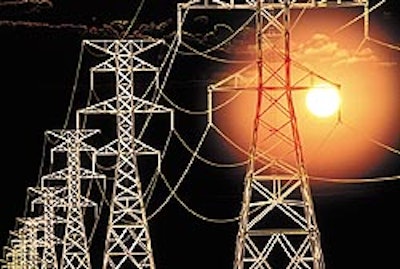
Operations executives accustomed to simply flipping a switch here in the United States were amazed and frustrated by the trials and tribulations that foreign plants experienced in locating, keeping, and “cleaning” sources of power, particularly electricity.
Not only did power interruptions create waste, downtime, and underutilized labor, it made it virtually impossible to duplicate the kinds of ‘round-the-clock manufacturing that is so common in the United States. For example, in this issue (see p. 50), we report on Heaven Hill Distilleries, Bardstown, KY, buying bottles from a Louisville blow molder, Captive Plastics, that produces polyethylene terephthalate bottles on a 24/7 schedule, keeping the blow molders cycling away no matter which shift is monitoring them.
That blow molding operation, like so many other plants, depends on a consistent supply of good electricity. If those machines experience an unplanned shutdown, skilled machine operators turn into maintenance workers to remove all the fast-hardening melted resin in the silent extruder and melt channels and dies.
In the last couple of years, many parts of the United States have been surprised by power outages, some lasting for several days. But floods, tornadoes, ice storms and other natural disasters join the man-made failures of poor planning and failed energy management that have created power problems in virtually every part of the country.
In the recent winter, shortages of natural gas drove heating prices practically out of reach for many consumers. Gasoline prices this summer are expected to approach the levels that Europeans have been paying for years.
In the last few weeks, Packaging World has had no shortage of press releases related to the energy issue. Some promote high-efficiency motors and drives that can bring energy cost savings to manufacturers. Others report how energy management software can help companies manage their energy needs. Still others describe how agreements to outsource energy management to a sole supplier can pay dividends. Other companies display equations that can prove the value of back-up power generation capabilities. Any or all of these may be sound investments, both short- and long-term.
One little nugget caught my attention. Schneider Electric (Palatine, IL) reports that fully 8% of the total U.S. electricity consumption today can be attributed to the Internet! Now, in the grand scheme, 8% isn’t huge, but Schneider claims that the Internet today consumes more electricity than the steel industry, the pulp and paper industry, and U.S. chemical industries combined!
Now, let’s keep in mind that this isn’t just those chat-room addicts we hear so much about. Perhaps the lion’s share of Internet use is to power e-mail, and a major part of that is business communications and research. But I wonder what that percentage would rise to if we added in the power used by all the computers (including the one used to write this column)?
Some of us remember—often fondly—producing virtually the same type of copy on manual typewriters, and later on early-generation, network-free computers that were turned off at every opportunity, if for no other reason than to avoid overheating.
Think about all the electronic controls on your packaging lines that, some time back, replaced mechanical devices that didn’t use much electricity. As you’ve read here before, these controls and business computers continue to be cited as one of the main reasons our country’s industries continue to improve levels of productivity, as measured in worker hours per unit of production.
As proud as I am of these figures, and especially the role of packaging in improving productivity numbers, I have to wonder if we shouldn’t have a parallel index that measures our production per unit of energy consumed. My guess is that, in the future, the cost of virtually everything is going to become increasingly more dependent on energy costs and decreasingly so on labor costs. I’m not saying that the importance of manufacturing labor will decline in real terms, but I think it will in proportion to the increasing importance of energy costs. If you don’t agree, I suggest you talk with a packaging converter in California—but you’ll have to do it soon.