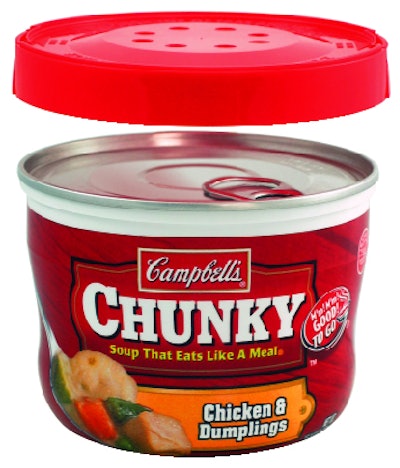
High-speed, highly automated packaging systems play a key role in Stull Technologies’ (www.stulltech.com) ability to meet growing demand for the snap-fit, polypropylene caps on Campbell Soup’s 151⁄4-oz microwavable soup bowls.
Complicating Stull’s path to automation was the cap’s unique design, says Jason Stull, senior director of marketing and administration at this 60-year-old, third-generation manufacturing company based in Somerset, NJ.
"Molded into the cap on opposite sides are two flex-lock points, which is why we call this a ‘double locking overcap," explains Stull. "These make it easy for the consumer to remove the cap, open the ring-pull end, and snap the cap firmly back in place for microwave heating. No existing packaging equipment would accommodate Stull’s unique design, so we sourced custom solutions."
Two automation integrators were identified to provide the robotic solutions Stull required.
Stack molds
CBW Automation (www.cbwautomation.com) was tapped for Line 1 and Gima Advanced Technology (www.gima.com) for Line 2. Since Line 1 came first, it’s a good place to begin.At the head of Line 1 are two 550-ton Cincinnati Milacron (www.milacron.com) all-electric injection molding systems. Each is equipped with a stack mold supplied by StackTeck (www.stackteck.com) that produces 32 parts/cycle. Stull Technologies is committed to all-electric technology, having brought in more than 15 new machines in the past few years. Assistant vice president of manufacturing Bernard Banks III is a fan of the all-electric injection-molding system and the stack-mold tooling.
"Electric is over 60% more energy-efficient than hydraulic," says Banks. "In addition, the shot-to-shot repeatability is better, which lets us manufacture in a tighter process window. That means we use less material, which aids our efforts to be more efficient and more sustainable.
"The stack-mold tooling maximizes output while minimizing the clamping force required. If we had a single-face, 16-cavity mold, we’d need a 500-ton press. With the stack mold, you can typically double your cavitation with only a 10% increase in tons of clamping force."
Each measuring just over 4 in. in diameter, the freshly molded caps are mechanically oriented so that all are right-side up. Then they are conveyed in the direction of a flighted incline conveyor that leads in turn to a laning device that sorts the caps into eight parallel lanes. These lanes lead to a "waterfall" device that gently reorients the caps from a horizontal to a vertical position. Sensors along the way cause gating devices to direct most caps into two adjacent lanes at a time. When each of these two adjacent lanes has 40 caps neatly and compactly nested together in a "log," the two logs are advanced to a forward position. From here, a twin-head robot with a vacuum end effector picks up the two logs and carries them at a right angle to a staging area. When four logs of 40 caps each are in this staging area, a second robotic head with a similar vacuum end effector picks all four and puts them in a corrugated case. With three layers of logs in a case, the case indexes forward to a 3M (www.3m.com) case taper.
Additional elements of automation are incorporated in the line both upstream and downstream, including an automated case erector from Combi Packaging Systems (www.combi.com). Downstream from the case taper is a PZ Pilot small-character ink-jet printer from Squid Ink (www.squidink.com) that imprints production data on the corrugated case; a palletizer from Wyard Industries, a Barry-Wehmiller (www.barry-wehmiller.com) company; and a stretch wrapper from Wulftec (www.wulftec.com).
On to Line 2
No sooner had Stull brought Line 1 into commercial operation than it found itself looking at even higher volumes from customer Campbell Soup. So Banks and manager of sales engineering Jameson Stull began exploring a second automated system. This time the trail led to Gima and a side-entry robot that removes freshly molded caps from the molding tools.
"We were very pleased with the solution provided to us by CBW," says Jameson Stull. "The gravity-feed approach was a more conservative way to automate in that it wasn’t as aggressive, from a technology standpoint, as take-out robots. But with the second robotic installation, we felt we needed to do some other things. We wanted more control over the molded caps along each step of the way. These parts are like Frisbees; they want to fly all over the place. So a key goal the second time around was to capture parts right from the mold. Side-entry robotic take-out gives us that.
"Greater simplicity was also important to us. If you think about the series of steps involved in our first robotic line, it includes gravity drop from the molds, conveying with a flighted incline conveyor, accumulation, and collation into logs. Then the logs are picked by two separate robots and placed in corrugated shippers. At every step along the way, there’s a chance for error."
