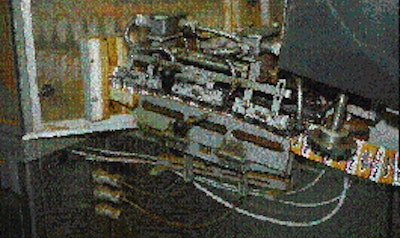
It's no secret that the taste for Latin-style food is growing in the U.S. So when Miami-based Packaging Ltd. a Goya Foods company upgraded the 5- and 10-g pouch-packaging operation for Goya's Latin-inspired powdered seasonings and bouillons management looked for equipment that could keep pace with that demand.
The end result is a line that runs at 540 pouches/min. That compares with about 190/min on the line used previously for these products a line located in a Puerto Rican plant now closed. Accuracy is greatly improved as well.
"I'd say weight control is 70% better" says plant manager Manuel Villapol. It's important not only because the manufacturer doesn't want to give away product in overweight packages. "An underweight package rejected by the checkweigher also means wasted product materials and time" says Villapol.
Primary packaging is accomplished by a Cloud RCM continuous-motion pouch packager from Klockner Bartelt (Sarasota FL). Cartoning is also done on a Klockner Bartelt system and the line ends with a two-piece tray packer from Schneider (Brewerton NY).
One of the most serious shortcomings of the previous packaging operation was that it was forced to run at absolute maximum capacity. That meant that if special product promotions weren't scheduled with the utmost care running out of stock was a very real possibility.
"Running out of stock is a cardinal sin under normal circumstances but during a promotion it's even worse" says product manager Frank Unanue. "The new line has simplified our lives in terms of how we run promotions. Product availability is always there and we can meet our deadlines easily."
Making the new line all the more welcome says Villapol is its relatively small footprint. The space it occupies had to be carved out of existing warehouse space and the firm was able to keep it under 2 sq ft. The area is also walled off for better control of temperature and relative humidity key concerns in packaging hygroscopic products like these.
Dual-auger filling
Outside the packaging room products are mixed and put into portable totes that are moved by forklift to the hopper that feeds the Cloud RCM's dual-auger filler. Roll-fed pouch material a paper/foil/polyethylene lamination from several suppliers is fed over a forming plow that folds the material in half. A sensor at the plow detects eye marks on the printed material to keep it in register.
Next the web travels around a vertical sealing drum for side sealing into a strip of individual pouches. The stainless steel drum is equipped with vertical "lands" or strips of metal protruding about 1/4" from the drum itself. These lands are heated so when the two-ply material is pinched between a heated land and a pair of rubber rollers the vertical side seals are made.
Now the side-sealed pouches are ready for the rotary filling turret. The vertical seals are positioned against registered lands and a vacuum cup opens each pouch from the rear so that the widest possible opening can be offered to the filling funnel.
Product is delivered to the pouches by 48 funnels continuously rotating past a Klockner Bartelt servo-driven dual-auger filler. In turn the augers are constantly flooded with product by an agitation system leading to a bulk hopper capable of holding about eight hours worth of product.
Filling is done volumetrically as the amount of product dispensed into each funnel and then into the pouch beneath it is a function of how many turns the auger screw makes. A single auger would have been capable of delivering sufficient product to meet Goya's needs but greater accuracy is gained by dividing the flow into two.
Independent servo drives
Each auger has its own servo drive so it's independent of the rest of the machine. According to Klockner's Dennis Calamusa this adds operational flexibility and reduces maintenance.
"Traditionally augers like this have relied on electromechanical clutch brake mechanisms" says Calamusa. "That means you're faced with the wear and tear inherent in that kind of operation. Here each auger has an independent servo head. It virtually eliminates maintenance and makes it easy to ramp up and down in speeds."
The filling turret is mounted in such a way that it makes a slight dip at one end of its revolution. This causes the filler funnels to dip down into the pouch just at the point where they're releasing their load of product. Consequently the product is dropped well below the seal area which means less chance of product in the seal area. This results in more secure seals.
Filled pouches still in their continuous web are drawn through a top seal mechanism by two downstream power rollers. Constant tension is maintained during this continuous-motion heal-seal process to eliminate wrinkles in the seals. Once the top seal is made the web of pouches is routed to a rotary knife/collation station. This step cuts the pouches into pairs perforated in the middle and collates the pairs in the proper stack counts. These stacks are then dropped into a flighted conveyor that takes them to the product infeed of a Klockner Bartelt IMC/S intermittent cartoner.
The cartoner has independent servo drives for each of its primary functions including the main drive infeed conveyor carton setup and product insertion. As with the rotary filler the servo drives mean greater flexibility than if all functions were tied into the line shaft of the machine. For example in the loading area one carton requires a double load of pouches. One stack must be pushed deep into the carton and then the loading arm comes out and loads a second stack though this time with a shorter stroke. Setting up the cartoner to accommodate this particular handling characteristic is greatly simplified when the loading function is driven by its own servo.
Carton loads vary
Cartons are erected and advanced independently to the load station via a carton transfer system. When sensing devices verify that both carton and product pouches are available the servo-driven loader inserts the pouches into the carton. For cartons holding eight or 12 pouches a single load stroke is used. For the 20-count carton a stack of 10 pouches is inserted into the rear of the carton first then a second stack is inserted after it.
Filled cartons are conveyed past a Nordson (Duluth GA) glue system that applies hot melt to the flaps before a compression system closes them. An ink jet printer from Videojet Systems (Wood Dale IL) prints lot number and date on each carton; the imprinter can also be programmed to print promotional information.
Next in line is a Garvens checkweigher available through Hi-Speed Checkweigher (Ithaca NY) that includes a statistical feature to track and print out weight variations. Once past the checkweigher the cartons are conveyed to the collating station of the Schneider two-piece tray packer Model TPTL.
Lying flat on their back panels the cartons are admitted into the collating station in predetermined amounts. For instance if a tray of 24 is in production each time three cartons are indexed in they get "upstacked" to make room for the next three beneath them. This happens eight times. Then the collating unit flips from its 12 o'clock position to a 3 o'clock position which means the cartons now are standing on their bottom flaps in a 3 x 8 pack pattern. A pusher arm pushes them into the display tray which has been picked from a 240-blank magazine and set up in a flighted conveyor. This conveyor cycles forward moving the loaded tray into a folding and hot melt gluing station.
At this point the display tray is complete. It now continues in the same direction until it's positioned beneath a magazine-fed corrugated lid. The tray is pushed up into the flat lid and the lid is formed around the tray. Hot melt glue seals the flaps of the lid. Then the lidded tray is discharged at a right angle through a taping head that secures the lid to the tray. The finished trays are conveyed out of the packaging room which is manned by only one operator and are manually palletized. A Lantech (Louisville KY) stretch wrapper brings the packaging operation to an end.
Now in production for about one year the line typically runs two shifts five days a week. Its output serves markets in Puerto Rico as well as the U.S. Product changeovers are kept to a minimum and in fact it's usually two or three weeks before such a change is made. Switching to a new pouch size however happens more frequently and according to Villapol it only takes about 30 minutes to go from a 5-g to a 10-g pouch or vice versa.
The line has been such a success that the firm has ordered two more just like it. At the heart of each will be the Klockner/Cloud pouch packager. The decision to purchase them was a bit easier for Villapol than the first time when he knew relatively little about the Cloud system.
"You always worry when you switch to something new" says Villapol. "We were unfamiliar with the technology of the Cloud machine but we trusted Klckner and they recommended the Cloud packager."
At this point he's glad they did. "For all its speed it's a simply engineered machine" he concludes.