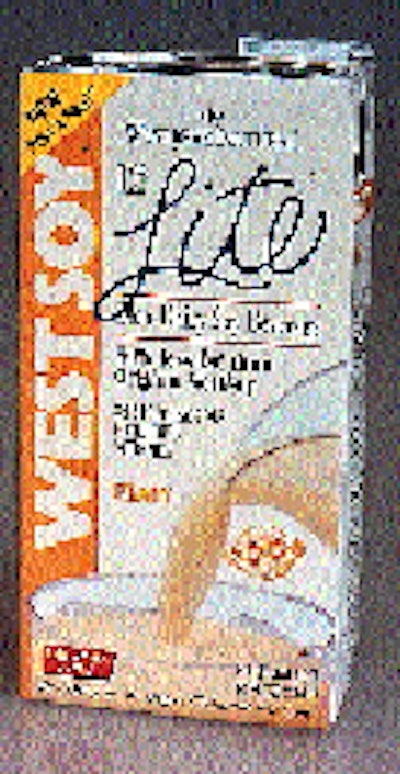
Low-acid dairy and dairy-type products in aseptic packages have been available for some time in pint, quart and 1-L sizes. But with the July launch of four rice- or soy-based beverages aimed at people who are lactose-intolerant, Westbrae Natural Foods of Carson, CA, became the first to market low-acid beverages in 1/2-gal aseptic packages.
"Listening to our customers makes Westbrae a leader in the industry, and when they said they wanted a larger package, we listened," explains president Andrew Jacobson. The 1/2-gal containers now complement Westbrae's quart-sized aseptic offerings of the same products. The larger unit brings consumers about a 50¢ savings compared to what they'd pay for two quarts, says Jacobson. Selling price on the 1/2-gal, he adds, is in the $3.00 to $3.50 range.
The new packages are produced on a Model cf405al-21 system from Combibloc (Columbus, OH). "We've been following this piece of equipment for awhile," says Jacobson. "When Farmland installed it, we jumped all over it, because we feel it's very important."
The installation Jacobson refers to is at Farmland Dairies of Wallington, NJ, the firm that installed the Combibloc system earlier this year (see Packaging World, Dec. '95, p. 57). Farmland copacks Westbrae's 1/2-gal aseptic cartons.
During a recent tour of the Farmland facility, president Marc Goldman told PW how a former knitting mill adjacent to the dairy was acquired, gutted, and fitted with not one but two brand new aseptic lines. Right next to the Combibloc 1/2-gal system is a Combibloc 507 for smaller containers. As soon as the necessary filings with the U.S. Food and Drug Administration are complete, the 507 will swing into commercial production, too. While previous equipment from Combibloc peaked at 83 qts/min, the 507 is rated at 116.
The processing side of Farmland's new aseptic operation was supplied by Schmidt-Bretten (Bohemia, NY). But it was modified by Farmland in ways the firm considers proprietary.
Processing basically unchanged
Already in place when the new aseptic packaging equipment was installed, the Schmidt-Bretten processor has been used by Farmland for several years now to package dairy products in gabletop cartons having extended shelf life under refrigeration thanks to ultra high temperature processing. According to Goldman, the processor required only minor modifications to make the switch from UHT/ESL status to fully aseptic. "What you really need is more data from the system to be able to document that you are meeting FDA requirements for aseptic packaging," says Goldman.
Though processing for aseptic packaging differs only modestly from ESL processing, the 12-month shelf life Farmland gets on its aseptic pack is a huge advantage.
"For those in the dairy business, shelf stability is something of a novelty," says Goldman. He finds it particularly exciting because it means no longer being limited by traditional shelf placement. "You can sell these cartons in a gas station," he says.
As PW goes to press, Farmland is preparing to launch its Skim Plus® brand in the 1/2-gal aseptic package. A skim milk that's fortified with nonfat milk solids to taste more like whole milk, Skim Plus is currently available in a UHT/ESL gabletop carton. That won't change, says Goldman.
"We don't see the aseptic package replacing the gabletop," says Goldman. "The idea is to make Skim Plus more available to more consumers." The aseptic carton's shelf stability will allow Farmland to do just that.
Goldman acknowledges that Skim Plus in the aseptic package will carry an upcharge, but he says it will be modest. He also envisions a day not too far off when it won't be just value-added products--like Westbrae's line and his own Skim Plus line--that are marketed in aseptic packaging, but "regular," high-volume products like whole milk, 2%, and 1% varieties.
