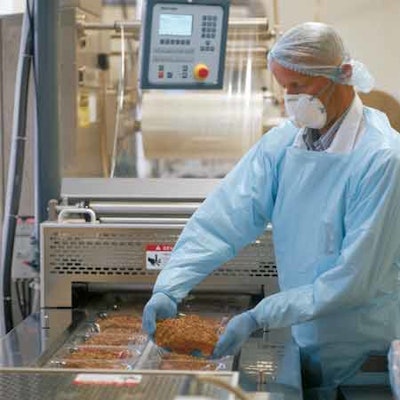
Convenience food is no less popular in Europe than it is in the U.S. For evidence, look no farther than Brandenburg Vlees en Vleesproducten BV. A meat producer and marketer in the Netherlands, this firm has grown its business by focusing on products that taste good and are conveniently packaged.
“We manufacture tasty convenience products, such as pre-spiced joints, that need only be heated in the oven by the consumer before eating,” says Loek Brandenburg, who runs the family-owned firm together with his brother Hans. “We do all the preliminary work beforehand.”
Since the summer of 2005, Brandenburg has been using an R250 FormShrink packaging machine supplied by Multivac (www.multivac.com). Pre-portioned pieces of meat are given a tailor-made shrink package on the automated inline system, a style of packaging that was once only possible with pre-made shrink bags and a vacuum chamber system. Multivac developed the FormShrink process in co-operation with film producer Krehalon (www.krehalon.nl), which was the first to offer a roll-fed shrinkable film capable of performing like a shrink bag. Once the FormShrink process is completed, this highly transparent film fits snugly around the product without any wrinkles or excess film. The skin-tight FormShrink package gives the product exceptional stability and helps it to stand out from the competition.
Loek Brandenburg is enthusiastic about the new machine: “We are under a lot of pressure as a supermarket supplier, particularly in view of the fact that the market is unwilling to accept price increases,” he explains. “We are forced to increase our efficiency by taking different measures, such as highly automated production, in order to be able to operate profitably.”
He says this is exactly what the company has achieved with the Multivac solution. The FormShrink machine has replaced the three chamber machines that used to carry out packaging in conventional shrink pouches. Substantial labor cost savings are realized as a result while the appearance of the product has been improved.
“We used to need two employees for each chamber machine,” says Brandenburg. “One would place the pieces of meat into the pouches and the other would operate the machine. Now there is just one operator at the machine infeed end, who loads the meat, and another one at the discharge end, so that we have been able to reassign four employees.” Brandenburg kept one of the chamber machines to eliminate bottlenecks during seasonal peaks or special campaigns.
Early adapter
Brandenburg is among the first to put FormShrink packaging into commercial production. The technology was introduced by Multivac in 2004. Thermoforming at Brandenburg is done four-up at a speed of about seven cycles/min. Tooling inserts permit the firm to go from a 40-mm to a 100-mm (1.5” to 4.0”) depth of draw. Thermoformed cavities are filled manually. The cavities are then evacuated and sealed to the upper web under the application of pressure and heat.
An MR cross-web pressure-sensitive labeler from Multivac is mounted above the discharge area just downstream from the sealing chamber. Integrated into the labeller is a Markem (www.markem.com) thermal-transfer printer that puts variable information—date, weight, bar code—on the film label. The label is then applied to the top web of the package. Packages are cut with special tooling, which removes excess film, and subsequently passed through a steam shrink tunnel to activate the film's unique shrinking properties, creating a perfect, skin-tight package conforming to the unique contours of the product.
The transparent shrink film, which Krehalon developed specifically for the FormShrink process, brings distinct advantages to processors. The film has unusually high puncture resistance and sealed seam strength, in spite of its thin construction. The lightweight material also serves processors well in terms of cost to purchase as well as recycle. “Our new line consumes substantially less packaging film than the shrink pouch process,” notes Brandenburg. “The total weight of plastic film needed per pack is lower, which reduces not only the material costs but also the recycling charges, e.g. for the ‘Green Dot' scheme.”
Both forming web and lidding material are six-layer coextrusions that include ethylene vinyl alcohol as a barrier layer. Because the FormShrink process creates a package that conforms exactly to the varying weight, shape and size of the contents, every individual item is only given as much packaging as is necessary. Product weights of between 450 and 700 g (1 to 1.54 lbs) are processed and the sizes can vary according to the customer, the required retail price, and the order.
“The investment in the FormShrink process is right in line with our company philosophy of supplying high quality at reasonable prices,” says Brandenburg. “The machine produces packs with very strong visual appeal that present our product to the customer with a high-quality image. Thanks to the additional automation and the innovative new shrink film, we have at the same time been able to save costs, which guarantees us high flexibility in the markets we supply. We have found Multivac to be a reliable partner, who not only provides us convincing solutions for new production operations but is also there to give us theoretical and practical advice if problems ever arise in day-to-day production.”
Brandenburg's convenience products have been a big hit with consumers, earning the company a prominent position on shelves in Dutch self-service supermarket chains. Additional distribution is planned for Germany and Great Britain in the near future.