Gima reached Stull’s radar screen not so much on the strength of its expertise in packaging, but rather because of its expertise in handling injection-molded CD jewel cases. Making Gima all the more attractive was its experience in integrating machine vision inspection into an installation. In Stull’s Line 2, the inspection system selected by Gima and Stull is an Insight Series 5000 unit from Cognex (www.cognex.com).
"Vision inspection was extremely important to us in the second installation," says Jameson Stull. "We’re looking for five different defects on every single cap. Should one of these defects be detected, an air blast diverts that closure from the line."
Significant differences
Line 2 has been in production since last October. While it has much in common with its predecessor, it represents a significantly different way of skinning the cat. Molding is once again done by a Cincinnati Milacron 550-ton system with the same 32-cavity stack mold from Stack Teck. But this time, there’s only one molding machine. And rather than discharging caps to a gravity-feed system that turns them into logs, this time a side-entry robotic picking system picks the caps from the mold and reciprocates back out of the mold to its starting position. Here a pair of robotic picking arms removes all 32 caps and places them two-across on an outfeed conveyor leading to a stacking system. The side-entry picking robot then strokes back into the mold for another 32 caps.
Vacuum sensors verify that all 32 injection-molded parts have been picked from the mold. If a part has not been picked, the controls system signals the tools not to close, and an alarm is sounded. This prevents the mold from closing on a formed part, which, if allowed to happen, could cause damage to the tooling.
Caps are conveyed in a two-across orientation out of the robotic pickers and past the Cognex vision system. It uses four cameras, two per lane, to compare each part’s parameters with preprogrammed parameters to make sure quality is spot-on. One camera looking straight down at the caps checks for ovality, misshapen finger tabs, bent parts, and the presence and correct size of all eight vent holes. The second camera in each lane looks from a side angle for "short shots," a term used by injection molders to describe a part that didn’t get a full shot of molten plastic. It’s usually caused by heating irregularities in the injection-molding system.
Joe Sebastian, a process manager at Stull, says the Cognex system is considerably more advanced than standard vision systems Stull has used in the past. He notes that each camera has not only the optical components that permit it to capture an image, but also a digital signal processor that runs the vision algorithms. In other words, it takes pictures
"This vision system has more processing capabilities and more-powerful software built in, which is one reason why we can check for five different things," says Sebastian. He also notes that the new vision technology came with a learning curve, but the benefits gained in terms of efficiency and part quality made it all worthwhile.
and it analyzes whether or not what it sees is within parameters. If a part is bad, the system signals the line’s central controller so that the part can be automatically rejected.Custom-made stacker
Caps exit the vision inspection station and move toward the custom-made stacking system. It uses vacuum cups to pick the two-across caps four at a time. It then folds out so that the caps can be fed into four continuous, parallel rows. At this point, the continuous rows must be collated into logs of 40 caps each.
"Forming the logs might be the most challenging part," says Jameson Stull. "The parts are so sensitive, since they’re just out of the mold and are still shrinking."
Back-pressure control is crucial. It’s assisted by a system of brushes and bristles that keep the caps nested and perfectly spaced. Also essential is a reciprocating overhead portioning device that meters out four 40-count logs to a forward position from which they can be picked by a robotic head with a vacuum pickup end effector. This robot then puts the four logs into a case three layers high. A high-flow vacuum permits the end effector to pick the relatively heavy load cleanly and consistently with no need for a mechanical assist.
The controls system governing the Gima robotic system is a PC-based solution from B&R (www.br-automation.com). "We prefer servo motors where possible," says Gima’s Robert Bird, "and the side-entry robot uses two, also from B&R. Pneumatic actuation is used for the robotic picker that takes caps from the side-entry robot and for the downstream stacker and case packer."
Case erecting on Line 2 is done on a Combi system just like the one on Line 1; case taping on a 3M unit is also identical.
Palletizing of full cases on Line 2 is handled by a Stacker system from TopTier (www.toptier.com). With a compact footpint of 10 x 12 ft, the Stacker includes a palletizer, a pallet dispenser, and a full-load discharge. A Category IV safety enclosure and redundant operator-protection measures ensure worker safety
The final step in the automated process is stretch wrapping of pallets, which is done on the same Wulftec system used for Line 1. When asked about parts/min, Stull was reluctant to be specific. But Jason Stull says that the two robotic cells combined produce several hundred thousand parts per day.
Watching the two robotic systems in operation and listening to the Stull team describe them is a vivid reminder of how an infusion of new technology can propel a manufacturer into the future. And apparently, we ain’t seen nuthin’ yet.
"We’re moving from a day when an operator was able to operate, at best, two molding machines, to a day when an operator will run three injection-molding machines, three assembly operations, and in some cases more," says assistant vice president of manufacturing Banks. "We’ll continue automating, too, and as we add more vision to the operation, we’ll take even more cost out."
Jason Stull puts it this way: "If we expect to provide the latest in closure innovation and manufacturing to our customers, we need best-in-breed technology on our plant floor."
.