Sterilization techniques
Like other Combibloc systems used to fill smaller sizes, the 1/2-gal low-acid aseptic filling system takes preformed carton blanks, forms and sterilizes them with heat and hydrogen peroxide, and then fills and seals them aseptically. The foil/paperboard blanks are supplied by Combibloc.
The key challenge in making the leap from liters or quarts to half gallons was finding a way to sterilize the larger internal volume without sacrificing machine speed. So Combibloc engineers conducted extensive research on different combinations of sterilization techniques.
"Delivery of hydrogen peroxide didn't change from the standpoint of the reservoir that holds the liquid or the method by which it goes to the measuring block," says Rich Biziak, processing engineering manager at Combibloc. "Nor did the spray nozzles or the hydrogen peroxide heaters change much. What did change is the pattern used to flow hydrogen peroxide into the container."
In other Combibloc systems, Biziak explains, there are four stations in which the hydrogen peroxide is delivered. Also, a hot air station comes between the second and third dosing stations.
"For this machine," says Biziak, "it was determined that sterilization is best accomplished by injecting the complete shot of hydrogen peroxide in one station."
The intermittent-motion se-quence begins with liquid hydrogen peroxide flowing to a measuring block. Next it flows to a nozzle, where it is mixed with filtered compressed air and heated by a tubular heater to about 210°C (410°F) and sprayed into the carton. In the next station nothing at all happens. It's basically an opportunity for the hydrogen peroxide to react on the inside of the container.
Then the container moves into the drying zone. It stops beneath each of four nozzles that blow hot sterile air inside. Registering again in the 210°C range, the hot air completes the sterilization process and causes residual hydrogen peroxide to evaporate. The net result is a bacteria kill rate meeting all FDA guidelines.
Improved control system
One other point of differentiation between this machine and previous Combibloc versions revolves around the control system. It's an open architecture system in which the PLC, the IBM-compatible computer, the filling system, and the temperature control system all talk to each other over the same network. This means that operator functions that had to be split across different PLCs and controllers in the past are now performed at one operator control panel. Temperature set points for various heaters, for instance, were entered through a separate controller in past systems. The Farmland system allows the operator to enter these set points at the operator panel. They are transferred to the temperature controller automatically.
Filling is done two-up. The rated speed of the system is 5ꯠ units/hr (83/min), and according to Goldman, those speeds were indeed being achieved shortly after installation was complete.
In each lane, blanks are opened by vacuum cups and pulled down over a mandrel. The mandrel rotates 600 and hot air heats the bottom of the package. After tucker arms tuck the flaps in, a bottom pressing station comes up and completes bottom forming. The carton then drops bottom first into a pocket conveyor that carries it through the rest of the process.
After a "dedusting" station in which sterile air is blown in and vacuumed out, the carton enters the aseptic zone, which is overpressured by a sterile air flow. Filling is performed in two stages, which makes it possible to propel the liquid at high velocity yet minimize foaming. After the second stage, a defoamer removes foam prior to top sealing, which is done ultrasonically.
At this point the carton leaves the aseptic zone. The top is heated so that the flaps can be folded down and heat-sealed against the side panels. Cartons then exit by way of a paddle wheel that deposits them on a discharge conveyor leading past a Videojet (Wood Dale, IL) ink-jet coder. It imprints date and time of packaging on each carton top.
Right after coding, cartons are conveyed out of the filling room, which has special air cooling and filtering systems that maintain positive pressure and minimize contamination from ambient atmosphere. The next piece of equipment in the line is a vertical accumulator from Hartness (Greenville, SC). Capable of holding some 600 cartons, it allows Farmland to keep the aseptic filler running steadily for up to seven or eight minutes if some downline machine needs to be stopped.
A short distance from the Hartness accumulator is a Combibloc machine that automatically applies the combiTop® pour spout (see sidebar). The final step in the packaging line is secondary packaging, executed by a wraparound traypacker from Meurer (Fuerstenua, Germany). It wraps cartons in either a full-height open-top tray that then gets sent through a Meurer shrink film applicator or it packs them in a full wraparound case requiring no wrap.
One look at the new side-by-side aseptic lines in their clean-room home tells even the casual observer that they represent a sizeable capital investment. But Goldman sees it paying big dividends.
"This kind of packaging offers real advantages," he says, "in distribution, in where you can display the product, and in convenience to consumers who can now store unopened milk without refrigeration. We feel good about these lines, so we made a significant investment to do it right."