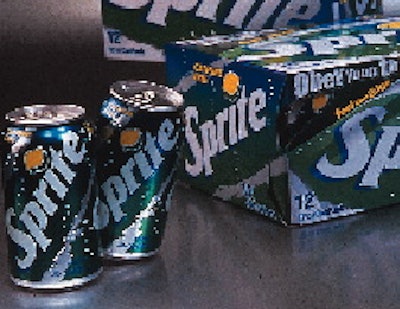
This time it's a 12-oz Sprite® can that is said to be the first ever that's debossed in register. The can is being test-marketed in Portland, OR, beginning this month. American National Can (Chicago, IL) makes the can in its Kent, WA, plant using machinery specially developed by Alcoa Packaging Equipment, a subsidiary of Alcoa (Pittsburgh, PA). Alcoa's Model 333 REM is a 24-station rotary system that uses laser optics to find the location of a specific reference point on the decoration of each can. Then its high-speed servo motors cause the can to rotate until the decoration is in register with male and female tooling that closes on the can. The tooling debosses 40 bubbles and three diagonal splashes in the sidewall of the can, giving it a highly tactile quality. "Consumers constantly challenge us to be special and innovative," says Coca-Cola USA president Jack Stahl. "The cutting-edge quality of [this] can is a natural fit for the cool personality of Sprite." This new can-shaping technology, says Alcoa sales manager Steve O'Connor, was developed over the past year "from the ground up." He emphasizes that the two-piece drawn-and-ironed Sprite can is perfectly conventional in terms of coatings, inks and other physical properties. Designing equipment that would accept a conventional aluminum can was, he says, "the difficult part of this development." Fed by air conveyors, the Alcoa machine at ANC's Kent plant is located between the inside bake oven, which dries the can's inner lacquer, and the necking equipment. O'Connor says it's a prototype, and he isn't revealing its operating speeds. But Alcoa's aim, he says, is to build equipment capable of keeping pace with today's U.S. can lines. That means up to 2귔 cans/min. Coke isn't commenting on the upcharge on the Sprite can compared to straightwall versions. The debossed cans will come in 12- and 24-count Duodozen® multipacks, from Mead (Atlanta, GA), that are converted from 18- and 24-pt Mead CNK® board. Printing is done flexo in five colors. Like the multipacks developed for the curvy Coke can, these have special side cutouts to let consumers feel the cans. Elsewhere in the Coke empire, POWERaDE noncarbonated sports drink hot-filled into a 24-oz polyethylene terephthalate bottle has a brand new closure that replaces the popular and increasingly ubiquitous push/pull sports cap. Rolling out nationwide beginning last month, it's described by Coke as a "revolutionary new closure" that permits the liquid to flow faster while it prevents spillage. At press time, the identity of the closure maker was not available from Coke. But industry sources confirm the 33-mm, injection-molded, polypropylene, hinged, flip-top closure is the SimpliSqueeze® from Seaquist (Mukwonago, WI). It uses a diaphragm-type valve made of silicone that cuts off product flow and reseals without leaking. It's been popular for soaps, lotions, and other products in the health and beauty aids category, but this application in the beverage industry represents something of a breakthrough. On the bottle's label, Coke touts the unique dispensing closure as the "New Powerflo."