After experimenting with PC-1 during machine trials, Cook found that using polypropylene in a cold seal application permits improved line efficiency with less waste. For the present, packaging speeds at General Mills remain the same, limited by other equipment on the line. But the promise of increased productivity in the future are part of what attracted General Mills to PC-1. By their nature, cold-seal films can be run faster than heat-sealable ones. The reason? "The rubber latex cohesive coating doesn't require heat on the sealing jaws to work, just pressure," says David Rieckmann, a product development engineer at Printpack. "[The film] can run at very high line speeds. In the confectionery market it's been done for several years now." The only equipment change that was required was new sealing jaws for the flow wrappers. Technical considerations aside, the other main impetus for a switch was plain good looks. General Mills wanted a film that would enhance the product's appearance to the consumer. "PC-1 moved us into the forefront of the industry in terms of packaging," opines Cook. "The new, updated look of the package says 'fresh' to the consumer."