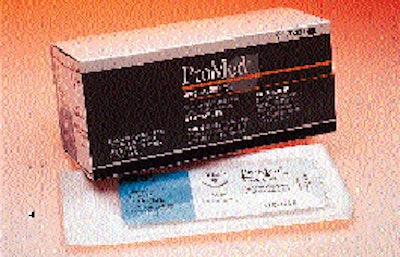
Since its beginnings 17 years ago, Englewood, CO-based Cottrell Ltd. has grown from a distributor of a single line of surgical sutures to one handling over 300 medical and dental products.
Last February, the company expanded its business to include not only distribution but also manufacturing of its own ProMed® line of surgical and dental sutures. That meant installation of both manufacturing and packaging lines, the latter anchored by a thermoformer/sealer from Klockner Medipak (Clearwater, FL).
Cottrell's director of operations A.J. DiMercurio decided to buy the Klockner Compacker 2 thermoformer partly because he liked a Compacker 8 he previously purchased for a former employer. "I had looked at many brands of equipment in the past and had chosen Klockner," says DiMercurio, "so this time it was just a matter of going back to the top suppliers out there. I carefully weighed the features of each and the type of package we wanted to make, and Klockner not only offered the best equipment but the best service."
Though a small company competing against suture manufacturers that are giants, Cottrell has been able to build a solid reputation, in part because of its peelable package. "We offer the technique preferred in many hospitals," says DiMercurio. Instead of a fin-seal package produced on a flow wrapper, where the package must be torn open to access the suture, Cottrell offers a peelable blister pack. "Our concept for the package is built around the idea of allowing the practitioner to get into the package quickly for fast and efficient application. We feel this affords the surgeon or end-user a little more control over the suture."
Not all sutures are the same. Thicknesses, lengths, needle curvatures, materials, features like flexibility or absorption--all these vary for different medical and dental procedures. For Cottrell's packaging purposes, sutures fall into one of two major categories: nonabsorbable and absorbable. Most common are nonabsorbable. Cottrell packages them in a polyvinyl chloride tray using DuPont's (Wilmington, DE) Tyvek® as a lidding.
Absorbable, or "catgut" sutures, are used in procedures where absorption into the organ after healing is preferred over removal. These collagen-based sutures are made from ovine or bovine byproducts and require an alcohol-fill solution to keep them intact. Cottrell uses the same PVC forming stock for these, but it uses a foil laminate for its barrier properties to maintain the proper alcohol-fill level in the product.
Likewise, dental sutures vary from medical sutures. To keep them all straight, and to facilitate selection within the operating room, industry-standard color codes were developed. Packaging-wise, this meant varying labels for the packages.
The packaging process varies, too. "The FDA has required all medical device manufacturers to validate not only equipment but the process for making that particular package," explains DiMercurio. Absorbable and nonabsorbable sutures each require a separate validation, with separate heat-seal requirements. These variables translate into one thing for Cottrell: the need for quick changeover.
"The Klockner form/fill/seal blister thermoformer allows us to produce state-of-the-art packaging for our new medical and dental sutures," says DiMercurio. "The Compacker-2 gave us the flexibility to change over quickly. We select from the microprocessor control the desired product set-up, which resets heat parameters, and we're ready to go within twenty minutes or so." The machine is controlled by an Allen-Bradley (Milwaukee, WI) SLC 500 microprocessor, operated through a touch-screen that allows simplified control of all packaging parameters. "Once you establish the validated parameters for the package, they can be programmed into the microprocessor so that no package will vary outside of those parameters," says DiMercurio. "If, for some reason, the parameters aren't met, the equipment shuts down and notifies the operator."
Peelable blisters
The peelable blister package begins with a roll of 10-mil thick PVC sheet from American Mirrex (New Castle, DE). It's fed through the CP-2 for blister forming two-up. Depth of draw is .040", according to DiMercurio. The tray measures 1 3/8" x 4" x 1/8".
After cavities have been thermoformed, sutures, which have been previously hand-wound onto carrier cards, are manually placed into the PVC thermoform. If absorbable sutures are being packaged, the blisters proceed to a metering station, which consists of an Ivek (North Springfield, VT) Digispense(TM) 8 meter. A total of 1.25 mL of alcohol-fill solution is pumped into the tray.
High-quality labels
Meanwhile, mounted above the forming stations, a printing station handles lidding. "In the medical profession your label is very important," says DiMercurio. Cottrell's lidding is preprinted with only industry color codes. A 13-mil adhesive-coated Tyvek from Oliver Products (Grand Rapids, MI) is used for nonabsorbable sutures. For the absorbable version, Cottrell uses a 4-mil lamination of polyester on the outside and heat-seal coated foil on the inside. It's supplied by Tolas (Feasterville, PA). All text, including logos, nomenclature, and other essential information, including an illustration of the suture, is printed flexographically on an Adolph Gottscho (Union, NJ) Model 806-4 printer. As forming and filling take place below, the lidstock first goes through a printing station, then air drying before meeting the blister trays at the sealing station.
Here, lids and trays are heat-sealed together. The CP-2 can reach speeds from 60 to 90 packages/min, with absorbable sutures running at the low end so that the alcohol doesn't spill during sealing.
From there, they pass through a cool-down station and index for die-cutting two-up. The sealed blisters then wait for final inspection by one or two people. Blisters are then manually inserted into the secondary packaging, a pouch made of clear polyester on top and white Tyvek on bottom. These are sent to Cottrell by its sister company, which makes them. Materials for them are supplied by Cur*Med (Oshkosh, WI).
Once thermoforms are inside their pouches, they are manually heat-sealed.
Electron beam sterilization is next and finally, cartoning into groups of 12 for distribution to medical offices.
The ProMed line of sutures has been on the market since early 1995, and customer acceptance has been excellent, says DiMercurio. "We are reaching many new customers who want new products--and the CP-2 fits right into that picture for future production."